Réparation de machines-outils : travaux courants et capitaux. Réparation de machines-outils : différences entre courant et capital
La deuxième partie du manuel contient des travaux types et des normes pour la fréquence, la durée et l'intensité de la main-d'œuvre de l'entretien et de la réparation des principaux types d'équipements industriels généraux: machines à couper les métaux, équipements pour le travail du bois, équipements de forgeage et de pressage, presses hydrauliques spéciales, fonderie matériel de four électrique, matériel de levage et de transport, matériel de compresseur et de pompage, matériel de ventilation et de climatisation, matériel de concassage et de broyage, matériel roulant transport routier, construction de routes et machines agricoles.
Des recommandations sur la composition des opérations de réparation et de prévention sont élaborées en tenant compte des recommandations des fabricants et de la réglementation en vigueur dans les entreprises de diverses industries et zones de production. Les valeurs numériques des normes de fréquence, de durée et d'intensité de travail de l'entretien et des réparations sont considérées comme des moyennes pondérées pour les entreprises opérant dans des conditions normales pour la production d'entretien et de maintenance préventive.
7. ÉQUIPEMENT DE COUPE, DE TRAVAIL DU BOIS ET DE PRESSAGE DES MÉTAUX
Les équipements de coupe des métaux, de travail du bois et de forgeage et de pressage sur le lieu d'utilisation sont principalement concentrés dans les ateliers (zones) de réparation mécanique et mécanique des entreprises ayant des conditions d'exploitation similaires. La réparation et la maintenance préventive de ces types d'équipements sont également assez courantes, il est donc conseillé de les considérer dans une seule section.
Les machines-outils et les machines pour le travail des métaux, la coupe des métaux (groupe de tournage, groupe de perçage et d'alésage, taillage d'engrenages, fraisage, rabotage et rainurage, rainurage de boulons, machines de coupe, spéciales et spécialisées) sont affectées au septième groupe d'amortissement avec une période utilisation bénéfique plus de 15 à 20 ans inclus.
Les machines-outils et machines pour le forgeage et l'emboutissage des métaux (presses mécaniques, presses hydrauliques, presses à forger automatiques, marteaux, machines et cylindres à forger, redresseuses plieuses, cisailles) appartiennent au sixième groupe d'amortissement avec une durée d'utilité supérieure à 10 à 15 ans inclus .
Les machines à bois (rabotage, fraisage, tenonnage, meulage, polissage, perçage, rainurage et rainurage) appartiennent également au sixième groupe d'amortissement avec une durée d'utilité supérieure à 10 ans à 15 ans inclus.
Les machines à travailler les métaux d'autres groupes, y compris le traitement à la flamme gazeuse, le revêtement métallique, la projection thermique, les systèmes de production flexibles (robots) appartiennent au troisième groupe d'amortissement avec une durée de vie de plus de 3 à 5 ans inclus. Le même groupe comprend les scies circulaires, les scies à ruban et les scies sauteuses.
7.1. Maintenance
7.1.1. Une gamme typique d'opérations d'entretien pour les équipements de coupe des métaux, de travail du bois et de forgeage et de pressage est présentée dans le tableau. 7.1.
Tableau 7.1
Une gamme typique de travaux d'entretien par types d'équipements de coupe des métaux, de travail du bois et de forgeage est donnée dans le tableau. 7.2.
Tableau 7.2
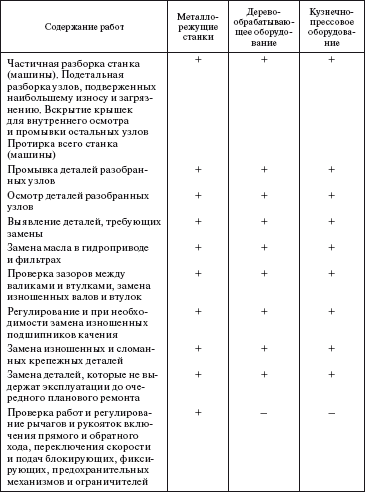

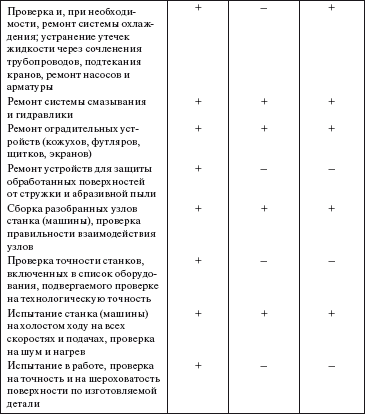
7.3. Révision
Table 7.3.


7.4. Normes de fréquence, de durée et de complexité des réparations
Les normes relatives à la fréquence, à la durée et à la complexité de la réparation des équipements de coupe des métaux, de travail du bois, de forgeage et de pressage sont indiquées dans le tableau. 7.4.
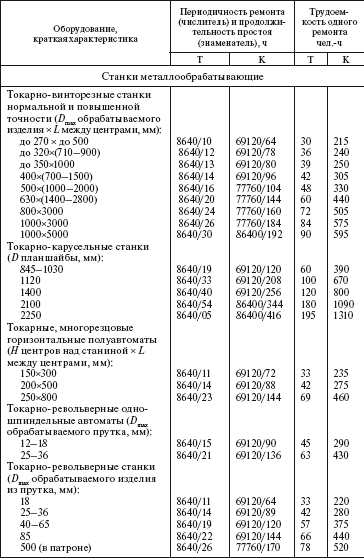
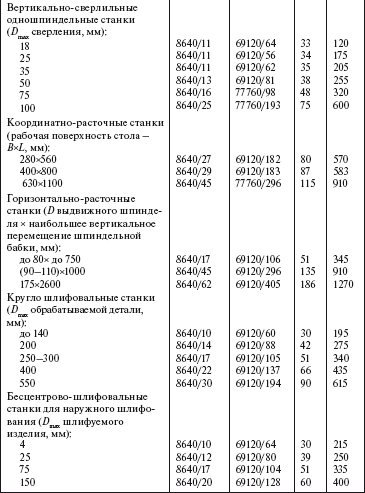


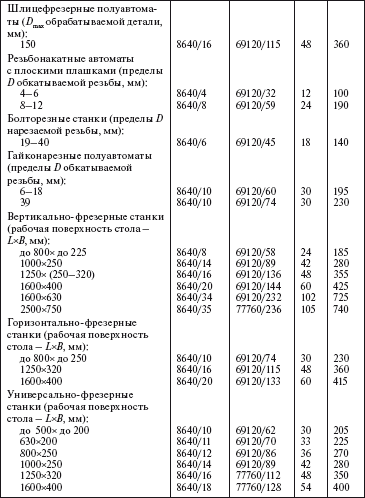
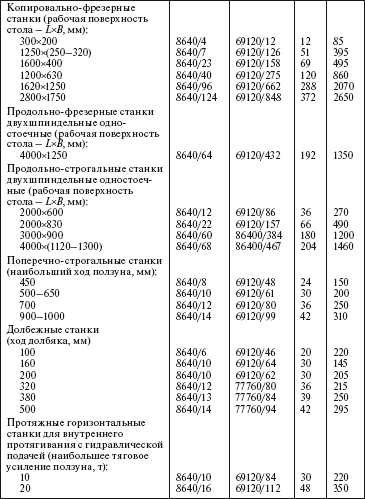


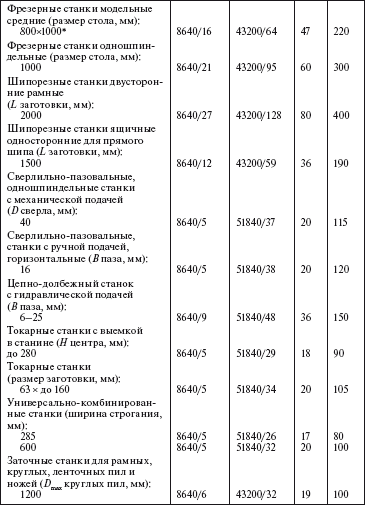
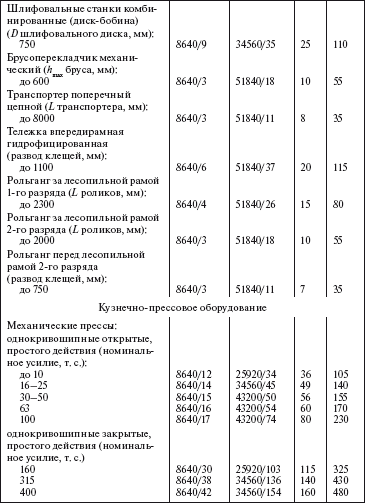

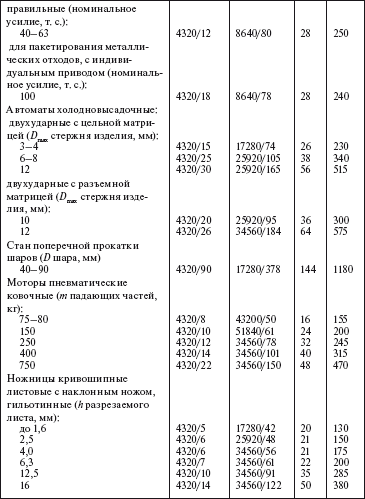

* Pour les machines semi-automatiques, la complexité de la révision augmente de 35 %.
8. ÉQUIPEMENT FOUR ÉLECTRIQUE DE FONDERIE
La rubrique comprend les équipements de fonderie suivants : fours électriques, fours électriques et mécanismes, qui appartiennent au cinquième groupe d'amortissement avec une durée d'utilité supérieure à 7 à 10 ans inclus.
8.1. Maintenance
La maintenance des fours électriques, des fours électriques et des équipements est effectuée conformément aux exigences de la documentation technique des fabricants dans le cadre d'un processus de maintenance non planifiée.
La liste des opérations typiques pour chaque groupe d'équipements est indiquée dans le PTE de l'entreprise. Liste indicative les opérations de maintenance typiques par nom d'équipement sont données ci-dessous.
8.1.1. Robinets. Nettoyer les surfaces de travail du mélangeur du mélange et de la saleté. Soufflage d'air de la traverse, dispositif de débridage, boîtes de vitesses, dispositif de contrôle du moulage du mélange, panneau de commande. Contrôle : état des bennes, des racleurs, des charrues et des goupilles des rouleaux, si nécessaire - réglage, remplacement. Vérification de l'état des couvercles de protection, des protections, des limiteurs, etc. Vérification du fonctionnement du mélangeur et des boîtes de vitesses pour le bruit et les vibrations. Contrôle et réglage de la tension des courroies. Vérification de l'état et du fonctionnement de l'embrayage, des électroaimants. Vérification du niveau d'huile dans les boîtes de vitesses ; réapprovisionnement si nécessaire. Serrage des fixations et remplacement des pièces défectueuses usées des bennes, des racleurs, des charrues, des chemises, des goupilles et des chemises en caoutchouc des accouplements, des bagues, des essieux, des tiges, des arbres, des goujons, des écrous, des vis, etc. Inspection et élimination des fuites dans les cylindres, les boîtes de vitesses, dans un réservoir de mesure, dans la vanne d'arrêt, les graisseurs, les canalisations et les équipements pneumatiques. Nettoyage des entailles, rayures, éraflures et bavures. Contrôle du travail et réglage : mécanisme de chargement des composants secs et humides ; mécanisme de déchargement et d'échantillonnage du mélange ; mécanisme d'ouverture et de fermeture des trappes de déchargement, dispositifs de chargement et de dosage; cylindres pneumatiques; systèmes de ventilation; dispositif de moulage par mélange ; dispositifs de système de lubrification; limiteurs, interrupteurs et arrêts; entraînements par courroie trapézoïdale ; dispositifs de protection conformes aux exigences de sécurité. Ajustement des écarts entre le fond du bol et le bord inférieur de la lame; entre le bord latéral du racleur du socle et le revêtement du socle (pour les mélangeurs à rouleaux à rotation verticale).
8.1.2. Machines de formage. Vérification et serrage des fixations des mécanismes soumis à des vibrations et à des chocs. Réapprovisionnement des modèles de réservoirs de pulvérisation avec un agent de démoulage. Vérification du dysfonctionnement des capots de protection, des clôtures, des limiteurs. Réglage du mécanisme d'extraction. Vérification de la fixation et du fonctionnement des électroaimants, de l'état des modèles, des douilles, des goupilles, des surfaces de travail des flacons. Vérification et serrage des fixations des cylindres et des pistons, des traverses et des patins de presse, des cadres de brochage et des fontes de levage, des supports, des plateaux tournants, des culbuteurs, des arbres. Vérification du travail : mécanisme d'agitation pour la fréquence des battements par minute, la hauteur de la table ; mécanisme de presse pour la force de pression ; mécanisme d'orientation pour la fiabilité et la vitesse de rotation. Vérification de l'état des connexions des éléments du système pneumatique : vérins et équipements de contrôle ; distributeurs d'air et vannes, tuyaux et flexibles; équipements de contrôle et organes exécutifs. Vérification du fonctionnement et du réglage des mécanismes de rotation de la traverse et du racleur, des pinces du ballon, des vibrateurs. Vérification du fonctionnement du mécanisme de rotation de la table, des crémaillères, des boucles d'oreilles, des leviers, des goupilles et du vérin pneumatique. Remplacement des pièces usées et cassées. Vérification de l'état de fonctionnement des limiteurs, interrupteurs, vannes, arrêts, etc. Lors des vérifications, les réglages nécessaires sont effectués, prévus par le manuel d'utilisation et les spécifications techniques de la machine contrôlée. Vérification de l'état de l'ensemble du système hydraulique et des dispositifs de graissage : présence d'huile dans les réservoirs, les graisseurs, les graisseurs à bouchon et goutte à goutte et autres points de graissage. Élimination des fuites; réglage de l'alimentation en huile des surfaces frottantes des mécanismes.
8.1.3. Machines à barres. Nettoyage de la saleté et de l'huile de toutes les unités et mécanismes de la machine. Inspection externe de l'absence de pannes et de fuites dans les équipements hydrauliques et pneumatiques, le système de refroidissement par eau et le système de chauffage au gaz avec élimination des défauts identifiés ; évacuation des condensats des déshumidificateurs. Vérification de l'état des interrupteurs de fin de course, leur réglage et dépannage. Vérification de l'état de l'équipement de base. Vérification et serrage des fixations soumises à des vibrations et à des charges périodiques. Vérification de l'état des protections et capots de protection, dépannage. Réglage du travail des dispositifs de serrage, des pilonneuses et des pinces. Vérification de l'état : des joints du manchon de sablage, du dispositif de grille et de la buse de sablage ; diaphragmes des soupapes d'admission et d'échappement ; éléments de commande (interrupteurs, boutons de commande, lampes de signalisation, etc.); parties du dispositif de porte, vannes de soufflage et d'échappement, alimentateur vibrant. Vérification du niveau d'huile dans les réservoirs, réservoirs et autres contenants ; vérification de la présence d'huile dans les distributeurs d'huile et les lubrificateurs goutte à goutte et de lubrifiant dans les lubrificateurs à capuchon ; vérifier le débit d'huile vers la destination. Contrôle de l'état : systèmes de chauffage au gaz pour les boîtes à noyaux, systèmes de chauffage électrique pour les boîtes à noyaux ; radiateurs électriques tubulaires; système pyrométrique pour surveiller et maintenir la température prédéterminée de chauffage de la boîte à noyaux. Vérification et serrage des fixations dans les dispositifs de serrage, les pinces, les chaînes de convoyeurs à rouleaux. Vérifier la taille des fentes du manchon de sablage et le remplacer si les fentes sont supérieures à 0,5 mm. Vérification de l'état des surfaces de la porte et de la plaque gonflable ; en présence d'entailles, d'éraflures, de rayures d'une profondeur de 0,3 mm ou plus, remplacer ou réparer. Inspection et vérification de l'état des rouleaux et de leur fixation sur les tables à rouleaux ; remplacement des rouleaux présentant des défauts (usure sur le périmètre, excentricité, etc.). Vérification et serrage des connexions boulonnées, remplacement des fixations desserrées ou usées. Vérification de l'état des cylindres, des tiges, des raccords à bride et des autres pièces du système pneumohydraulique pouvant être inspectées visuellement. Vérification du fonctionnement de la sécurité et appareils automatiques. Identification des défauts qui doivent être éliminés lors de la prochaine réparation planifiée.
8.1.4. Grilles défonçables. Vérifiez l'état du lecteur. Vérifier : l'état des supports élastiques et des fixations du vibrateur ; températures de chauffage des logements de roulement ; resserrer la fixation de l'âme des sections de grille de la grille ; niveau d'huile (pour les bains liquides) dans l'excitateur de vibrations ; serrage de toutes les fixations. Remplacement des fixations usées. Vérification de l'état et de la soudure de l'âme des sections de grille et du corps de grille. Vérification de l'état : câblage électrique ; roulements et arbres. S'il y a des fuites d'huile, remplacez les joints et les joints.
8.1.5. Lanceurs de sable. Nettoyage de la saleté, du mélange et de l'huile. Vérification de la fixation du godet et de l'arc. Vérification de l'écart entre le bord supérieur du godet et l'arc. Lors de l'installation d'un nouveau godet, l'écart ne doit pas dépasser 0,5 à 0,7 mm. Vérification de la tension des entraînements par courroie trapézoïdale, du câble des mécanismes d'alimentation et de la chaîne d'entraînement de la courroie d'alimentation. Vérification des travaux : mécanismes de déplacement du chariot et du pont (pour lanceurs de sable de type pont) ; mécanismes pour tourner les grandes et petites manches, systèmes hydrauliques; têtes (au ralenti); bon fonctionnement du chariot du mécanisme d'alimentation. Vérification et serrage des fixations du rotor de la tête de lancement. Nettoyage des fosses du sable de moulage et lubrification des engrenages ouverts. Vérification du fonctionnement de la tête de sablage avec les manchons étendus sur une ligne, ainsi que lorsque l'axe du petit manchon est situé à un angle de 90 ° par rapport au grand manchon (l'affaissement ne doit pas dépasser 5 mm). Vérification de la verticalité des axes de rotation des grandes et petites manches. Vérification de l'état des éléments de l'articulation du petit manchon du lanceur de sable avec un grand et un grand manchon à axe de rotation central. Vérification des angles de rotation des grandes et petites manches. Vérification du système de lubrification : quantité et état de l'huile dans les boîtes de vitesses ; alimentation en huile de tous les points de lubrification conformément au passeport du véhicule ; la présence de lubrification dans les ensembles de roulements. Vérification de l'état des engrenages ouverts. Vérification du fonctionnement des dispositifs automatiques et de sécurité. Vérification et réglage des accouplements et dispositifs de freinage. Vérification de l'état des fondations et des boulons de fondation. Vérification de l'état des bandes transporteuses.
8.1.6. Vérification du bon réglage du séparateur. Vérification du fonctionnement des portes et de l'interrupteur de fin de course du treuil de benne. Vérification de l'état de la broche de la roue, des pièces d'usure. Vérifiez l'éventuel colmatage du système de circulation de la grenaille aux endroits des vannes, du tuyau de dérivation, la présence de gros morceaux de métal sur le séparateur à tamis à tambour. Inspection et vérification de l'état des composants et des mécanismes : grenailleuse, convoyeurs à plaques et à vis, séparateur, élévateurs, monte-charge, portes, volets de grenaille. Vérification de l'état des soudures. Vérification de l'état du revêtement de protection de la chambre du disque d'extrémité et de la porte. En cas d'usure extrême, un remplacement partiel ou une réparation est effectué. Vérification des joints du système de circulation de la grenaille afin d'éliminer les fuites de grenaille. Vérification du fonctionnement du système d'extraction des poussières. Vérification et serrage des raccords amovibles des canalisations pour éliminer les fuites d'air. Vérification de l'état et remplacement des pièces d'usure de la grenailleuse. Vérification de l'état de la courroie ou des chaînes de l'élévateur à godets. Vérification de l'état des mangeoires et du tamis à tambour du séparateur, changement de maille. Vérification du fonctionnement des mécanismes de rotation de la table, des plaques de déplacement du chariot et du palan à benne. Contrôle et réglage de la tension des entraînements par chaîne et courroie trapézoïdale. Vérification de l'état de fonctionnement du système de lubrification, vérification de la quantité d'huile dans les boîtes de vitesses et de la qualité de l'alimentation en huile de tous les points de lubrification selon la carte de lubrification. Réglage des roulements, vérification des joints et remplacement des joints et joints usés. Vérification de l'état : des dispositifs de protection ; organes directeurs. Vérification du fonctionnement des dispositifs automatiques et de sécurité. Identification des défauts qui doivent être éliminés lors de la prochaine réparation planifiée.
8.1.7. Machines de moulage par injection. Nettoyer la surface de la machine des éclaboussures de métal et de la saleté. Vérification de l'état du système hydraulique (les fuites sont inacceptables). Vérification de l'état du système de lubrification. Vérification de la force de verrouillage. Vérification du fonctionnement du système de chauffage et de refroidissement. Contrôle du serrage des fixations des couvercles, des brides et de toutes les connexions du système hydraulique. Portez une attention particulière aux joints situés près des fours et du moule. Serrage des fixations, remplacement des pièces usées et cassées pour les flexibles de fixation, traverse à la tige du vérin hydraulique, traverse fixe au banc de la machine, barres transversales du piston presseur, moteur électrique et pompe, tiges de fin de course. Vérification de l'état des connexions des éléments hydrauliques. Vérification de la présence d'huile à tous les points de frottement des joints. Ajustement des éléments du système hydraulique: élimination des fuites, en présence de vibrations de la canalisation, resserrement de la fixation des canalisations ou fixation avec des attaches supplémentaires; s'il y a de la mousse d'huile ou des vibrations de la pompe, vérifiez la conduite d'aspiration de la pompe hydraulique. Réalisation d'analyses en laboratoire de la qualité des huiles pour le respect des indicateurs physiques et chimiques du passeport. Vérification et réglage des soupapes de soupape (avec une révision complète des vannes d'arrêt du système d'alimentation en azote). Démontage et lavage du filtre. S'il y a des sédiments dans le réservoir hydraulique, rincer la surface intérieure des réservoirs, accumulateurs, canalisations, unité d'injection. Vérification du fonctionnement du système de chauffage et de refroidissement au mazout (le chauffage autorisé ne dépasse pas 50 ° C). Vérification de l'étanchéité des joints d'étanchéité, des manchettes, des genoux et des autres joints d'étanchéité. Vérification de l'instrumentation (manomètres, pressostats, etc.), ainsi que des équipements électriques (relais temporisés, automates, etc.). Vérification de l'état du système de refroidissement du moule et du piston de pressage. Inspection externe de l'absence d'éraflures, d'entailles, de bosses, d'usure sur les colonnes de guidage, les glissières, les tiges, les éléments du mécanisme de verrouillage. Vérification de la concentricité de la coupelle et du piston. Changement de pièces d'usure ; piston, télescopes, verre, douille de coulée et autres pièces défectueuses. Vérification et réglage de la douceur de roulement (absence d'à-coups, de chocs et de blocages). Vérification de l'état de fonctionnement des limiteurs, des butées, des dispositifs de sécurité, des clôtures, du bouclier de sécurité. Vérification de l'état des organes de commande de fonctionnement de la machine : poignées, tringles, leviers, boutons, etc. Vérification de la résistance de mise à la terre de la machine. Vérification du parallélisme des traverses mobiles et fixes.
8.1.8. Machines de refroidissement. Nettoyer la surface des machines des éclaboussures de métal et de la saleté. Inspection et vérification de l'état des mécanismes, remplacement des pièces défectueuses. Vérification et serrage des supports de la machine ; remplacement des fixations desserrées, usées et défectueuses. Vérification de l'état du réseau d'alimentation de la machine avec le fluide de travail, serrage des connexions de la canalisation. Soupape et réglage des soupapes. Vérification du système de lubrification (vérification de l'alimentation en huile de tous les points de lubrification selon la carte de lubrification). Vérification de l'état de la surface des rouleaux. Vérification de l'état d'usure de la surface des rouleaux à pâtisserie, des rails, des tiges, des poussoirs, des raccords à bride. Vérification de l'état des surfaces des tiges. Réglage des tiges reliées aux vérins hydrauliques pour déplacer les tiges et la palette mobile. Vérification de l'état des ressorts. Vérification de la rotation du disque dans le mécanisme d'éjection. Vérification du fonctionnement des charnières, des galets, du levier de rappel de l'éjecteur. Goupilles et douilles pivotantes de rechange. Vérification de l'état des joints : bagues d'étanchéité, joints, manchettes, bagues et autres pièces. Changement des pièces d'usure : coussinets, chemises, etc. Vérification de l'état des dispositifs du système de commande de la machine : pédales, poignées, tiges, leviers, boutons, etc. Vérification de l'état, réparation et installation des protections et autres dispositifs pour assurer la sécurité de la machine.
8.1.9. machines centrifuges. Vérification de l'alimentation en huile de lubrification de tous les points du système de lubrification. Vérification des fuites d'air. Contrôle du chauffage : huile dans les réservoirs d'huile (chauffage autorisé pas plus de 50 °C), pompes, roulements du carrousel. Vérification de l'état de fonctionnement des dispositifs de sécurité et de freinage qui assurent la sécurité du travail. Vérification de la présence de bruits et de vibrations parasites lors du fonctionnement des mécanismes causés par un dysfonctionnement des éléments de la machine et de l'entraînement électrique. Vérification de l'état des guides, broche et support, galets presseurs. Soupape et réglage des soupapes. Vérifiez l'alimentation en huile de tous les points de lubrification. Vérification du système de refroidissement par eau. Vérifier l'étanchéité du système hydraulique de l'entraînement pour déplacer la caisse et système commun. Vérification de tous les joints, remplacement des manchettes, des joints. Vérification de l'état des pièces des cylindres pour saper et éjecter les pièces moulées. Vérification de l'état de fonctionnement des limiteurs, des arrêts, des fusibles. Vérifier l'état, réparer et installer des protections et autres dispositifs pour assurer la sécurité de la machine.
8.2. Maintenance
Pendant la réparation en cours, les opérations de maintenance et ci-dessous sont effectuées travaux suivants par types de voitures.
8.2.1. Robinets. Démontage de paliers d'arbres horizontaux ou verticaux, lavage et mesure d'usure, nettoyage des bagues et axes d'arbres. Les bagues sont remplacées lorsqu'elles sont usées. Vérification de l'usure des bagues des leviers et des axes des rouleaux. Réglage et, si nécessaire, remplacement des roulements. Vérifier l'usure de la coque et du fond du bol. Remplacement des inserts annulaires dans le fond du bol. Remplacement du rouleau et du revêtement en caoutchouc (pour les mélangeurs centrifuges). Vérification de la fixation de la coque. Remplacement des dépotoirs, des racleurs et des charrues. Remplacement des boulons de réglage et recoupe des filets. Vérification de l'état des supports. Démontage et vérification de l'état des pièces du mécanisme de charge. Démontage, nettoyage des pistons, axes, goupilles, ainsi que le changement des joints spi, joints et de toutes les fixations. Vérification de l'état des pièces des distributeurs à vis. Remplacement des courroies trapézoïdales et vérification des tolérances des rainures des poulies. Le contrôle de l'état et le remplacement des éléments des accouplements. Vérifier : l'état des fixations des bollards et des cadres à la fondation ; l'état de la fondation (si nécessaire - réparation); tous les raccords de conduits d'air ; porter une attention particulière à l'intégrité des tuyaux et à leur fixation, ainsi qu'aux vannes, afin d'éliminer les fuites d'air comprimé du système pneumatique; parallélisme de l'arbre intermédiaire et des arbres de transmission à grande vitesse ; sur l'alignement de l'arbre de sortie de la boîte de vitesses et de l'arbre vertical ; parallélisme des axes de rotation des poulies et déplacement des axes des gorges des poulies. Essai de la machine au ralenti et en charge avec les travaux de réglage nécessaires.
8.2.2. Machines de formage. Démontage et réparation du mécanisme de secouage. Lavage et nettoyage, mesure et détection des défauts des pièces. Remplacement des bagues, ressorts, joints et autres pièces sujettes à usure. Éraflure des pistons et des cylindres avec meulage ultérieur. Lorsque la table vibrante se déforme, ses surfaces sont rabotées et s'il y a des fissures, un soudage est effectué. Vérification de l'état des boulons d'ancrage du lit et mise à niveau du lit. Inspection et remplacement des pièces d'usure des amortisseurs. Ébavurage et réglage des barres de guidage, des goupilles et des douilles du mécanisme de secouage. Démontage du mécanisme d'échappement avec des pièces défectueuses. Nettoyage des éraflures des pistons et des cylindres.
8.2.3. Machines à barres. Inspection et lavage des citernes et conteneurs ; nettoyer, laver ou remplacer les filtres. Vidange d'huile usagée et remplissage d'huile neuve (si la réparation en cours coïncide avec le calendrier de vidange d'huile). Effectuer des analyses en laboratoire de la qualité de l'huile pour la conformité aux indicateurs physiques et chimiques du passeport. Démontage du mécanisme de levage et de pressage de la boîte à noyaux vers la buse, du mécanisme de soufflage avec vannes d'insufflation et d'échappement, du dispositif de porte, de l'alimentateur vibrant et des autres unités et mécanismes soumis à la plus grande usure ; détection des défauts des pièces, remplacement des pièces usées des unités et mécanismes démontés. Identification des défauts qui doivent être éliminés lors de la révision ultérieure avec une inscription dans la liste préliminaire des défauts. Vérifier la rectitude de la surface de travail des guides (l'écart ne doit pas dépasser 0,2 mm sur une longueur de 1000 mm). Vérifier le parallélisme de la surface de travail du cadre oscillant et de la surface d'appui de la bride de fixation du sablage (1 mm sur une longueur de 1000 mm). Démontage et réparation de vérins pneumohydrauliques avec remplacement des pièces usées, joints et autres produits en caoutchouc.
8.2.4. Lanceurs de sable. Vidange de l'huile, rinçage des réservoirs d'huile et des systèmes hydrauliques. Inspection et nettoyage de l'ensemble de la machine. Démontage de la tête de la sableuse et remplacement des pièces usées. Équilibrage du rotor de la tête de sablage. Vérification de l'état des roues, des freins, des chaînes d'entraînement, de la boîte de vitesses et des autres éléments de montage du chariot du lanceur de sable. Vérification de l'état des mécanismes de rotation des grandes et petites manches. Vérification de la chenille : joints bout à bout, fixations et état de la chenille. Alignement des rails dans un plan horizontal par niveau. Vérifier la bonne connexion des extrémités du ruban et resserrer le ruban si nécessaire. Vérification de la connexion des grands et petits manchons, serrage de la fixation des tiges et du châssis des convoyeurs. Vérification de l'état des équipements hydrauliques, serrage des raccords et des joints. Vérification de l'état de fonctionnement des butées d'arrêt des interrupteurs. Identification des défauts qui doivent être éliminés lors de la prochaine réparation programmée, avec une inscription dans la liste préliminaire des défauts. Test de la machine au ralenti et sous charge.
8.2.5. Grilles défonçables. Vérification de l'état et remplacement des pièces usées de l'excitateur de vibrations. Ajout d'un lubrifiant épais. Vérification de l'état et du serrage des boulons de fondation. Remplacement des sections Web de la grille. Restauration des endroits détruits des parois latérales, des sections de grille, des poutres de support. Vérification des performances de la grille.
8.2.6. Chambres de grenaillage et tambours. Vérification de l'état des éléments les plus soumis à l'usure : revêtement intérieur de la chambre, disques et portes d'extrémité, convoyeurs à plaques et à vis, séparateur avec remplacement des pièces usées. Démontage de la grenailleuse avec remplacement (si usé) de la turbine et des pièces d'usure, vérification de l'état des roulements, équilibrage de la turbine de la grenailleuse. Lavage des pièces des unités démontées. Serrage de la bande transporteuse à tablier, des courroies trapézoïdales de la grenailleuse, de la courroie des élévateurs et des entraînements par chaîne. Remplacement des fixations usées (endommagées). Vérification du parallélisme des gaines d'ascenseur. Vérification de l'état de la voie ferrée, des joints bout à bout, des fixations ; alignement des rails dans un plan horizontal par niveau.
8.2.7. Machines de refroidissement. Nettoyer et laver les surfaces des mécanismes des machines. Laver, essuyer les pièces des unités démontées. Remplacement des pièces d'usure : douilles, chemises, axes. Remplacement de tous les joints : manchettes, bagues, joints, joints et racleurs. Mesurer la quantité d'usure et vérifier l'état des guides, des bagues, des rouleaux à pâtisserie, des tiges, des tiges, des rouleaux. S'il y a des écarts, réparer ou remplacer. Réglage des tringles, biellettes, vérification du tassement des ressorts. Démontage du mécanisme de charnière et vérification de l'usure des douilles et des goupilles (le jeu admissible entre la douille et la goupille est conforme aux tolérances du dessin). Vérifier les fuites dans tous les cylindres hydrauliques et pneumatiques. Vérification de l'étanchéité aux joints des canalisations ; élimination des fuites de fluide de travail sur toute la longueur du réseau d'alimentation de la machine, aux endroits des joints et des connexions des canalisations, des mamelons et des bouchons de vidange. Réparation, réglage et remplacement de limiteurs, butées. Vérifier le fonctionnement des commandes, des protections, des dispositifs de sécurité et des verrouillages. Vérification de la rectitude des surfaces de montage des plaques pour la fixation des moules dans différentes directions. Vérification du parallélisme des plaques de montage pour le montage des moules. Vérification de la perpendicularité du plateau de la palette et des surfaces de montage latérales des plateaux pour la fixation des moules. Réparation ou remplacement des dispositifs de protection, assurant leur fonction conformément aux règles de sécurité. Vérification du fonctionnement des soupapes et des vannes. S'il y a des écarts, remplacez. Test de la machine au ralenti et sous charge.
8.2.8. machines centrifuges. Démontage détaillé du mécanisme d'éjection de la coulée et du mécanisme de rotation du moule, qui sont les plus soumis à l'usure. Lavage, essuyage et détection des défauts des pièces du mécanisme d'éjection de la coulée et rotation du moule. Remplacement des pièces d'usure : douilles, axes, bagues. Remplacement de tous les joints : manchettes, bagues, joints... Vérification de l'état et remplacement des galets défectueux. Vérifiez les joints des roulements et remplacez-les si nécessaire. Remplissage des roulements avec du plastique lubrifiant. Vérification du système de refroidissement des moules métalliques. Remplacement des presse-étoupes ou des raccords. Vérification du système de lubrification et de l'état de l'huile. Vérification de l'état des pièces des équipements hydrauliques et pneumatiques. Vérification de l'étanchéité aux joints des canalisations ; élimination des fuites de liquide sur toute la longueur du réseau d'alimentation de la machine, aux endroits des joints et des connexions des canalisations, des mamelons et des bouchons de vidange. Remplacement des joints qui ont perdu leur étanchéité. Vérification du serrage des fixations des couvercles, des brides, de toutes les connexions des systèmes hydrauliques et pneumatiques. Mise en place des équipements hydrauliques et pneumatiques de la machine. Test du système hydraulique de la machine. Vérification de l'état de la broche. Remplacement des roulements de broche. Vérification de l'état de la transmission par courroie trapézoïdale. Remplacement des courroies trapézoïdales. Démontage du mécanisme de charnière et vérification du développement des bagues et des doigts. Réparation, réglage et remplacement de limiteurs, butées, fusibles. Vérification du fonctionnement des équipements électriques, pneumatiques, hydrauliques. Vérification des normes de précision de la machine selon les spécifications. Test de la machine au ralenti et sous charge.
8.2.9. Machines de moulage par injection. Centrage de la traverse mobile par rapport aux colonnes. Vérification de l'écart entre les douilles de la traverse mobile et les colonnes (la tolérance ne doit pas dépasser la taille définie conformément aux dessins). Vérification du parallélisme des traverses mobiles et fixes. Vérification des écarts sur les écrous pour déplacer les traverses. Vérification du niveau de l'installation de la machine sur la fondation (la précision d'installation requise dans les deux sens est de 0,5 mm par 1000 mm). Serrage des boulons de fondation. Démontage du mécanisme de charnière et vérification de l'usure des douilles et des goupilles (écart autorisé entre la douille et la goupille conformément aux dessins. Il est interdit d'utiliser des douilles et des goupilles avec des traces d'éraflures de plus de 0,3 mm de profondeur). Remplacement des joints et des racleurs du mécanisme de pressage. Vérification de l'alignement de la tige de pressage par rapport à la coupelle de pressage. Vérifier les fuites dans les cylindres hydrauliques. S'il y a des fuites, inspectez et remplacez les joints. Vérification de la perpendicularité du vérin hydraulique de pressage par rapport à la traverse fixe. Vérification de la planéité de la plaque d'assise. Vérification du parallélisme des traverses mobiles et fixes. À la discrétion du mécanicien, le travail est effectué sur un ou tous les points de l'inspection. Assemblage d'appareils et de mécanismes réparés. Test de la machine au ralenti et sous charge. Test du système hydraulique à une pression supérieure à celle de travail de 25 %.
8.3. Révision
Pendant la révision, tous les travaux de réparation en cours sont effectués; en outre, les travaux suivants sont effectués sur les noms d'équipement.
8.3.1. Robinets. Vidange de l'huile des conteneurs. Compléter le démontage détaillé et le dépannage des unités, des assemblages et des pièces. Si nécessaire, restaurer ou remplacer : roulements, arbres, bagues, tiges, pistons, chemises de cylindre, joints, fixations, supports, boulons d'ancrage, crémaillères et cadres, coque et fond de cuve, jantes de rouleaux, ressorts, mécanismes de levier. Les surfaces des soutes, des portes, des écoutilles et des réservoirs doivent être redressées, sablées aux endroits où la corrosion est présente, puis apprêtées et peintes. Les bunkers, réservoirs, citernes, etc. en acier résistant à la corrosion doivent être redressés s'il n'y a pas d'usure importante. Restaurer la fondation. Restauration ou remplacement d'éléments : équipements pneumatiques, équipements de lubrification, systèmes électriques, tableaux, enseignes, numéros, inscriptions. Test de charge et mise en service.
8.3.2. Machines de formage. Démontage détaillé complet de tous les composants et mécanismes de la machine. Lavage, essuyage des pièces d'assemblages et mécanismes. Réparation des mécanismes d'agitation, de pressage, de rotation, d'échappement, des mécanismes de rotation de la traverse et du racleur, des flacons de préhension. Remplacement des pièces principales rejetées : tables vibrantes et rotatives, cylindres et pistons, cylindre de presse, leviers et supports, colonnes, goupilles, tourillons, arbres, axes. Remplacement segments de piston, manchettes, colliers, bagues, manchons, tiges, rouleaux à pâtisserie. Remplacement de l'ensemble des amortisseurs. Réparation de dispositifs de serrage, mécanisme de fixation. Remplacement des accouplements, engrenages, engrenages, crémaillères rejetés. Remplacement d'éléments d'équipements hydrauliques et pneumatiques, système de lubrification, réparation de la canalisation et des éléments de ses connexions. Réparation ou remplacement des dispositifs de protection et de protection conformément aux exigences de sécurité. Assemblage, installation et test des composants et mécanismes réparés au ralenti et sous charge. Vérification de l'état de la fondation et de sa réparation. Remplacement de parquet. En présence de fissures, battage et coulage du ciment avec des grades de ciment à haute résistance. Remplacement complet du lubrifiant. Mastic, peinture de toutes surfaces brutes.
8.3.3. Moulins à barres. Démontage détaillé complet de tous les composants et mécanismes de la machine. Lavage, essuyage et inspection de toutes les pièces. Compilation et clarification de la feuille d'estimation défectueuse. Remplacement complet de toutes les fixations usées. Réparation du mécanisme de levage de la boîte à noyaux, du mécanisme de pression de la boîte à noyaux sur la buse (ou du mécanisme d'abaissement de la buse), du mécanisme de démontage de la boîte à noyaux, du mécanisme de soufflage avec la soupape d'aspiration et d'échappement, du mécanisme de déplacement transversal et autres mécanismes sujets à l'usure. Réparation du dispositif de porte, de l'alimentateur vibrant et d'autres unités. Remplacement des principales pièces rebutées : manchon de sablage, plaques gonflables avec évents, vérins et pistons, leviers, supports, colonnes, goupilles, arbres, axes, etc. Réparation et remplacement des dispositifs de serrage et de fixation, chaînes et engrenages des convoyeurs et de leurs éléments. Réparation de l'équipement pneumohydraulique et du système d'approvisionnement en eau avec remplacement des éléments de l'équipement pneumohydraulique ; réparation des canalisations et élimination des fuites sur toute la longueur du réseau électrique. Réparation et remplacement d'éléments du système de lubrification. Réparation d'équipements électriques avec remplacement d'éléments d'équipements électriques et de radiateurs électriques tubulaires, systèmes de chauffage pour boîtes à noyaux. Réparation du système de chauffage au gaz des boîtes à noyaux avec remplacement des éléments d'équipement au gaz ; réparation des canalisations et élimination des fuites. Réparation de l'équipement pyrométrique du système de contrôle et de maintien de la température de consigne des boîtes à noyaux chauffants. Réparation ou remplacement des dispositifs de protection et de protection conformément aux exigences de sécurité. Vérifier l'installation de la machine et l'état des fondations. Vérifier, resserrer ou remplacer les boulons de fondation ; fixation de la fondation en versant du mortier de ciment. Vidange complète : la vidange de l'huile usagée et le remplissage d'huile neuve. Effectuer des analyses en laboratoire de la qualité de l'huile pour la conformité aux indicateurs physiques et chimiques du passeport. Assemblage de la machine à partir de composants et de mécanismes réparés. Vérification de la bonne interaction des nœuds et des mécanismes de la machine. Peinture des surfaces externes non fonctionnelles de la machine avec du mastic ; restauration des tables, inscriptions, index endommagés, etc. Test de la machine au repos et en charge. Vérification de la conformité de la machine avec les données de passeport et les normes de précision spécifiées dans le manuel d'instructions.
8.3.4. Lanceurs de sable. Démontage détaillé complet de tous les composants et mécanismes de la machine. Lavage, essuyage et inspection de toutes les pièces. Rédaction d'une feuille de devis défectueuse. Remplacement complet de toutes les fixations usées. Démontage complet de la tête de lancement avec remplacement du boîtier, remplacement de la tête. Équilibrage du rotor de la tête de lancement assemblé. Démontage de boîtes de vitesses avec remplacement d'une paire de vis sans fin, d'engrenages, de roulements, de bagues, de joints et d'autres pièces. Démontage du mécanisme de mouvement avec remplacement des rampes, axes, entraînement par chaîne, roulements et autres pièces. Inspection des soudures et soudure des fissures. Assemblage de composants et mécanismes réparés. Vidange de l'huile des réservoirs et rinçage du système de tuyauterie. Installation et réglage des équipements hydrauliques selon le schéma hydraulique et les données du passeport. Vérification du bon fonctionnement des principaux organes du lanceur de sable par démarrage séparé ou combiné des mécanismes ; faire tourner la voiture au ralenti. Masticage et peinture de toutes les surfaces brutes selon cahier des charges pour la finition des équipements neufs. Pour les lanceurs de sable stationnaires, vérifiez l'état et réparez la fondation (serrage ou remplacement des boulons de fondation, fixation de la fondation par ajout de mortier de ciment). Pour les lanceurs de sable mobiles - vérification de l'état et remplacement des sections individuelles de la voie ferrée, remplacement des pièces des joints bout à bout et des fixations des rails, mise à niveau des rails dans un plan horizontal. Test de la machine sous charge.
8.3.5. Grilles défonçables. Démontage détaillé complet de tous les nœuds. Lavage, essuyage et inspection de toutes les pièces. Rédaction d'une feuille de devis défectueuse. Remplacement des pièces usées (arbres, roulements, boulons, accouplements, etc.). Réparation ou remplacement des parois latérales, des poutres de support, des sections de grille. Remplacement complet du lubrifiant. Vérification de l'état de la fondation et installation du cadre de support. Peinture sur treillis, restauration de plaques, inscriptions, enseignes.
8.3.6. machines centrifuges. Démontage détaillé de tous les composants et mécanismes de la machine. Nettoyage de la saleté, lavage, essuyage et inspection de toutes les pièces. Rédaction d'une feuille de devis défectueuse. Remplacement ou réparation de toutes les pièces usées et défectueuses. Vérification de l'état des boulons de fondation et de la fondation (si nécessaire, remplacement des boulons de fondation et de la fondation). Rinçage du système hydraulique. Vidange. Réaliser une refonte majeure du système électrique. Assemblage et vérification de l'interaction correcte de tous les mécanismes des équipements électriques, hydrauliques et pneumatiques en fonctionnement au ralenti. Test de chargement.
8.3.7. Chambres de grenaillage et tambours. Démontage détaillé complet de tous les composants et mécanismes. Lavage, essuyage et inspection de toutes les pièces. Remplacement de la grenailleuse. Équilibrage du rotor de la grenailleuse sous forme assemblée. Remplacement complet de toutes les fixations usées. Remplacement complet des pièces de la grenailleuse : flexibles, ressorts, soupapes, joints et autres pièces. Démontage complet de l'élévateur : remplacement des roulements, godets, arbres, bagues et autres pièces, ainsi que remplacement des pièces usées de la protection. Démontage complet de la tarière avec remplacement des sections et des roulements. Démontage complet des mécanismes de rotation de la table et de rotation des plateaux. Démontage de l'élévateur avec remplacement des godets et des rivets (boulons) usés, remplacement ou réparation de la courroie de l'élévateur. Démontage de la vis sans fin avec remplacement des sections. Démontage complet du mécanisme de déplacement du chariot ; remplacement des roues de support usées, des câbles, du tambour, des galets tendeurs et d'autres pièces. Démontage complet du foyer mobile, remplacement complet des plaques transporteuses, disques latéraux, pignons, chaînes et autres pièces usées. Démontage du palan à benne, remplacement des blocs de câble, des galets de support, des guides de canal, soudure et réparation du châssis. Démontage complet des boîtes de vitesses avec remplacement des vis sans fin, engrenages, roulements, bagues, joints et autres pièces. Remplacement des courroies et poulies usées de tous les entraînements par courroie trapézoïdale. Réparation de dispositifs de verrouillage et de charnières, couvercles, tôles blindées, redressage de portes. Peinture de toutes les surfaces brutes selon les spécifications pour la finition des équipements neufs. Test de la machine au ralenti et sous charge.
8.3.8. Machines de moulage par injection. Démontage détaillé complet de tous les composants et mécanismes de la machine. Lavage, essuyage, inspection et mesure de l'usure de toutes les pièces de la machine. Préparation d'une fiche d'estimation complète des défauts. Remplacement complet de toutes les fixations usées. Remplacement des pièces d'usure et ensembles de vannes et boîtiers de distribution : pompe, tiroirs, vannes, sièges, manchettes, joints, ressorts, poussoirs, bouchons. Remplacement des douilles, pistons et douilles du plateau mobile du porte-moule. Remplacement des pièces de la cale et du mécanisme à manivelle pour le verrouillage du moule : cales, chemises, doigts de douille et autres pièces. Soudage des fissures du lit. Meulage des surfaces de travail internes et externes des cylindres avec usure, risques et rayures, suivi d'un chromage. Démontage des canalisations avec rinçage et purge, remplacement de sections individuelles de canalisations, joints, mamelons et autres pièces. Vérification du parallélisme et de la planéité du sommier. En présence d'écarts, les travaux de restauration doivent être effectués conformément au dessin. Vérification de la bonne installation du cadre sur la fondation (la précision d'installation requise dans les deux sens est de 0,1 mm par 1000 mm). Vérification de l'état de la fondation. Vérification, serrage et remplacement des boulons de fondation. Correction de la fondation conformément aux spécifications pour la fabrication de la fondation. Installation de mécanismes réparés sur le châssis. Installation et réglage des équipements hydrauliques selon le schéma et les spécifications hydrauliques. Vérification de la bonne interaction des nœuds et des mécanismes de la machine. Vérification de la perpendicularité du vérin hydraulique de pressage par rapport à la traverse fixe. Vérification de l'alignement de la tige de pressage par rapport à la coupelle de pressage. Vérification du parallélisme des traverses mobiles et fixes. Rodage à vide : ouverture, fermeture du moule et pressage à froid. Peinture complète de toutes les surfaces externes non travaillantes de la machine. Restauration des tableaux et des inscriptions. Test de la machine sous charge. Vérification de la conformité de la machine avec les données du passeport. Acceptation selon TU et GOST.
Noter. Teneur travaux standards, effectuées lors des réparations de la partie mécanique de la presse à injecter, ne comprennent pas les opérations de réparation des outillages (moules) et du groupe de pompage.
8.3.9. Machines de refroidissement. Démontage détaillé complet de tous les composants et mécanismes de la machine. Nettoyage de la saleté, lavage, essuyage et inspection de toutes les pièces. Rédaction d'une feuille de devis défectueuse. Dépannage et remplacement des fixations usées. Restauration de pièces de base : plaques de sous-coulage, lit, crémaillères, corps de palette, plateau de palette. Fissures de soudure dans le bâti de la machine. Vérification de la planéité des surfaces de travail des plaques de sous-coulage ; en cas de déviation - fraisage (pour les machines conçues pour la longueur des pièces moulées en métaux ferreux). Remplacement de bielles, pistons, genoux, cylindres ne faisant pas l'objet de remise à neuf. Remplacement de pièces d'équipements de distribution hydraulique; manchettes, joints, ressorts, poussoirs, fiches et boîtes de jonction d'équipements électriques. Remplacement des bagues, chemises, essuie-glaces, tiges, axes, boucles d'oreilles, rouleaux. Réparation et remplacement de tous les dispositifs de protection et dispositifs de protection. Assemblage de machines à partir de composants et de mécanismes réparés. Vérification de la rectitude des surfaces de montage des plaques pour la fixation des moules. Masticage, apprêt et peinture de toutes les surfaces externes non travaillantes de la machine, restauration des tableaux et des inscriptions. Vérification de l'état des fondations, réparation de la fondation en versant du mortier de ciment, vérification et remplacement des boulons de fondation. Vérification de l'interaction correcte de tous les mécanismes de travail de la machine. Vérification des équipements électriques, hydrauliques, pneumatiques en mode opérationnel, semi-automatique et automatique.
8.4. Normes de fréquence, de durée et de complexité des réparations
Les normes de fréquence, de durée et de complexité des réparations des équipements de four électrique de fonderie sont indiquées dans le tableau. 8.1.
Tableau 8.1


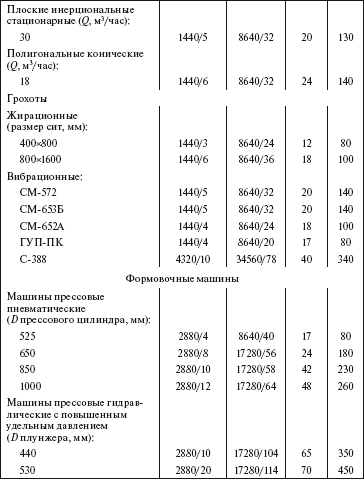
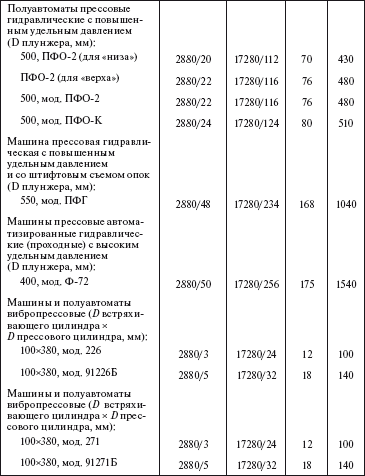


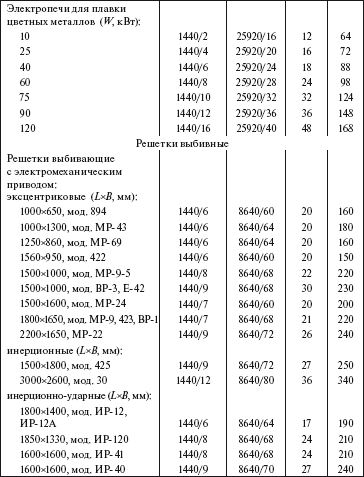

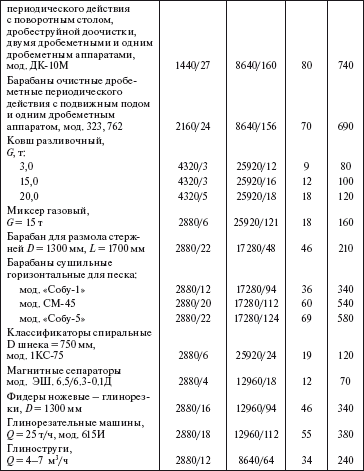

9. ÉQUIPEMENT DE CONCASSAGE, DE BROYAGE ET DE TRI
Les équipements de concassage, broyage et tri sont affectés au sixième groupe d'amortissement avec une durée d'utilité supérieure à 10 à 15 ans inclus.
L'équipement utilisé pour le concassage, le broyage et le criblage fonctionne dans un mode d'usure intense et subit des charges alternées élevées. La durée de vie des organes de travail de cet équipement ne dépasse pas 34 560 heures, après quoi une révision majeure est nécessaire.
9.1. Maintenance
9.1.1. L'entretien des équipements de concassage et de broyage est effectué pendant son fonctionnement par les ouvriers de la production lors de la livraison et de l'acceptation des quarts de travail conformément aux instructions du lieu de travail. L'objectif principal de la maintenance est d'assurer le bon fonctionnement. La pratique montre que sa violation entraîne une usure accrue et des pannes d'urgence de certaines parties de l'équipement.
9.1.2. Outre le nettoyage des équipements et la lubrification, l'inspection et le contrôle de l'état technique des mécanismes et des assemblages, le réglage et l'élimination des dysfonctionnements mineurs sont effectués.
9.1.3. La maintenance des équipements incombe non seulement au personnel d'exploitation, mais également aux réparateurs en service, aux chefs de quart, qui surveillent périodiquement visuellement, auditivement et à l'aide d'instruments de mesure le fonctionnement des unités les plus critiques ( moteurs électriques, boîtes de vitesses, accouplements) jusqu'à leur ouverture lors d'arrêts brefs de l'équipement.
En dehors de contrôles techniques effectués par le personnel de maintenance, des arrêts programmés des sections de concassage et de broyage sont effectués, au cours desquels l'état de fonctionnement de l'équipement est surveillé à l'aide d'appareils de diagnostic. Tous les dysfonctionnements identifiés sont éliminés immédiatement si cela peut entraîner des arrêts de l'équipement pendant le fonctionnement.
9.2. Maintenance
9.2.1. Concasseurs à mâchoires. Inspectez et, si nécessaire, remplacez la plaque d'espacement arrière, les tiges, les joints et les ressorts correspondants, le blindage latéral supérieur, les craqueurs de plaque d'espacement, les roulements d'entraînement, les courroies trapézoïdales, les ressorts, les tiges. Alignez les essieux et les surfaces de référence. Faites les réglages et testez.
9.2.2. Concasseurs à cône. Réparez ou remplacez la plaque de distribution. Vérifier et, si nécessaire, remplacer l'armure usée du cône d'écrasement, l'armure fixe et la garniture de la bague de commande, les douilles coniques et cylindriques de l'ensemble excentrique. Vérifier le fonctionnement du système de lubrification, changer l'huile si nécessaire. Remplacez l'armure de la partie inférieure du corps du concasseur et l'armure d'entraînement, les bagues et les disques du palier de butée, les engrenages de l'arbre d'entraînement. Inspectez et réparez la roue dentée excentrique. Remplacez les bagues d'arbre de transmission avant et arrière. Remplacer les ressorts et l'arbre d'entraînement si nécessaire. Faites les réglages et testez.
9.2.3. Concasseurs à marteaux et rouleaux. Remplacer les marteaux (pour réduire la durée de la réparation en cours, le rotor avec les marteaux usés est démonté et remplacé par un pré-assemblé). Laver et lubrifier les roulements. Vérifiez l'alignement du rotor avec l'arbre du moteur. Vérifiez et, si nécessaire, remplacez les courroies trapézoïdales et les grilles. Remplacez la doublure dans la zone de battement. Réparer et équilibrer le rotor. Remplacer les joints. Ajusteur de réparation. Faites les réglages et testez.
9.2.4. Serrez la fixation de la doublure, révisez la station d'huile. Vérifier et, si nécessaire, remplacer sélectivement les plaques de revêtement, éléments de la grille de fixation. Remplacez partiellement ou complètement la garniture du tambour et des couvercles, les garnitures de garniture et les boulons individuels. Remplacez ou réparez la mangeoire à escargots. Inspectez le disque ou remplacez-le (si un disque de rechange est disponible). Vérifiez l'alignement de l'entraînement.
9.2.5. Moulins à cylindres. Serrez les boulons de fixation du broyeur. Remplacer les socs, l'anneau de meulage, les lames. Rincer le système d'huile. Remplacez ou restaurez l'arbre d'entraînement, le petit engrenage conique, les bagues d'arbre vertical, les bagues à rouleaux, les essieux pendulaires et partagés, le grand engrenage conique (le travail est effectué au besoin).
9.2.6. Écrans GNT. Vérifiez et ajustez l'amplitude et la rectitude des oscillations de la boîte avec le cadre, l'uniformité des écarts entre les tampons des liens élastiques et l'absence d'oscillations locales des tamis, des parties de la boîte du cadre et d'autres éléments. Vérifiez et, si nécessaire, remplacez les roulements du vibrateur et les ressorts de support, les grilles de chargement et de déchargement.
9.2.7. Écrans GIL. Vérifiez et ajustez l'amplitude et la rectitude des vibrations de la boîte avec le cadre, les écarts entre les tampons des liens élastiques, l'absence de vibrations locales des tamis, des parties de la boîte, du cadre et d'autres éléments. Vérifiez les connexions des goulottes de chargement et de déchargement, des bains, des accouplements et des courroies trapézoïdales, éliminez les défauts identifiés. Remplacez les écrans, les bandes, les tubes inférieurs et supérieurs lors du chargement de la boîte.
9.2.8. Écrans GSL. Vérifiez et ajustez l'amplitude et la rectitude des vibrations de la boîte avec le cadre, les écarts entre les tampons des liens élastiques et l'absence de vibrations locales des tamis, des parties de la boîte, du cadre et d'autres éléments. Vérifiez l'état des goulottes de chargement et de déchargement. Retirez les tamis supérieur et inférieur. Éliminer les défauts trouvés dans les pièces et les assemblages de la boîte. Si nécessaire, remplacer les tamis, lamelles, équerres, lamelles et attaches des tamis, doigts vibreurs. Réparer les dispositifs de protection et régler le fonctionnement de l'écran.
9.3. Révision
Pendant la révision, tous les travaux de réparation en cours sont effectués; en outre, l'étendue suivante des travaux de réparation par type d'équipement.
9.3.1. Concasseurs à marteaux. Retirez les protections, les courroies trapézoïdales d'entraînement, le moteur électrique, les poulies, la goulotte de chargement, la partie supérieure du boîtier, les couvercles et les boîtiers de roulement, les joints de presse-étoupe, le rotor, les chariots, la barre de garde-boue, la douille conique, les roulements du rotor. Démontez le rotor, la grille de suspension, les chariots, l'armure de revêtement en pièces. Nettoyez et triez les pièces du concasseur et les pièces de fixation, remplacez celles qui sont défectueuses. Faire des tampons. Installez les roulements, la bague conique, la barre de protection, les chariots, les joints de presse-étoupe, les boîtiers et couvercles de roulement, la partie supérieure du boîtier, la goulotte de chargement, les poulies, le moteur électrique, les courroies trapézoïdales, les protections. Tester et mettre en service.
9.3.2. Concasseurs à rouleaux. Retirez les protections, le coupleur, les courroies, le toit du concasseur, les chapeaux de palier, les roulements, les unités d'entraînement du concasseur et les pièces, les unités et les pièces périphériques internes broyeurs. Démontez les composants du concasseur en plusieurs parties. Nettoyer et trier les pièces, remplacer celles qui sont défectueuses. Nettoyez l'intérieur du broyeur. Démonter les fixations. Faire des tampons. Assemblez et installez les dispositifs internes et les unités d'entraînement, les roulements, les chapeaux de palier, le couvercle du broyeur, les courroies, le coupleur. Installez des clôtures. Tester et mettre en service.
9.3.3. Concasseurs à mâchoires. Déposer les carters, courroies, poulies, chapeau, volant moteur, chapeaux de paliers, bielle, arbre excentrique, ressort, plaques entretoises, axe de la joue mobile, joue mobile, cales de dilatation latérales, roulements. Nettoyer et trier les pièces du concasseur et les pièces de fixation. Faire des tampons. Monter les roulements, les cales d'écartement latérales, la joue mobile, l'axe de la joue mobile, les plaques entretoises, le ressort de traction, l'arbre excentrique, les chapeaux de bielle et de roulement de mouche, le chapeau, les poulies, les courroies, les protections. Tester et mettre en service.
9.3.4. Concasseurs à cône. Déposer les protections, moteur électrique, courroies de transmission, demi-accouplements, dispositif de chargement, carter, dispositif de verrouillage, plaque de distribution, culasse, bague de réglage, coupelle de support, excentrique, arbre de transmission, blindage, ressort d'amortisseur. Démontez les pièces du concasseur en plusieurs parties. Nettoyez et triez les pièces du concasseur et les pièces de fixation, remplacez celles qui sont défectueuses. Faire des joints, des joints. Assembler les composants du concasseur à partir de pièces. Installez le dispositif de chargement, l'anneau de commande, le cône de broyage, le bol de support, l'anneau de commande, l'arbre d'entraînement, les ressorts d'amortisseur, l'excentrique, la plaque de distribution, le dispositif de verrouillage, le moteur électrique, les moitiés d'accouplement, les courroies d'entraînement, les protections. Tester et mettre en service.
9.3.5. Broyeurs à billes et à barres. Déconnectez et retirez les protections, les courroies, les canalisations, la boîte de vitesses, le moteur électrique. Débranchez le coupleur. Retirez l'arbre d'entraînement et comprimez les roulements de support et l'engrenage. Sortez le tambour du broyeur à boulets. Pressez les roulements principaux ensemble et retirez les moitiés inférieures des logements de roulement. Déconnectez et retirez la couronne dentée et les capuchons d'extrémité du tambour. Nettoyer l'intérieur du moulin. Rincez et triez les pièces de l'appareil et les fixations, remplacez celles qui sont défectueuses. Préparez un jeu de joints. Vérifiez la boîte de vitesses. Installez et fixez les embouts de tambour et la couronne dentée. Installez les boîtiers de roulement et pressez les roulements sur l'arbre. Installez le tambour. Assemblez et installez l'arbre d'entraînement avec l'engrenage. Connectez l'accouplement, installez la boîte de vitesses et le moteur électrique. Mettez des ceintures. Installer des canalisations et des clôtures. Testez le moulin et mettez-le en marche.
9.3.6. Moulins pendulaires. Déconnectez et retirez la conduite, la protection, le couvercle du carter du broyeur, le boîtier. Retirer les courroies d'entraînement. Déconnecter le séparateur, le chargeur. Retirez l'engrenage conique d'entraînement avec l'arbre d'entraînement. Démontez le corps du broyeur, retirez les pièces des dispositifs internes (croix, pendules, rouleaux, racleurs, socs, vis sans fin, système de lubrification, système d'entraînement du pendule). Nettoyer, laver et trier les pièces du moulin et des fixations, remplacer celles qui sont défectueuses. Inspectez les engrenages à vis sans fin et coniques. Préparez un jeu de joints. Installez les détails des dispositifs internes, assemblez le corps du moulin. Installez l'engrenage conique d'entraînement avec l'arbre d'entraînement. Installez le chargeur, le séparateur, les courroies d'entraînement. Installez et fixez le boîtier, le couvercle du corps du broyeur, les clôtures, la canalisation. Testez le moulin et mettez-le en marche.
9.3.7. Moulins "Désintégrateur". Déconnecter les couvercles de trou d'homme, déconnecter et retirer le carter, déconnecter les deux raccords. Retirez les arbres avec les disques et les roulements à rouleaux, appuyez sur deux moitiés d'accouplement, retirez les disques des arbres. Nettoyer, rincer et essuyer les pièces, trier, remplacer celles qui sont défectueuses. Préparez un jeu de joints. Vérifiez et équilibrez le lecteur. Installez les disques sur les arbres, appuyez sur deux moitiés d'accouplement, installez les arbres avec les disques et les roulements à rouleaux. Connectez les raccords, installez et fixez le boîtier. Installer des couvercles de trou d'homme. Testez le désintégrateur et mettez-le en service.
9.3.8. Moulins "Démembraneur". Retirez les courroies, la poulie. Ouvrez le couvercle du boîtier, retirez les disques mobiles et fixes avec cames et le moyeu. Sortez l'arbre, appuyez sur les roulements. Sortez le tambour. Nettoyer, rincer, essuyer et trier les pièces, remplacer celles qui sont défectueuses. Remplacer les cames, disque fixe, écran démembreur, cracker. Préparez un jeu de joints. Installez le tambour, appuyez sur les roulements et installez l'arbre. Installez le moyeu, les disques à cames fixes et mobiles. Fermez le couvercle du boîtier. Installez la poulie, les courroies. Testez le démembreur et mettez-le en service.
9.3.9. Broyeurs à arbre et colloïdes. Retirer la protection, déconnecter les moitiés d'accouplement. Débrancher et retirer le couvercle, démonter le moulin (retirer les batteurs, l'embrayage, les portes du moulin), retirer et démonter le rotor, retirer l'arbre de la boîte de vitesses. Démonter la pompe à huile avec le tuyau d'huile et le filtre. Nettoyez, rincez, essuyez et triez les pièces et accessoires du moulin. Remplacer les roulements. Installez l'arbre de la boîte de vitesses, assemblez et installez le rotor. Assemblez le moulin, installez et fixez le couvercle du moulin. Connectez les moitiés d'accouplement, installez les protections.
9.3.10. Moulins à cinq rouleaux "Raymond", moulin "Leshe" et autres. Séparez les joints de bride, retirez la conduite d'huile, l'entraînement hydraulique, l'équilibreur. Retirez la protection, la courroie, le chargeur. Déconnectez et retirez le carter du moulin. Démonter le moulin, nettoyer la surface intérieure. Nettoyer, rincer et trier les pièces et accessoires de l'usine. Vérifiez la boîte de vitesses. Récupérez le moulin. Installez le corps du broyeur, le chargeur, la courroie et la protection. Installez l'équilibreur, l'entraînement hydraulique, l'oléoduc. Connectez les joints de bride. Testez le moulin et mettez-le en marche.
9.3.11. Moulins humides. Retirez la tuyauterie, les raccords, les protections, les courroies trapézoïdales, le moteur électrique, la poulie, la boîte de vitesses, les arbres intermédiaires et verticaux, les pinces de glissière, les glissières, le bol pivotant. Nettoyer et trier les pièces, remplacer celles qui sont défectueuses. Vérifiez la boîte de vitesses. Installez le bol pivotant, les glissières, les pinces de glissière, les arbres verticaux et intermédiaires, la boîte de vitesses, la poulie, le moteur électrique, les courroies trapézoïdales, les protections, les raccords, la tuyauterie. Testez l'appareil à vide et mettez-le en service.
9.3.12. Écrans. Retirez les protections d'entraînement, la transmission par courroie et les poulies des arbres du vibrateur et du moteur. Déposer le moteur électrique, les carters d'arbre et de vibrateur, les colliers et balourds, les chapeaux de palier. Appuyez sur les douilles et les roulements et retirez l'arbre d'entraînement du vibrateur avec le tube d'espacement. Retirez les écrans, les barres de serrage et les joints. Démontez la suspension, retirez la boîte et la goulotte rugissent. Nettoyer, laver et trier les pièces, remplacer celles qui sont défectueuses. Installez et fixez la boîte, les cintres, les grilles sur les lattes, les lattes de serrage, le tuyau d'espacement avec l'arbre d'entraînement du vibrateur. Appuyez sur les douilles et les roulements. Installez et fixez le boîtier de l'arbre du vibrateur, les poulies sur les arbres, le moteur électrique, la transmission par courroie, les protections et les goulottes. Essai de dépistage et mise en service.
9.3.13. Broyeur rotatif en plastique. Déposer le capot de protection de l'accouplement, le moteur électrique, le guide et la partie inférieure de la trémie, le capot supérieur et la grille du stator, les couteaux du rotor et du stator, le capot de fixation du rotor, le rotor, les chapeaux de paliers, les coupelles, les roulements, la grille inférieure du stator, le stator, le moteur électrique, le ventilateur, la turbine de l'arbre . Nettoyez et démontez les pièces, remplacez celles qui sont défectueuses. Équilibrez la turbine. Installez la turbine sur l'arbre, le ventilateur, le moteur électrique, le stator, la grille inférieure du stator, les roulements, les coupelles, les chapeaux de palier, le rotor, le couvercle de montage du rotor, les couteaux du rotor et du stator, la grille supérieure et le couvercle du stator, les parties inférieure et de guidage de la trémie, moteur électrique, capot de protection accouplement . Testez le broyeur au ralenti et sous charge, mettez-le en marche.
9.4. Normes de fréquence, de durée et de complexité des réparations
Les normes relatives à la fréquence, à la durée et à la complexité des réparations des équipements de concassage, de broyage et de criblage sont indiquées dans le tableau. 9.1.
Tableau 9.1
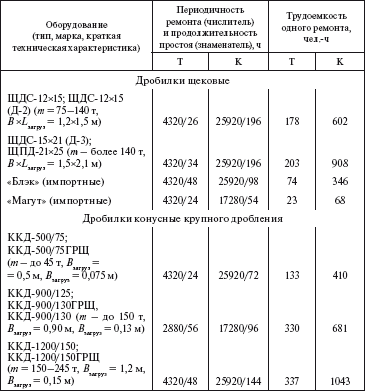


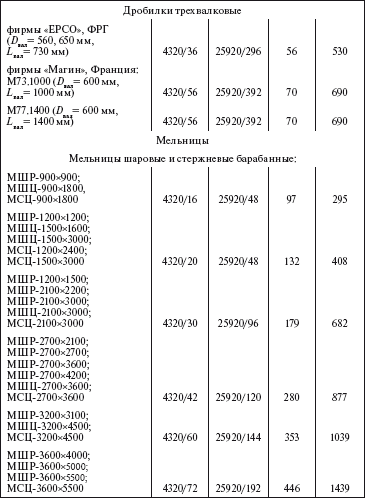
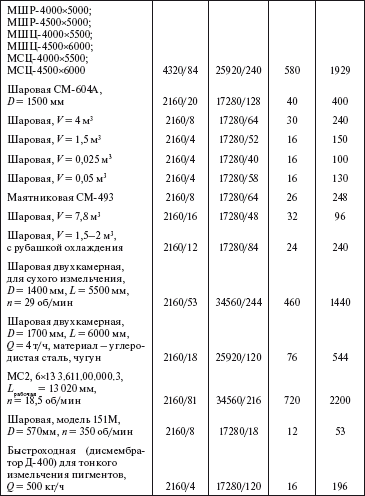
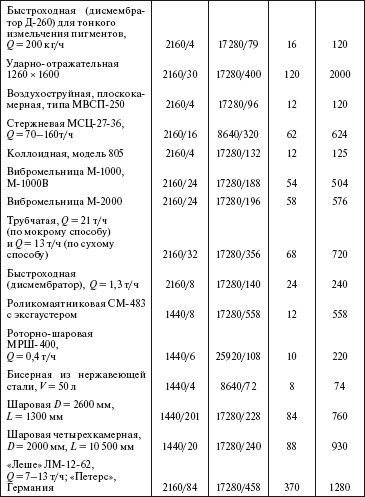
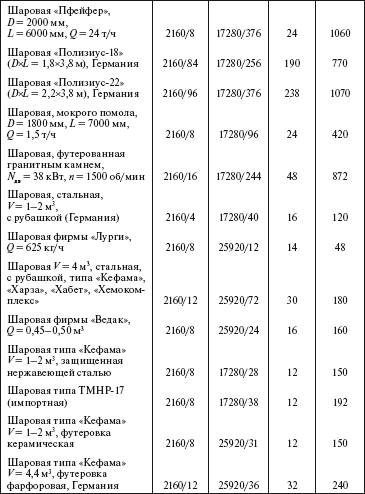
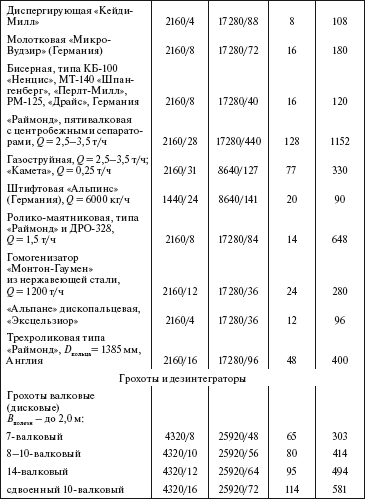
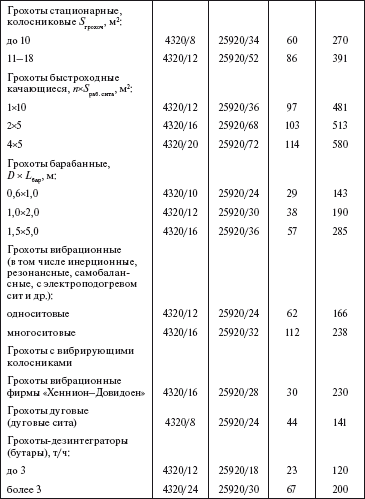

10. MACHINES ÉLECTRIQUES
Des instructions de maintenance et de réparation sont données pour les types de machines électriques suivants : asynchrones, synchrones et à courant continu.
10.1. Maintenance
10.1.1. Les opérations de maintenance pour tous les types de machines électriques sont similaires et sont effectuées, en règle générale, avec une maintenance réglementée.
10.1.2. Lors de la maintenance, les travaux suivants sont effectués: réparations mineures ne nécessitant pas d'arrêt spécial de la machine et effectuées pendant les pauses dans le fonctionnement des installations technologiques afin de corriger en temps opportun les défauts mineurs, notamment: serrage des contacts et des fixations; changement de brosse; réglage des traverses, dispositifs qui fournissent les paramètres de sortie des générateurs, des convertisseurs et des convertisseurs ; réglage des protections ; essuyer et nettoyer les parties accessibles de la machine (surfaces extérieures, bagues, collecteurs, etc.) ; surveillance quotidienne du respect des PTE et des instructions du fabricant, en particulier contrôle de la charge, de la température des roulements, des enroulements et du boîtier, et pour les machines avec un système de ventilation fermé - température de l'air entrant et sortant ; contrôle de la présence de lubrification; vérification de l'absence de bruits et bourdonnements anormaux, ainsi que de l'absence d'étincelles sur les collecteurs et bagues ; surveillance quotidienne de l'état de fonctionnement de la mise à la terre ; arrêt des machines électriques en cas d'urgence; participation aux essais de réception après installation, réparation et réglage des machines électriques et de leurs systèmes de protection et de contrôle.
10.1.3. Pour les moteurs électriques antidéflagrants, les opérations suivantes sont en outre effectuées : vérification de l'état de l'enveloppe antidéflagrante ; serrage de boulons, écrous, bagues de protection ; vérification de l'état de fonctionnement des dispositifs d'entrée, de la présence d'éléments d'étanchéité et de câbles de fixation. Pour les moteurs électriques fonctionnant dans la version souterraine, les opérations suivantes sont effectuées : nettoyer les trous de drainage dans les brides de sortie d'huile et dévisser les vis des trous de lubrification inférieurs, vérifier l'alimentation en eau et le système de drainage ; vérification de la présence de bagues d'étanchéité en caoutchouc, de fiches et d'isolateurs, de pinces conductrices de courant d'appareils d'entrée et de câbles de toutes tailles.
10.2. Maintenance
10.2.1. La gamme typique de travaux pour la réparation courante des machines électriques comprend toutes les opérations de maintenance ; outre:
démontage partiel du moteur électrique ; vérifier le bon fonctionnement et la fixation du ventilateur ; tourner les cols de l'arbre du rotor et réparer la "cage d'écureuil" (si nécessaire); contrôle de dédouanement ; changement des joints de bride et lubrification des roulements ; remplacement des roulements usés, lavage des paliers lisses et, si nécessaire, leur remplissage ; restauration des aiguisages aux boucliers du moteur électrique; montage du moteur électrique avec essai au ralenti et en fonctionnement ; vérifier les fixations de la machine et l'état de fonctionnement de la mise à la terre ;
démontage du moteur électrique ; élimination des endroits endommagés des enroulements du stator et du rotor sans les remplacer; rinçage des composants mécaniques et des pièces du moteur électrique ; remplacement des cales à fente et des douilles isolantes défectueuses ; imprégnation et séchage des enroulements; recouvrir l'enroulement d'une couche de finition ; vérification de l'état de fonctionnement et de la fixation du ventilateur ; si nécessaire, tourner les cols de l'arbre du rotor, vérifier les jeux, changer les joints de bride, rincer et graisser les roulements, remplacer les roulements usés, rincer les paliers lisses et, si nécessaire, les remplir, restaurer les affûtages des blindages du moteur électrique, tourner et bagues de meulage, si nécessaire - leur remplacement, réglage et fixation de la traverse porte-balais, réparation du mécanisme des balais, remplacement des balais, montage du moteur électrique avec essai au ralenti et en fonctionnement, vérification des fixations du moteur électrique et l'état de fonctionnement de la mise à la terre ;
démontage du moteur électrique et inspection de ses pièces; réparation, imprégnation et séchage de l'isolation des bobinages ; remplacement des cales défectueuses fixant l'enroulement; remplacement des pneus usés, remplacement des balais, inspection et vérification du fonctionnement des dispositifs de démarrage du moteur électrique ; mesure des jeux entre le rotor et le stator ; assemblage et test de moteurs (essais);
vérifier les fixations disponibles, l'état du collecteur et des porte-balais ; vérifier l'état de tous les équipements auxiliaires de la machine ; démontage de la machine électrique ; vérification de l'état des roulements, tourillons d'arbre avec mesure des jeux, isolation des roulements, changement des lubrifiants ; conduire le collecteur, chanfreiner les plaques, rectifier le collecteur, réparer les porte-balais, remplacer les balais usés, vérifier les enroulements et les bandages avec mesurer la résistance d'isolement ; vérifier l'état des cales à fente, des bandages, des entretoises d'égalisation, des barres de pression, des supports d'enroulement ; vérification de l'état des rations d'induit par la méthode de la chute de tension ; restauration des revêtements de vernis des enroulements et autres pièces; mesure des écarts entre l'espace de fer et l'assemblage de la machine ; vérifier l'état de mise à la terre du corps de la machine ; test au travail.
10.2.2. Pour les moteurs électriques antidéflagrants, les surfaces antidéflagrantes des brides et leurs joints sont également vérifiés, la qualité de l'étanchéité du câble est vérifiée et la taille de la bague d'étanchéité correspond au diamètre de l'alésage d'entrée ; vérification de la résistance d'isolement du moteur électrique, de l'état des bagues collectrices, des porte-balais et des balais (pour les moteurs électriques à bagues collectrices), vérification de la largeur des fentes antidéflagrantes (espaces) entre les couvercles et le carter.
10.3. Révision
10.3.1. Une gamme typique de travaux lors de la révision des machines électriques comprend toutes les opérations de réparation courantes ; outre:
moteurs électriques asynchrones à rotor à cage d'écureuil : démontage complet du moteur électrique avec remplacement complet ou partiel des enroulements ; tourner les cols de l'arbre ou remplacer l'arbre du rotor ; équilibrage des rotors ; remplacement du ventilateur et des brides ; assembler le moteur électrique et le tester en charge ;
moteurs électriques asynchrones à rotor de phase : démontage complet du moteur électrique avec remplacement complet ou partiel des enroulements du stator et du rotor ; remplacement, si nécessaire, de l'arbre du rotor ; anneaux de cloison ; équilibrage des rotors ; réparation de dispositifs de fermeture et de contact; remplacement du ventilateur et des brides ; remplacement du mécanisme de la brosse ; assembler et peindre le moteur électrique et le tester sous charge ;
moteurs électriques asynchrones haute tension et synchrones : démontage complet du moteur électrique et élimination des défauts détectés ; excavation du rotor, réparation du rotor (fer du rotor et enroulement ou tiges de cage et bagues collectrices); réparation de roulements ; réparation de stator (fer et bobinage de stator); remplacement (partiel ou complet) des enroulements (bobines polaires) si nécessaire ; mesure et essai de la rigidité diélectrique de l'isolation des enroulements; réparation de refroidisseur d'air et de système de refroidissement; assemblage du moteur électrique et essai en mode de fonctionnement ;
Machines électriques à courant continu : démontage complet de la machine électrique ; unités et pièces de lavage; remplacement des cales à fente et des enroulements isolants défectueux ou leur réparation suivie d'au moins deux imprégnations ; redresser, tourner les cols ou remplacer l'arbre du rotor et réparer la "cage d'écureuil" ; réparation ou fabrication de flasques et de brides de paliers; bagues collectrices ou collecteur de cloison ; réparation et réglage des mécanismes de brosses; soudure complète des "coqs"; remplacement du ventilateur et des fixations ; vérification de la fixation du fer actif sur l'arbre et dans le stator et sa réparation si nécessaire ; montage et peinture de la machine électrique, essais selon GOST pour les nouvelles machines. Pour les machines électriques d'une puissance supérieure à 200 kW - démontage de la machine avec dépose de l'induit ou déplacement du système magnétique, réalisation de mesures et d'essais afin d'identifier les défauts ; nettoyage et imprégnation, séchage et peinture des bobinages; serrage et retournement du collecteur, recalage de l'ancre et remplacement des bandages en acier, remplissage ou remplacement des roulements; si nécessaire - rembobinage complet ou partiel des enroulements de la machine, cloison ou remplacement du collecteur ; équilibrage des ancres ; assemblage de machines; peinture extérieure, essai de la machine au ralenti et en charge.
10.4. Normes de fréquence, de durée et de complexité des réparations
La fréquence des réparations est établie pour les machines électriques fonctionnant dans des conditions normales de fonctionnement. Les normes de fréquence, de durée et de complexité de la réparation des machines électriques sont données dans le tableau. 10.1.
La complexité de la réparation dans le tableau. 10.1 est donné uniquement pour la réparation des machines électriques proprement dites, à l'exclusion de la réparation des ballasts et de la vitesse, des régulateurs de tension et des autres appareils de commutation, dont la complexité de réparation est fixée séparément.
Tableau 10.1
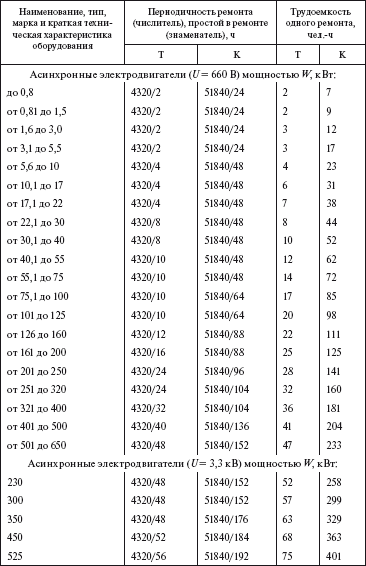
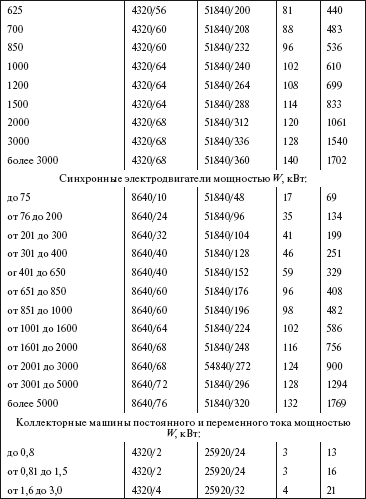
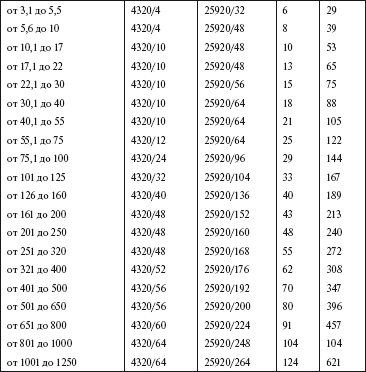
Remarques.
1. Pour les machines électriques fonctionnant dans des conditions difficiles (ateliers chauds, chimiques, galvaniques, de menuiserie, etc.), ainsi que celles utilisées avec de longs cycles de travail continu et avec un degré de charge élevé (entraînements de pompes, compresseurs, ventilateurs, climatiseurs, moteurs - générateurs, concasseurs, moulins, dragues, umformers, etc.) la révision doit être planifiée au moins après 17 280 heures, courant - au moins après 4 320 heures Il est permis de réparer les moteurs électriques qui font structurellement partie de l'équipement , conformément à la fréquence de réparation de cet équipement, si elle ne dépasse pas les valeurs indiquées dans le tableau. 10.1.
2. L'intensité de la main-d'œuvre et les temps d'arrêt dans la réparation des moteurs électriques asynchrones sont indiqués pour les moteurs électriques à rotor à cage d'écureuil. Pour les moteurs électriques à rotor phasé, les moteurs antidéflagrants, à plusieurs vitesses, submersibles et de grue, la complexité et les temps d'arrêt pour réparation sont pris avec un facteur de 1,3.
3. Des normes d'intensité de main-d'œuvre pour les réparations sont données pour les moteurs électriques avec des enroulements non volumineux en fonction de leur fourniture avec des sections préfabriquées. Pour les moteurs électriques à enroulements lâches, l'intensité de travail est prise avec un facteur de 1,8.
4. Les normes d'intensité de travail pour les réparations sont données pour les machines ayant une vitesse de rotation de 1500 tr/min. Pour les machines électriques à d'autres vitesses, les coefficients suivants sont introduits : 3000 tr/min - 0,8 ; 1000 tr/min - 1,1 ; 750 tr/min - 1,2 ; 600 tr/min - 1,4 ; 500 tr/min - 1,5.
5. La complexité de la réparation des moteurs électriques haute tension est donnée pour une tension de 3,3 kV. Pour les moteurs électriques d'une tension de 6,6 kV et plus, l'intensité de travail doit être prise avec un facteur de 1,3.
6. Pour les unités à deux, trois machines ou plus, les umformers, les moteurs-générateurs, la complexité de la réparation de l'unité dans son ensemble est considérée comme la somme des coûts de main-d'œuvre de la réparation de toutes les machines incluses dans l'unité (y compris l'entraînement ), multiplié par un facteur de 1,6.
11. ÉQUIPEMENT DE RÉFRIGÉRATION À COMPRESSEUR ET POMPES
La section comprend les compresseurs : air, ammoniac, fréon, détendeurs ; équipement auxiliaire; pompes : centrifuges, à piston, vortex, à vide, diverses.
La durée de vie utile des compresseurs est fixée à plus de 5 à 7 ans. Durée de vie utile des pompes : centrifuges, à piston et rotatives - de 5 ans à 7 ans, artésiennes et submersibles - de 3 ans à 5 ans, sol, sable, lisier, nutriment - de 2 à 3 ans.
11.1. Maintenance
11.1.1. L'entretien des équipements de compresseur-réfrigération et des pompes prévoit les travaux suivants: contrôle de l'absence de bruits et de coups parasites, vibrations anormales. Contrôle de la température des roulements, du niveau, de la pression et de la température de l'huile et de l'eau de refroidissement, de la qualité (couleur) de l'huile, de la température et de la pression d'air par étapes. Vérification de l'état extérieur de l'équipement, bon fonctionnement, accessible pour l'inspection des pièces mobiles. Contrôle de l'état de fonctionnement et de la position correcte des organes d'arrêt et des soupapes de sécurité, respect des modes de fonctionnement économiques et sûrs. Arrêt des équipements défectueux.
11.1.2. De plus, les travaux suivants sont réalisés pour certains types d'équipements :
compresseurs de tous types : nettoyage, rinçage des vannes. Remplacement des ressorts et plaques défaillants. Nettoyer les boîtiers de vannes de la suie et de la saleté. Vérifiez les sièges des soupapes et l'étanchéité des soupapes de fermeture. Vérification de la fiabilité de la fixation de la bague et de l'état des pièces de la traverse, de l'état du piston et de la tige, de la fiabilité de la fixation des joints de presse-étoupe et de pré-garniture, ainsi que des joints interbrides. Inspection et nettoyage du lubrificateur, clapets anti-retour dans l'oléoduc. Remplacement de l'huile contaminée, nettoyage et rinçage des filtres à huile et à air. Vérification de l'état de la fondation, des fixations d'ancrage, de la fiabilité des goupilles fendues des boulons de bielle et des boulons de contrepoids. Contrôle des écarts dans les roulements de vilebrequin, ainsi que des écarts dont le contrôle est prévu par les instructions d'usine lors de l'inspection de ce type de compresseur. Vérification de l'état des refroidisseurs intermédiaires et finaux, des séparateurs d'huile et d'eau, des unités de séchage d'air, des récepteurs ;
pompes centrifuges : vérifier le démarrage axial et la libre rotation de l'arbre, l'alignement de la pompe avec le moteur d'entraînement, ainsi que l'état des doigts de l'accouplement. Vérification du fonctionnement des soupapes d'admission et de contrôle. Élimination des fuites entre les sections dans les pompes sectionnelles multicellulaires. Serrage des boulons de guidage ;
pompes à vapeur alternatives : inspection et vérification du mécanisme de distribution de vapeur externe, de l'état des vannes d'aspiration et de refoulement. Reconditionnement des scellés. Nettoyer la grille de réception et vérifier les connexions des brides ;
vérification de l'état du condenseur, de l'évaporateur, du récepteur, du séparateur d'huile. Descente d'huile et d'air. Élimination des fuites dans les raccords à brides. Vérification du niveau d'ammoniac dans les évaporateurs à tubes verticaux et multitubulaires. Vérification de toutes les vannes d'arrêt et de contrôle. Nettoyage de la grille du collecteur de poussière. Vérification de l'état des dispositifs automatiques et de leur réglage. Vérification de l'état des blindages, du fonctionnement des pompes, des compresseurs et de l'état de toutes les communications.
11.2. Maintenance
11.2.1. La réparation actuelle de l'équipement de compresseur-réfrigération et des pompes est effectuée sur le site d'installation cet équipement; seuls les équipements de faible masse sont réparés dans des ateliers spécialisés (zones) de l'entreprise.
11.2.2. Une gamme typique de travaux de réparation lors de réparations en cours comprend des opérations de maintenance, un démontage partiel de l'équipement avec des réparations et le remplacement des pièces les plus usées. De plus, pour certains types d'équipements, la portée standard des travaux lors des réparations courantes comprend des travaux spécifiques à ce type d'équipement.
11.2.3. inspection des soupapes, ressorts, boîtes à air et nettoyage de la suie et de la saleté. Vérifiez l'étanchéité des vannes et essuyez les plaques. Vérification de l'état des sièges de soupapes. Lavage, nettoyage et (si nécessaire) réparation (remplacement) des roulements. Changement de l'huile contaminée, serrage des boulons du curseur et de la manivelle. Inspection et essuyage des robinets, vérification des joints entre les brides. Vérification des clapets anti-retour sur les conduites d'huile. Vérifier les fixations de toutes les pièces mobiles du compresseur. Inspection des arbres, nettoyage et lavage des filtres à air et à huile. Remplacement de la soupape ou des plaques de soupape. Vérifier la fixation des poids de manivelle, retirer les couvercles de cylindre, les nettoyer de la suie et nettoyer les endroits endommagés par le blocage. Rinçage, nettoyage des chemises de cylindre et des refroidisseurs intermédiaires du limon et du tartre. Nettoyer les pistons de la suie. Vérifier les soupapes et remplacer les pièces usées. Remplacement des aubes de travail et des anneaux de travail des compresseurs rotatifs. Couvertures de broyage de compresseurs rotatifs. Nettoyage du rotor des dépôts de carbone dans les compresseurs rotatifs, vérification et réglage des écarts de ces compresseurs. Vérification et réglage des espaces nocifs (morts) des compresseurs alternatifs, vérification et changement des mauvais ressorts de soupape. Vérification et réglage des régulateurs de pression. Vérifier la conicité, l'ellipticité et la réparation du tourillon d'arbre (si nécessaire). Vérification de l'intégrité des goujons du palier principal, vérification des boulons de bielle, vérification de la fixation des écrous de piston fixés au piston. Nettoyage du carter du lit, vérification de l'alignement du compresseur avec le moteur électrique. Assemblage et peinture.
11.2.4. Turbocompresseurs et turbosoufflantes : démontage du limiteur de vitesse, démontage et nettoyage du compresseur. Démonter le carter et le laver de la suie et de la saleté. Vérification de l'état du système de refroidissement, de la densité des connexions avec le remplacement des joints. Vidange.
11.2.5. Machines et groupes frigorifiques : ouverture, contrôle interne et l'élimination des défauts détectés dans le séparateur d'huile, le condenseur, le récepteur et l'évaporateur. Remplacement de tubes individuels dans le condenseur et l'évaporateur. Élimination complète de l'huile, de la saleté et du tartre du condenseur. Vérifier le récepteur et le système pour les fuites. Remplacement des fixations et des joints. Vérification des fixations des coques aux structures porteuses.
11.2.6. Pompes centrifuges : déconnexion du moteur électrique, déconnexion du réseau. Démontage de l'accouplement, des roulements et des sections de pompe, inspection et vérification de toutes les pièces. Surveillance de l'accélération axiale du rotor et des jeux dans les joints et les roulements, vérification de l'arbre. Contrôler le montage du rotor, le démontage et l'atterrissage de l'attelage avec clavettes et rainures de clavette. Remplacement du presse-étoupe (chemisage sur l'arbre) sans démonter et monter d'autres pièces, remplacer les boulons de l'accouplement, remplacer la bague supplémentaire (deux demi-bagues) de la pompe. Équilibrage statique de la roue, alignement de la pompe avec un moteur électrique. Test de la pompe.
11.2.7. Pompes à pistons : inspection et essai du mécanisme de distribution de vapeur externe. Vérification de l'étanchéité de la vanne d'arrêt de la vapeur, vérification et nettoyage de la crépine d'aspiration, vérification des raccords à bride, regarnissage des presse-étoupes. Inspection des vannes d'aspiration et de refoulement. Changement des goujons et écrous des caches cylindres, meulage des rayures et encoches des coussinets. Démonter le piston, vérifier les fixations de la tige et connecter les segments de piston, changer et rectifier les segments de piston, refixer la tige. Changement de presse-étoupe, de cloison, rodage et test de pression de la vanne d'arrêt vapeur et du mécanisme de transmission. Changement des pivots. Rasage et polissage du miroir des bobines. Changer l'axe ou le siège, percer le siège de la vanne d'arrêt de la vapeur, changer les fixations et les brides de la ligne de vapeur. Remplacement ou réparation du purgeur de vapeur. Révision de la vanne de réception. Nettoyage, rinçage, test de pression de la conduite d'aspiration. Assemblage et test de la pompe.
11.3. Révision
11.3.1. La révision comprend les réparations en cours, le démontage complet du matériel, le lavage, le dépannage des pièces, le remplacement des pièces inutilisables.
Après une révision majeure, les équipements soumis aux exigences de Rostekhnadzor sont soumis à des tests appropriés et présentés aux représentants de Rostekhnadzor. De plus, les travaux suivants sont réalisés par type d'équipement.
11.3.2. Compresseurs à pistons et rotatifs : démontage des paliers principaux, leur remplissage et réglage. Démontage et enlèvement du volant moteur, de l'évidement du vilebrequin, de l'alésage du cylindre. Remplacement de piston, enlèvement, nettoyage et remplacement de segments de piston usagés. Vérifier les rainures et monter de nouveaux segments de piston. Vérification de l'ellipticité, de la conicité et de leur réparation des axes de piston et de traverse. Déconnecter la tige de piston et la rectifier sur la machine. Montage de tous les roulements et leur remplissage. En vérifiant le diamètre et la longueur de la tige, si nécessaire, réparez-la ou remplacez-la par une neuve. Vérification de la position correcte de la bielle par rapport à l'arbre et au piston et élimination des déformations. Vérification et rinçage au kérosène des conduites d'huile, des raccords de graissage et des pièces usées la pompe à huile. Tournage et meulage des tourillons principaux et de bielle du vilebrequin. Nettoyage de la saleté et du tartre de toutes les surfaces de refroidissement. Inspection et test des refroidisseurs intermédiaires et post-refroidissement et remplacement des tuyaux et serpentins usés. Inspection et nettoyage du réservoir d'air des séparateurs huile-eau et des purgeurs de vapeur et leur réparation. Nettoyage des conduites de refoulement du compresseur au récepteur de la saleté, des dépôts de carbone et de l'huile. Inspection, réparation et test d'étanchéité de toutes les vannes. Vérification de la fixation du châssis, du compresseur et de l'état des boulons de fondation. Inspection et réparation de toutes les soupapes de sécurité et régulateurs de pression. Assemblage et peinture.
Après une révision majeure, le compresseur est testé selon un programme qui vérifie la qualité de la réparation, l'état du système de contrôle, le contrôle de capacité et la protection d'urgence.
Toutes les données sur les réparations effectuées et les résultats des tests doivent être enregistrées dans le journal du compresseur, et les données sur la réparation et les tests du collecteur d'air - dans le passeport du collecteur d'air.
11.3.3. Turbocompresseurs et soufflantes : démontage complet, remplacement du disque, vérification de l'arbre, réparation ou remplacement. Réparation du compresseur et du système de refroidissement. Équilibrage dynamique du rotor et de la roue.
11.3.4. Machines et groupes frigorifiques : démontage complet et réparation avec remplacement des plaques tubulaires et des tubes du condenseur et de l'évaporateur. Rinçage et nettoyage du séparateur d'huile, du collecteur d'impuretés, du carter d'huile, du vase intermédiaire et de la pompe de circulation. Purge des batteries de refroidissement et leur réparation avec remplacement des tuyaux et brides. Nettoyage des surfaces externes des batteries de la rouille et de la vieille peinture, séchage et peinture. Réparation des supports de batterie et des structures de support d'autres appareils.
11.3.5. Pompes centrifuges : démontage complet de la pompe, démontage du rotor. Réparation des disques et boîtiers, remplacement des disques usés et autres pièces. Remplacement des roulements, des fixations et des joints.
11.3.6. Pompes à pistons : alésage des coussinets de cylindre, changement ou réparation des pistons et plongeurs. Montage ou remplacement de tringles, révision complète de la boîte à bobine et sa réparation. Remplacement des segments de piston, remplissage ou remplacement des coussinets de palier.
11.4. Normes de fréquence, de durée et de complexité des réparations
11.4.1. La fréquence des réparations courantes et majeures des équipements de compresseur-réfrigération et des pompes dépend en grande partie de l'objectif et du type de vecteur d'énergie. Pour les pompes centrifuges, la fréquence des réparations est donnée lors de leur pompage eau froide. Lors de l'utilisation de pompes centrifuges dans d'autres conditions, la fréquence des réparations doit être prise comme suit :
pour le pompage eau chaude J= 2160h, K= 25 920 heures ;
pour le pompage d'eau agressive et d'essence T = 2160 heures K= 17 280 heures ;
pour liquides et acides chimiquement actifs T = 1440 heures K= 8640 heures.
11.4.2. La complexité de la réparation de l'équipement et des pompes de compresseur-réfrigération est indiquée dans le tableau. 11,1 hors frais de main-d'œuvre pour la réparation des moteurs électriques et à vapeur et des équipements de démarrage.
Tableau 11.1

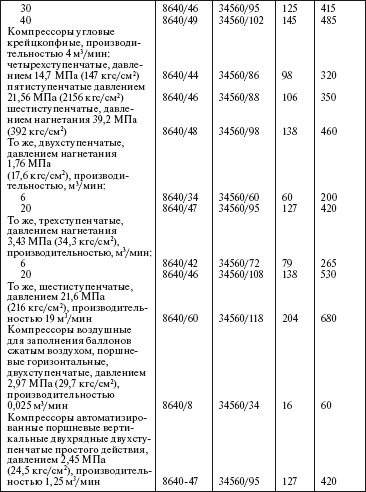

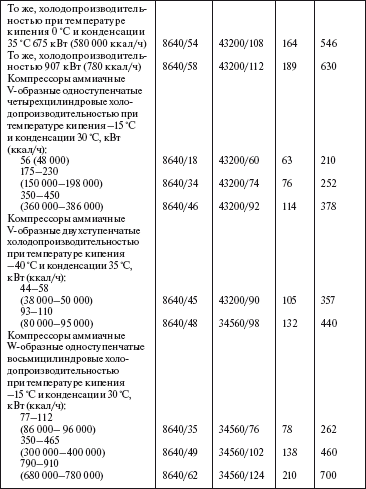


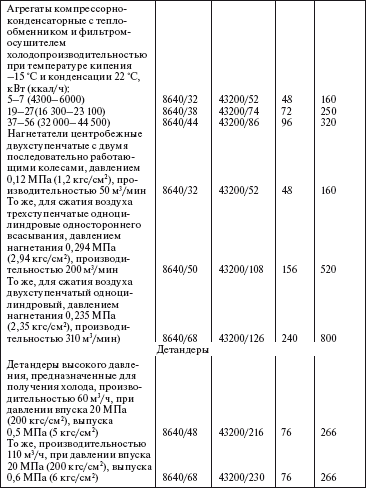
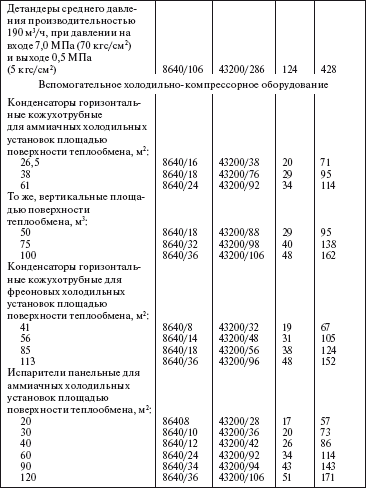

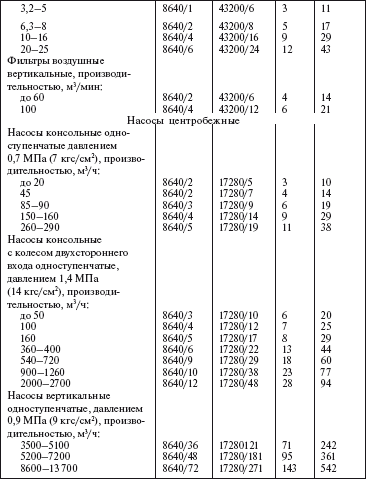
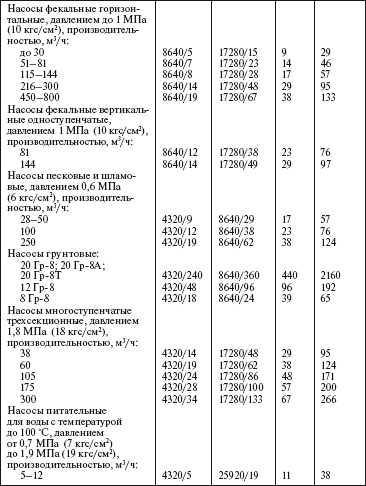


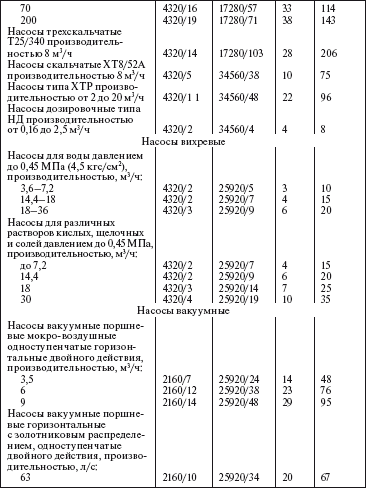
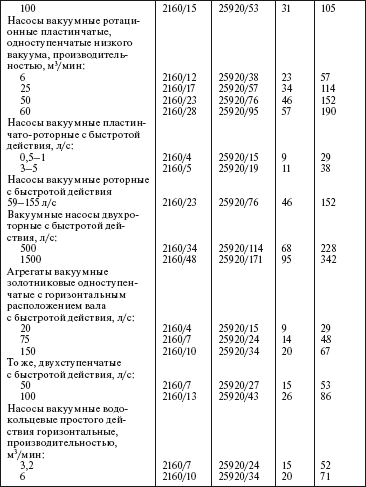
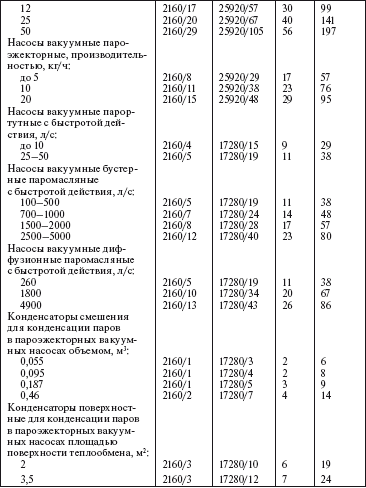

Remarques:
1. Les normes d'intensité de main-d'œuvre pour la réparation des pompes en porte-à-faux pour les acides, les alcalis et les pompes en porcelaine sont acceptées avec un facteur de correction de 1,2.
2. L'intensité du travail de réparation des pompes artésiennes est augmentée de 5 % pour chaque étape subséquente sur six étapes pour les pompes submersibles et trois étapes pour les pompes électriques au-dessus du puits.
3. La complexité de la réparation des pompes à plusieurs étages avec plus de trois sections augmente de 5% pour chaque paire de sections suivante.
12. ÉQUIPEMENT DE VENTILATION ET DE CLIMATISATION
Les équipements inclus dans la section appartiennent au cinquième groupe d'amortissement avec une durée d'utilité supérieure à 7 ans à 10 ans inclus.
12.1. Maintenance
12.1.1. Lors de la maintenance des équipements des systèmes de ventilation et de climatisation, les types de travaux suivants sont effectués: surveillance quotidienne du fonctionnement des équipements et inspections programmées des équipements.
12.1.2. Les travaux suivants sont effectués dans l'ordre de la surveillance quotidienne : contrôle de la mise en œuvre des consignes d'exploitation des systèmes ; le bon sens de rotation des ventilateurs, l'absence de bruit, de vibration et d'aspiration anormaux ; contrôle de la position des vannes et des papillons des gaz ; température du liquide de refroidissement et du réfrigérant fournis à l'unité ; contrôle de l'absence de fuite dans les réchauffeurs, les évaporateurs, dans la chambre d'irrigation et les canalisations de la chambre d'alimentation ou de l'unité de conditionnement d'air ; contrôle de la mise en marche et de l'arrêt en temps opportun des systèmes de ventilation et des dispositifs d'admission d'air individuels; réajustement des systèmes en cas de violation des paramètres spécifiés de l'environnement aérien dans les locaux habités avec fixation des opérations effectuées dans le journal des opérations.
12.1.3. Des inspections programmées pour les équipements situés dans les salles des machines avec un entretien constant sont effectuées à chaque quart de travail, et pour le reste de l'équipement, la fréquence des inspections est attribuée en fonction des conditions locales, mais au moins une fois par mois. Pour les installations classées comme équipement principal (systèmes de ventilation et installations de conditionnement d'air des locaux fermés, zones à risque d'explosion et d'incendie, ainsi que les zones utilisant des substances toxiques) - au moins une fois tous les 10 jours.
Pour les unités de récupération de gaz situées derrière les équipements de procédé, une inspection est effectuée une fois tous les 3 mois avec la participation de médecin sanitaire et l'acte est dressé.
12.1.4. La portée des inspections effectuées selon le calendrier approuvé, en tant qu'opérations indépendantes, comprend les travaux suivants : surveillance de l'état des roulements, des accouplements, des poulies, des transmissions par courroie, des supports de ventilateur et de l'état de fonctionnement des dispositifs d'amortissement des vibrations ; inspection du carter du ventilateur ; surveiller l'état des pales du rotor, des réchauffeurs, des évaporateurs, des vannes, des buses et de la chambre d'irrigation ; vérifier les jeux entre le rotor et le carter du ventilateur ; vérification de l'état, ainsi que (en présence d'un manomètre à liquide monté à demeure) de la résistance des filtres, de l'étanchéité des cassettes filtrantes au cadre, de la propreté des espaces arrière-filtres ; vérifier l'état de fonctionnement du mécanisme de déplacement des filtres à huile autonettoyants, le degré de contamination et le niveau d'huile dans le bain de filtre, l'état de fonctionnement des mécanismes d'agitation des filtres à manches ; vérifier l'exactitude et la fiabilité du fonctionnement des vannes, des vannes, des vannes, des papillons et de leurs mécanismes de commande; vérifier l'étanchéité des chambres, l'état et l'intégrité de l'isolation thermique des chambres, des collecteurs, des conduits d'air, des conduites de chaleur et de froid ; vérification de l'intégrité des connecteurs flexibles, des conduits d'air, de l'étanchéité des raccordements des conduits d'air et de la présence de joints d'étanchéité ; contrôle de l'état des peintures et revêtements anti-corrosion ; nettoyage de dispositifs de réception et de dépoussiérage, chambres de dépoussiérage, grilles, grilles de ventilation et persiennes; vérification de la résistance des puits de fixation, des tuyaux, des déflecteurs, des conduits d'air suspendus ; contrôle sélectif du degré de contamination des conduits d'air.
12.2. Maintenance
12.2.1. Au cours de la réparation en cours, des opérations de maintenance sont effectuées, ainsi que les travaux suivants sur les types d'équipements énumérés ci-dessous.
12.2.2. Systèmes d'aération : arrêt et démontage partiel du système de ventilation, réparation des bosses, scellement des trous et des endroits corrodés dans les enveloppes des chambres de ventilation, des collecteurs, des conduits d'air, des puits de ventilation, des cyclones, des épurateurs, des hottes d'extraction et d'autres dispositifs en tôle (acier, plastique vinylique, etc.); réparation de joints cassés à brides, rivetés, collés et soudés; serrage complet de toutes les connexions boulonnées, remplacement des brides, boulons, joints, inserts flexibles, fixations (supports de suspension, pinces, supports, etc.) inutilisables ; réparation des déblais aux endroits où les puits de ventilation et les conduits d'air traversent le toit et d'autres structures de construction; réparation et remplacement des plafonds de ventilation endommagés et installation des plafonds de ventilation manquants, buses, grilles, aspiration locales, filets, déflecteurs, ainsi que réglage de leur position, espaces et sections ; réparation de mécanismes de fixation et de réglage; nettoyage complet des conduits d'air, ventilateurs, radiateurs et autres éléments des systèmes de ventilation; réparation des finitions, des éléments structurels et des portes des chambres de ventilation. Nettoyage, lavage et lubrification des filtres à viscine, remplacement des matériaux filtrants ou des cassettes par des filtres de réserve, suivi de la réparation et de la recharge de ceux qui ont été retirés ; changement d'huile dans les réservoirs de filtres autonettoyants ; réparation du mécanisme d'agitation des filtres à manches avec remplacement des pièces usées ; nettoyer les buses des buses de la chambre d'irrigation ; remplacement des injecteurs endommagés, réglage de leur installation; réparation de tubes à ailettes d'appareils de chauffage et d'évaporateurs; soudage ou remplacement de tuyaux éclatés ; lubrification de tous les mécanismes et essieux ; nettoyage de la rouille de tous les éléments corrodés des systèmes de ventilation et restauration des vibrations locales des conduits d'air et des ventilateurs.
12.2.3. Aspirateurs de fumée : inspection et vérification de l'extracteur de fumée avant arrêt avant réparation, mesure des vibrations. Roulements d'ouverture et trappes sur la volute et les poches d'aspiration. Démontage, inspection, réparation et montage des aubes directrices axiales et des vannes de régulation. Vérification de l'état des pièces du rotor, des roulements, des volutes et de leur réparation (rétablissement de la fixation des aubes et de la roue, redressage des aubes, surfaçage local des aubes, colmatage des fuites des blindages, des volutes, des poches et autres petits réparations). Réparation des roulements du système de refroidissement et des raccords, des moitiés d'accouplement. Dépose du demi-accouplement, contrôle et nettoyage du siège de l'arbre, correction ou remplacement de la clavette. Retrait de la roue de l'arbre avec le moyeu, vérification et nettoyage du siège de l'arbre, réparation de la rainure de clavette, réparation ou remplacement de la clavette. Installation d'une turbine neuve ou remise à neuf avec un moyeu sur l'arbre. Rechargement des aubes de roue avec des alliages résistants à l'usure. Remplissage des coussinets de roulement. Mise en place et grattage des chemises le long de l'arbre après remplissage et retournement. Rechargement du col de l'arbre, usinage, rectification et inspection. Rechargement des armures, des volutes et des poches d'aspiration avec un alliage résistant à l'usure. Redressement d'arbres avec chauffage par brûleurs à gaz. Restauration des écarts normaux entre la roue et les diffuseurs, fixation des roulements et des trappes sur la volute et les poches.
12.2.4. Ventilateurs: inspection et essai des ventilateurs avant l'arrêt et mesure des vibrations. Détachement et déploiement du moteur électrique. Vérification de l'aube directrice axiale et de son entraînement, mesure des écarts entre le diffuseur et la roue et inspection de la roue. Étanchéité des escargots de ventilateur et des boîtes à air. Vérification des roulements avec changement des joints et mesure des jeux, vérification du niveau d'huile. Si nécessaire, remplissage des coquilles de paliers lisses, remplacement des roulements à billes et à rouleaux, remplacement des aubes de classe de travail défectueuses, alésage et meulage des cols d'arbre, réparation du carter et de la volute, réparation des dispositifs de refroidissement, vérification du faux-rond axial et radial de l'accouplement moitié. Remplacement des douilles élastiques sur les doigts du demi-accouplement ou remplacement des doigts. Démontage et montage du demi-accouplement, nettoyage et vérification du siège de l'arbre, réparation de la rainure de clavette, réparation ou remplacement de la clavette. Équilibrage dynamique du rotor. Assemblage, installation et alignement du moteur électrique. Test du fonctionnement du ventilateur inactif.
12.2.5. Superchargeurs : inspection externe du compresseur, élimination des défauts constatés, inspection des fixations, remplissage ou remplacement des coussinets, inspection des accouplements, tournage ou meulage des cols d'arbre, remplacement des aubes individuelles ou de leur soudage, réparation du carter, de l'isolation, des dispositifs de refroidissement ; équilibrage des rotors.
12.2.6. Conditionneurs : inspection externe du climatiseur, nettoyage de la poussière et de la saleté, enlèvement et, si nécessaire, réparation des panneaux et des caissons de volets, démontage partiel du climatiseur, inspection, nettoyage, test et, si nécessaire, réparation de l'unité de condensation, électrique réchauffeur (climatiseurs autonomes), pompe, refroidisseur d'air, collecteur d'humidité, réchauffeur d'air (climatiseurs non autonomes), ventilateur, filtre à huile, canalisations, raccords, fils, système d'automatisation, collecteur ; ajustement et ajustement.
12.2.7. Soufflantes (soufflantes à gaz): retrait des tuyaux d'échappement et nettoyage de la suie; inspection des pièces de refroidissement (disque réflecteur de chaleur, courroie aéraulique et entraînement du limiteur de vitesse) et, si nécessaire, leur remise en état ; démontage du limiteur de vitesse, inspection et remplacement des pièces usées ; démontage de la pompe à huile et du compresseur, inspection, rinçage, remplacement des pièces usées ; inspection du récepteur et élimination des défauts détectés (en particulier dans les lieux de fixation et de soudage); réparation des roulements et les laver à l'huile de turbine.
12.3. Révision
12.3.1. Lors de la révision des systèmes de ventilation, des opérations de maintenance sont effectuées et, en outre, le remplacement d'au moins 30% des conduits d'air, des échappements locaux, des plafonds de ventilation, des buses, des parapluies, des déflecteurs, des réchauffeurs, des évaporateurs, des buses et d'autres composants et éléments structurels et assemblages de systèmes de ventilation et de systèmes de climatisation jusqu'au remplacement de sections individuelles de climatiseurs ; nettoyage complet des chambres, des équipements, des dispositifs de dépoussiérage et de dépoussiérage des échappements locaux, des abris, des conduits d'air de la poussière, de la saleté, des boues et de la peinture écaillée; équipement de peinture du système de ventilation; assemblage du système ; tester des nœuds individuels et le système dans son ensemble ; essais et réglage de la production.
12.3.2. Ventilateurs et extracteurs de fumée : enlèvement et démontage complet ; Dépanner les pièces et, si nécessaire, remplacer les pièces inutilisables, y compris la roue, le logement de roulement, les roulements, les parois de volute usées, les poches d'aspiration, les volutes, etc. ; démontage du moteur électrique et envoi à l'atelier électrique pour réparation et test. Assemblage de ventilateurs et d'extracteurs de fumée, inspection, essais, peinture.
12.3.3. Superchargeurs : démontage complet, remplacement des pièces et ensembles usés, réparation du carter et du rotor, remplacement des carters de paliers d'arbre, montage et essais en fonctionnement.
12.3.4. Conditionneurs : remplacement pièces individuelles, composants et assemblages, installation de ventilateurs, recâblage du système de contrôle, assemblage, réglage, réglage et peinture.
12.3.5. Soufflantes (soufflantes à gaz): démontage complet des unités et des ensembles, inspection et élimination des défauts détectés, remplacement des pièces inutilisables et réparation à restaurer ; remplacement des boulons de fixation du disque et de l'arbre, des roulements ; équilibrage dynamique des pièces, vérification du faux-rond du disque rotor et de la roue, assemblage et essais.
12.4. Normes de fréquence, de durée et de complexité des réparations
12.4.1. Des normes relatives à la fréquence, à la durée et à la complexité de la réparation des systèmes de ventilation sont élaborées pour les conditions de leur fonctionnement avec des ventilateurs centrifuges. Ces normes (tableau 12.1) sont établies différemment pour les systèmes de ventilation avec certain nombre dispositifs de réception et de lancement d'air. Pour un dispositif d'entrée ou de sortie d'air, on prend classiquement un dispositif pour refouler (entrée) un volume d'air égal à 500 m 3 /h. Si les performances de l'appareil sont supérieures à 500 m 3 / h, chaque 500 m 3 / h ultérieur est assimilé à un appareil (entrée d'air ou sortie d'air).
Tableau 12.1

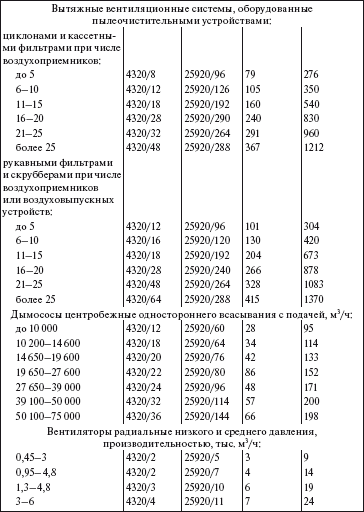
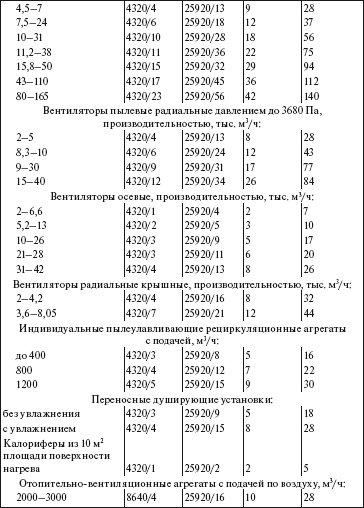
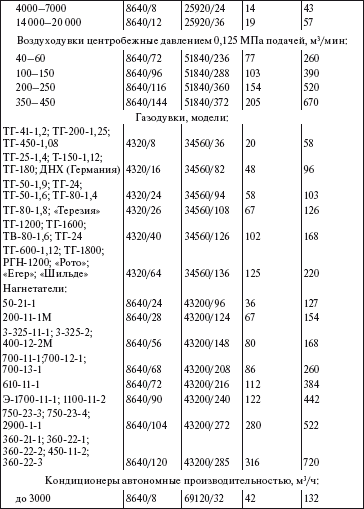
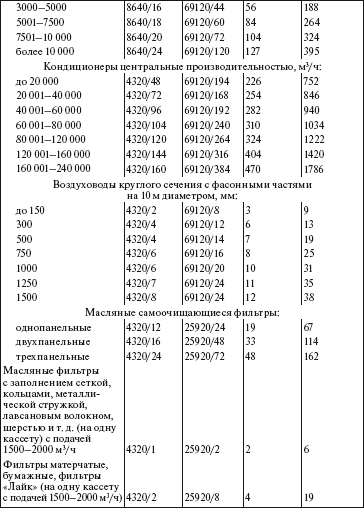

Remarques:
1. Pour les fans haute pression, poussière, dans les versions anticorrosion et spéciales, un coefficient de 1,5 est introduit dans les normes d'intensité de travail des réparations en capital et en cours.
2. Pour les climatiseurs de type bloc (type KT), un coefficient de 0,85 est introduit pour les grosses réparations et de 0,9 pour les réparations courantes.
3. Les normes d'intensité de travail pour la réparation des conduits rectangulaires sont prises selon les normes pour les conduits ronds de la même section. En fonction du matériau des conduits d'air, les facteurs de correction suivants sont introduits dans la norme d'intensité de travail des réparations en capital et en cours pour les conduits d'air en fer de toiture - 0,75, pour les conduits d'air en acier inoxydable - 1,3.
4. Les normes d'intensité de travail de réparation des systèmes de ventilation équipés d'échappements locaux et de buses doivent être appliquées avec un coefficient de 1,4.
5. Les normes d'intensité de travail pour la réparation des systèmes de ventilation équipés de ventilateurs axiaux sont acceptées avec un coefficient de 0,85.
13. CANALISATIONS PUBLIQUES
La section comprend les types de canalisations suivants: réseaux externes et internes d'alimentation en eau froide et chaude, canalisations de mazout, réseaux de chauffage, réseaux de chauffage, canalisations de vapeur, eaux usées fécales et industrielles, raccords de canalisation à usage général, qui appartiennent au septième amortissement groupe avec une durée de vie de 15 à 20 ans inclus.
L'entretien et la réparation de certains types de canalisations doivent être effectués conformément aux exigences des directives de Rostekhnadzor pour ce type d'équipement.
Lors de l'exploitation et de la réparation de conduites de vapeur avec une pression supérieure à 0,2 MPa (2 kgf / cm 2) et d'eau chaude à une température supérieure à 115 ° C, il est nécessaire d'être guidé par les exigences des règles de construction et Exploitation sécuritaire des conduites de vapeur et d'eau chaude.
Tous les systèmes de canalisations soumis à enregistrement auprès des autorités locales de Rostekhnadzor doivent avoir des passeports dans lesquels le personnel d'exploitation consigne les défauts constatés et les réparations effectuées.
Les conduites de vapeur et d'eau chaude enregistrées auprès de Rostekhnadzor sont soumises à un examen technique par un inspecteur-ingénieur en prochaines dates: examen externe - au moins 1 fois en 3 ans ; inspection externe et test hydraulique - avant la mise en service de la canalisation nouvellement installée après réparation associée au soudage des joints, et lors du démarrage de la canalisation après qu'elle ait été dans un état de conservation de plus de 2 ans.
Si l'entreprise dispose de canalisations en verre, des instructions d'exploitation, de réparation et de sécurité doivent être élaborées en fonction des exigences de cette production, en tenant compte des propriétés du verre.
Les entreprises recevant de l'énergie thermique provenant de chaufferies urbaines ou de centrales thermiques doivent respecter les règles d'exploitation et de réparation en vigueur dans ces entreprises.
13.1. Maintenance
13.1.1. Pipelines. L'étendue de la maintenance par types de canalisations comprend les travaux suivants : inspection externe des canalisations pour détecter les fuites dans les joints soudés, les joints à brides et l'état de l'isolation thermique et du revêtement anti-corrosion. Réparation mineure des raccords de canalisation en position de travail ; remplacement des vannes d'arrêt défectueuses, des volants, reconditionnement des presse-étoupes et remplacement des parois de douche. Vérification du fonctionnement des purgeurs de condensats et d'un point de chauffe. Réglage du système de chauffage. Vérifier l'état de fonctionnement des séparateurs d'huile et d'eau installés sur les conduits d'air comprimé et en évacuer le condensat. Vérification de l'état des sorties d'égout et de la densité des prises et des colonnes du viaduc. Serrage des fixations de fondation des colonnes, supports mobiles et fixes de la canalisation. Remplacement des agrafes individuelles. Réparation d'escaliers. Vérification de l'état des bouches d'incendie, de l'étanchéité des raccordements des gazoducs dans les puits (à l'aide d'une émulsion savonneuse), des protections électriques des canalisations.
13.1.2. Réseaux d'égouts :éliminer les blocages et vérifier le fonctionnement des neutraliseurs et des bacs à graisse.
13.1.3. Chauffe-eau: vérifier l'étanchéité des couvercles, des raccords et le fonctionnement des instruments de mesure.
13.2. Maintenance
13.2.1. L'étendue des travaux pour la réparation courante de tous les types de canalisations comprend toutes les opérations de maintenance, ainsi que les travaux suivants : élimination des défauts identifiés lors de la maintenance ; remplacement de sections individuelles de pipelines (pas plus de 20% de sa longueur); remplacement partiel des brides, des joints et des raccords défectueux ; changement de garniture de presse-étoupe dans les raccords et les compensateurs ; réparation de supports mobiles et fixes de canalisations, isolation thermique; restauration du revêtement anti-corrosion ; test de densité, test de résistance hydraulique et coloration partielle.
13.2.2. Pour certains types de canalisations, raccords de canalisation, les travaux suivants sont en outre effectués :
conduites d'air comprimé : nettoyage des pipelines des gisements de pétrole avec une solution à 5% de soude caustique, suivi d'un rinçage à l'eau chaude; réparation de séparateurs d'huile et d'eau;
réseaux de chauffage : rinçage du système de canalisations, remplacement de groupes individuels de radiateurs ou de tubes à ailettes, vannes de régulation ; réparation de tuyaux de vidange et d'air, de plongeurs et de vases d'expansion;
canalisations externes : réparation des puits, colonnes métalliques du viaduc ; remplacement partiel des fixations ; réparation de supports mobiles et fixes, d'isolation thermique et de son revêtement de finition ; inspection et réparation de pompes hydrauliques incendie.
13.2.3. Réseaux d'égouts : réparation du système de canalisation, des neutraliseurs et des trappes à graisse, des puits, des colonnes métalliques du viaduc ; remplacement partiel des fixations ; réparation de supports mobiles et fixes, d'isolation thermique et de son revêtement de finition ; inspection et réparation de pompes hydrauliques incendie; réparation et remplacement partiel d'équipements électriques dans un dispositif de protection électrique.
13.2.4. Raccords : démontage, nettoyage et lavage de toutes les pièces ; remplacement des pièces usées ; rodage des soupapes et des bouchons de robinets ; rupture de joints d'huile; vérification du fonctionnement de la tête d'entraînement et de sa réparation.
13.2.5. Chauffe-eau: inspection interne de l'état des bobines des radiateurs capacitifs, remplacement partiel des tubes ; remplacement des joints et des fixations ; réparation d'isolation thermique et de raccords.
13.3. Révision
13.3.1. Pour tous les types de canalisations, le périmètre des travaux de grosses réparations comprend toutes les réparations en cours, ainsi que les travaux suivants : démantèlement d'une canalisation devenue inutilisable et pose d'une nouvelle canalisation d'un montant supérieur à 20 % de la longueur de cette section du pipeline ; remplacement des raccords, des brides, des joints des compensateurs de presse-étoupe, des supports mobiles et fixes ; restauration complète du revêtement anti-corrosion et de l'isolation thermique ; test hydraulique avec livraison aux organismes locaux de Rostekhnadzor ; peindre les canalisations dans des couleurs correspondant à leur destination.
13.3.2. Pour des types spécifiques de canalisations et de raccords, les travaux suivants sont en outre effectués :
conduits d'aération : remplacement des séparateurs d'huile et d'eau ; réparation de déshumidificateurs et leur recharge; détermination des fuites d'air en général dans tout le système de conduits d'air avant et après réparation ;
canalisations externes : remplacement des colonnes métalliques sujettes à une forte corrosion ; remplacement du revêtement supérieur d'isolation thermique; remise en place de la partie supérieure des puits, remplacement des agrafes et des échelles ; réparation d'armoire de protection électrique pour canalisations, réseaux câblés, transformateur, équipement basse tension;
réseaux d'égouts : vérifier la présence de pentes appropriées et, si nécessaire, poser des tuyaux sur les sections principales, réparer les puits et les plateaux ;
raccords : démontage complet des raccords ; remplacement ou réparation de pièces individuelles ; alésage des surfaces des brides et des surfaces des sièges de soupape ; remplacement des paires d'engrenages des têtes d'entraînement ; réparation ou remplacement du mécanisme d'entraînement et du moteur électrique ;
Chauffe-eau: démontage complet; nettoyage du tartre et des boues ; remplacement des serpentins et des chauffe-eau capacitifs.
13.3.3. Après des réparations majeures et en cours, les conduites de vapeur et d'eau chaude doivent être testées dans la mesure établie par les "Règles pour la conception et l'exploitation sûre des conduites de vapeur et d'eau chaude", et les conduites de gaz - dans la mesure établie par les "Règles de sécurité dans l'industrie du gaz ».
13.4. Normes de fréquence, de durée et de complexité des réparations
13.4.1. Les normes relatives à la fréquence, à la durée et à la complexité de la réparation des canalisations, des raccords de canalisation et des équipements sanitaires sont indiquées dans le tableau. 13,1 (par 100 mètres linéaires de longueur de canalisation).
13.4.2. La fréquence de réparation des canalisations et des raccords de canalisation a été adoptée ajustée en tenant compte de la durée modifiée du cycle de réparation, ajustée en fonction de la durée de vie modifiée des tuyaux en acier et en fonte.
13.4.3. La valeur maximale du cycle de réparation pour les pipelines d'une durée de vie de 20 ans est de 129 600 personnes. - h (14 ans), et pour une durée de vie inférieure à 20 ans - 103 680 - 86 400 personnes. – h (12–10 ans).
13.4.4. Pour les canalisations constituées de tuyaux en polyéthylène, revêtues de caoutchouc et revêtues de plastique vinylique, de polyéthylène et de fluoroplastique, soumises à un fonctionnement continu, la fréquence de révision doit être prise égale à la fréquence de réparation des canalisations constituées de tuyaux en acier des réseaux internes et externes avec un coefficient de 0,75.
13.4.5. La complexité de la réparation des canalisations est donnée sans tenir compte de la réparation des raccords de canalisations industrielles. La complexité de la réparation des canalisations externes est donnée sans tenir compte de la mise en œuvre des travaux d'excavation et de construction.
Tableau 13.1


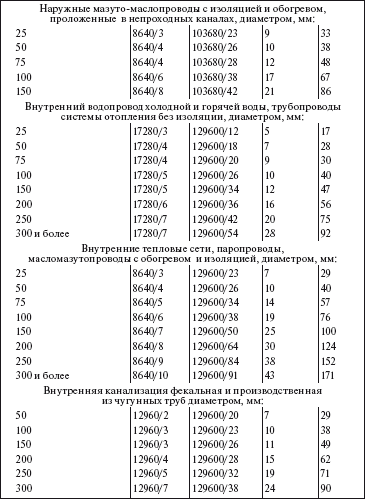
14. MATERIEL ROULANT DE TRANSPORT ROUTIER
Conformément à la réglementation en vigueur charges d'amortissement pour le matériel roulant de transport routier (ci-après dénommés voitures), les durées d'utilité suivantes sont établies :
3 à 5 ans : camions usage général capacité de charge jusqu'à 0,5 t inclus ;
sur 5 à 7 ans : camions d'une capacité de charge supérieure à 0,5 à 5 tonnes, tracteurs pour semi-remorques, fourgons, camions-bennes, camions-citernes, véhicules spéciaux et spécialisés, remorques et semi-remorques, bus jusqu'à 7,5 m de longueur compris; voitures particulières d'une cylindrée inférieure ou égale à 3,5 litres inclus ;
sur 7 à 10 ans : voitures capacité de chargement plus de 5 à 15 tonnes inclus ; véhicules tracteurs avec une charge de camion jusqu'à 7,5 tonnes; voitures à selle avec accessoires pour le nettoyage urbain; les bus d'une longueur supérieure à 7,5 à 12 m inclus ; voitures particulières d'une classe large et supérieure avec une cylindrée supérieure à 3,5 litres;
sur 10 à 15 ans : camions d'une capacité de charge supérieure à 15 tonnes ; véhicules tracteurs avec une charge à la selle de plus de 7,5 tonnes; bus d'une longueur supérieure à 16,5 m jusqu'à 24 m inclus.
Dans les limites de la durée d'utilité indiquée ci-dessus, les entreprises indépendamment, sur la base de l'expérience d'exploitation, établissent pour chaque unité du matériel roulant normes individuelles Cours. Les tournées annuelles de l'entreprise sont planifiées sur la base de l'expérience des années précédentes d'utilisation du matériel roulant. En l'absence de telles informations, vous pouvez utiliser les données moyennes du pays : 40 000 km par an pour camions; 70 000 km - pour les bus et voitures-Taxi; 20 000 km - pour les spéciaux et véhicules spécialisés.
Pour les véhicules spéciaux et spécialisés dont l'utilisation est enregistrée en heures, le kilométrage doit être recalculé à raison d'une heure - 25 km.
La planification de l'entretien, du courant et de la révision, les normes et standards pour leur mise en œuvre sont strictement liés au kilométrage des véhicules établi comme uniforme pour des conditions de fonctionnement moyennes. Pour les conditions d'exploitation autres que moyennes, le "Règlement sur l'entretien et la réparation du matériel roulant de transport routier" fournit des facteurs de correction et d'autres informations nécessaires.
Le principal impact technique du système d'entretien et de réparation des véhicules est l'entretien, qui est effectué de force à des kilométrages ou à des intervalles de fonctionnement du véhicule établis. Il s'agit d'une mesure préventive et est effectuée pour maintenir le véhicule en état de fonctionnement, assurer la fiabilité et l'efficacité du fonctionnement, la sécurité routière, réduire l'usure et prévenir les pannes.
Si des dysfonctionnements sont détectés lors de la maintenance, ils doivent être immédiatement éliminés en effectuant des travaux de réparation.
Les réparations courantes sont effectuées au besoin, à la fois après avoir détecté des dysfonctionnements lors de l'exécution de la maintenance sous licence, et au besoin.
14.1. Maintenance
L'ordre d'entretien des voitures est établi par le "Règlement sur l'entretien et la réparation du matériel roulant de transport routier":
du quotidien Maintenance(OE);
premier entretien (TO-1);
deuxième entretien (TO-2);
entretien saisonnier (SO).
L'entretien quotidien est effectué après le retour de la voiture du travail sur la ligne et comprend le ravitaillement en carburant, l'huile et le liquide de refroidissement, la préparation des travaux à venir.
TO-1 et TO-2 comprennent le contrôle et le diagnostic, la fixation, le réglage, la lubrification et d'autres travaux visant à prévenir et à détecter les dysfonctionnements, à réduire de manière intensive les paramètres de l'état technique du véhicule, à économiser du carburant et d'autres matériaux d'exploitation, à réduire impact négatif voitures à l'environnement.
L'entretien saisonnier est effectué deux fois par an et comprend des travaux de préparation du matériel roulant pour une exploitation en saison froide et en saison chaude.
Les défauts identifiés lors de la maintenance doivent être éliminés immédiatement, y compris le remplacement de toutes les unités, assemblages et pièces défectueux ; cela devrait inclure la main-d'œuvre et les temps d'arrêt.
Les listes détaillées des opérations de maintenance sont données ci-dessous.
14.1.1. Liste des travaux types TO-1
Moteur. Vérifiez l'étanchéité des systèmes de lubrification, d'alimentation et de refroidissement du moteur (y compris le réchauffeur de démarrage), ainsi que la fixation des équipements et des instruments sur le moteur ; état et tension des courroies d'entraînement ; pièces de fixation du conduit d'échappement (tuyau de descente, silencieux, etc.); montage moteur.
Embrayage. Vérifier l'action du ressort de rappel et la course libre de la pédale d'embrayage ; étanchéité du système de débrayage hydraulique; pour les véhicules équipés d'un servomoteur d'embrayage pneumatique, vérifier la fixation du support et parties constitutives cylindre de puissance de l'amplificateur.
Transmission. Vérifiez la fixation de la boîte de vitesses et de ses parties externes ; le fonctionnement du mécanisme de changement de vitesse sur un véhicule à l'arrêt.
Vérifiez la fixation de la boîte de vitesses hydromécanique, la fixation du carter d'huile et l'état des oléoducs ; fixer les extrémités des fils électriques ; réglage correct du mécanisme de commande du tiroir périphérique.
Transmission par cardan. Vérifier le jeu dans les joints articulés et cannelés de la transmission, l'état et la fixation du support intermédiaire et des plaques de support des roulements à aiguilles ; fixation des arbres à cardan à bride.
Essieu arrière. Vérifiez le serrage des connexions de l'essieu arrière (intermédiaire); fixation du carter de boîte de vitesses, des flasques d'arbre de roue et des couvercles de pignon de roue.
Direction et essieu avant. Vérifiez l'étanchéité du système de direction assistée; fixation et éclissage des écrous des goupilles à billes, des bipieds, des leviers des axes rotatifs, état des pivots et des rondelles de blocage des écrous ; jeu des articulations du volant et de la biellette de direction; serrer les écrous des cales de l'arbre d'hélice de la direction; jeu de roulement de roue ; jeu des roulements de roue.
Système de freinage. Vérifiez le compresseur (visuellement - état extérieur, travail à l'oreille et pression générée selon le manomètre standard); état et étanchéité des canalisations et des appareils système de freinage; l'efficacité des freins sur la béquille ; attelle des doigts des tiges des chambres de frein de l'entraînement pneumatique des freins, la course des tiges des chambres de frein, la course libre et utile de la pédale de frein; état de fonctionnement de la soupape de frein de l'entraînement de frein pneumatique ; état et étanchéité du cylindre principal, du surpresseur, des cylindres de roue et de leurs connexions avec les canalisations ; l'état de fonctionnement de l'entraînement et le fonctionnement du frein de stationnement.
Châssis, suspension, roues. Vérifier par inspection l'état du châssis, des composants et pièces de suspension, du remorquage et de la sellette d'attelage ; état et fonctionnement du mécanisme de levage des roues de route (semi-remorque); fixation d'échelles et doigts de ressorts, fixation de roues; étanchéité de la suspension pneumatique; l'état des pneus et la pression d'air. Retirez les corps étrangers coincés dans la bande de roulement et entre les roues jumelées.
Cabine, plate-forme (corps) et plumage. Vérifier l'état et le fonctionnement du mécanisme de verrouillage, du limiteur d'arrêt et du dispositif de sécurité de la cabine basculante ; état et fonctionnement des serrures, charnières et poignées des portes de la cabine ; fixation de la plate-forme au châssis, support de roue de secours ; au niveau de la semi-remorque, vérifier l'état et la fixation de la crémaillère du milieu ; fixation des ailes, repose-pieds, garde-boue. Inspecter les surfaces de la cabine et de la plate-forme ; si nécessaire, nettoyer les points de corrosion et appliquer un revêtement.
Le système d'alimentation électrique des véhicules fonctionnant au gaz liquéfié. Avant d'effectuer l'entretien, le gaz liquéfié de la bouteille doit être purgé, la bouteille dégazée gaz inerte ou azote. Vérifier l'état et la fixation des équipements à gaz et des gazoducs ; fixer les supports de bouteille de gaz aux longerons du châssis ; pression dans les premier et deuxième étages du détendeur, course et étanchéité de la vanne du deuxième étage du détendeur, étanchéité du dispositif de déchargement ; l'état et le fonctionnement de l'air et la soupape d'étranglement mixer; régler le calage de l'allumage lorsque le moteur tourne au gaz ; fonctionnement du capteur de niveau de gaz liquéfié ; l'état des éléments du système d'alimentation en carburant du moteur avec de l'essence et l'étanchéité des conduites de carburant; fixation du carburateur au tuyau de sortie et du tuyau d'admission au mélangeur. Retirer le dispositif économiseur doseur, vérifier son fonctionnement et son étanchéité ; si nécessaire, nettoyer les cavités gaz et eau de l'évaporateur. Retirez et nettoyez l'élément filtrant du filtre principal et la crépine du réducteur de gaz ; lubrifier les parties filetées des tiges des vannes principales de remplissage et consommables ; drainer les sédiments du réducteur de gaz ; retirer et laver le filtre à air du mélangeur ; verser de l'huile fraîche dans le bain; retirez le verre du filtre à sédiments d'essence, rincez et soufflez l'élément filtrant avec de l'air comprimé ; vérifier l'étanchéité de l'ensemble du système de gaz avec de l'azote ou de l'air comprimé ; retirer le pare-flammes du carburateur, rincer les grilles et souffler à l'air comprimé. Vérifiez le fonctionnement du moteur au gaz, puis à l'essence à différentes vitesses de vilebrequin. Réglez le régime moteur minimum en mode mouvement oisif. Vérifier et, si nécessaire, ajuster la teneur en monoxyde de carbone (CO) dans les gaz d'échappement.
Le système d'alimentation électrique des véhicules fonctionnant au gaz comprimé. Avant de placer la voiture sur le poteau (ligne), effectuer des opérations similaires à celles effectuées avant de mettre la voiture sur TO-1. Si nécessaire, retirez le gaz des bouteilles. Vérifier l'état et le réglage du détendeur haute pression ; état et réglage de la boite de vitesse basse pression; état et fixation des bouteilles de gaz aux supports et fixation des supports aux barres longitudinales de la plate-forme ; état de fonctionnement de l'entraînement de commande du carburateur-mélangeur; inspection - état et fixation des équipements à gaz et des gazoducs ; fonctionnement des manomètres haute et basse pression ; l'état et le fonctionnement de l'appareil de chauffage. Nettoyez l'élément filtrant du filtre principal ; lubrifier les filetages des vannes principales, de remplissage et consommables ; vérifier l'étanchéité du système de gaz avec de l'air comprimé ou de l'azote ; fonctionnement des électrovannes-filtres. Vérifier le démarrage et le fonctionnement du moteur au ralenti à différentes vitesses de vilebrequin ; ajuster la vitesse et le contenu minimum du vilebrequin ALORS dans les gaz d'échappement.
Système d'alimentation pour moteurs à carburateur. Vérifiez la fixation et l'étanchéité des réservoirs de carburant, des raccords de canalisation, du carburateur et de la pompe à carburant ; l'action de l'entraînement, l'intégralité de l'ouverture et de la fermeture des volets d'accélérateur et d'air; fonctionnement de la pompe à carburant sans démontage du moteur ; niveau de carburant dans la chambre à flotteur du carburateur ; facilité de démarrage du moteur, entretien ALORS dans les gaz d'échappement. Réglez le régime de ralenti minimum du vilebrequin.
Système d'alimentation diesel. Vérifier la fixation et l'étanchéité réservoir d'essence, connexions de canalisations, pompes à carburant, injecteurs, filtres, accouplements d'entraînement. Après un TO-2, retirez et vérifiez les buses sur un appareil spécial. Vérifier l'état de fonctionnement du mécanisme de contrôle de l'alimentation en carburant ; fonctionnement du système d'arrêt du moteur ; circulation du carburant (si nécessaire, pressuriser le système). Vérifiez la fiabilité du démarrage du moteur et réglez la vitesse minimale du vilebrequin en mode ralenti. Vérifiez le fonctionnement du moteur, de la pompe à carburant haute pression, du régulateur de vitesse du vilebrequin, déterminez la fumée des gaz d'échappement; après un TO-2, vérifier l'angle d'avance de l'injection de carburant.
Batterie d'accumulateurs. Vérifiez l'état de la batterie par la densité de l'électrolyte et la tension des cellules sous charge ; l'état et la fixation des fils électriques reliant la batterie à la terre et au circuit extérieur, le fonctionnement du coupe-batterie, ainsi que sa fixation dans la prise.
Générateur, démarreur, relais-régulateur. Inspectez et, si nécessaire, nettoyez la surface extérieure du générateur, du démarreur et du relais-régulateur de la poussière, de la saleté et de l'huile. Vérifiez la fixation du générateur, du démarreur et du relais-régulateur ; montage de la poulie du générateur. Avant de vérifier le fonctionnement du moteur à essence, il est nécessaire de fermer les vannes d'alimentation, les gaz d'échappement du système d'alimentation (avant l'arrêt du moteur) et de fermer la vanne principale.
Équipement électrique. Nettoyez la batterie de la poussière, de la saleté et des traces d'électrolyte ; nettoyer les trous de ventilation, vérifier la fixation et la fiabilité du contact des cosses de fil avec les broches de sortie ; vérifier le niveau d'électrolyte. Vérifier l'action signal sonore, lampes de tableau de bord, éclairage et signalisation, instrumentation, phares, veilleuses, feux arrière, feu stop et interrupteur d'éclairage ; générateur et démarreur et l'état de leurs connexions de contact.
Pendant la saison froide, vérifiez le fonctionnement de l'équipement électrique du système de chauffage et du réchauffeur de démarrage. Vérifier la fixation du disjoncteur-distributeur ; essuyez les contacts du disjoncteur avec un chiffon en lin.
Équipement de compteur de vitesse. Vérifiez la fiabilité de la fixation de l'arbre flexible au compteur de vitesse à entraînement mécanique et à la boîte de vitesses, ainsi que l'intégrité de la coque de l'arbre flexible (il ne doit y avoir aucun espace dans la fixation des pointes de la coque de l'arbre flexible) . Vérifier l'état et la fixation du variateur de vitesse électrique et du capteur. Les fils d'entraînement du compteur de vitesse et du capteur ne doivent pas être endommagés et doivent être sécurisés. Vérifier la bonne étanchéité du compteur de vitesse et de son entraînement conformément aux instructions en vigueur.
Lubrifier les unités de friction et vérifier le niveau d'huile dans les carters des unités et les réservoirs des entraînements hydrauliques conformément à la carte chimiotologique ; vérifiez le niveau de liquide dans l'entraînement hydraulique des freins et le désengagement de l'embrayage, le liquide dans les réservoirs des lave-glaces et des lave-phares, et pendant la saison froide également dans l'antigel (dans l'entraînement des freins). Nettoyez les reniflards de la transmission et de l'essieu. Lavez les filtres à air du servofrein à dépression hydraulique (vide). Vidanger le condensat des cylindres pneumatiques de l'actionneur de frein pneumatique. Nettoyez les écrans d'admission d'air sur le boîtier du convertisseur de couple de la poussière et de la saleté. Pour les véhicules avec moteur diesel vidanger les sédiments du réservoir de carburant et des boîtiers de filtre finement et nettoyage grossier carburant, vérifiez le niveau d'huile dans la pompe à carburant haute pression et le contrôle du régime moteur. Lorsque vous travaillez dans des conditions poussiéreuses, changez l'huile dans le carter du moteur, vidangez les sédiments des boîtiers de filtre à huile et nettoyez la surface intérieure du couvercle du boîtier de filtre à huile centrifuge des dépôts ; laver le bac et l'élément filtrant des filtres à air moteur et ventilation de son carter, le filtre grossier (si sa poignée ne tourne pas).
Vérifiez visuellement l'état du faux-châssis, des barres du faux-châssis et des joints pivotants du dispositif de levage de la plate-forme, de la sellette d'attelage et du dispositif de remorquage. Vérifiez l'état et l'étanchéité des connexions des conduites d'huile, des flexibles, le fonctionnement du dispositif de levage de la plate-forme, l'état de la butée de sécurité de la plate-forme. Vérifier l'état du hayon et le fonctionnement de son dispositif de verrouillage. Vérifier visuellement l'état et la fixation de la prise de force, des couvercles des essieux de la plate-forme basculante, des connexions de la tige et du vérin du dispositif de levage de la plate-forme. Vérifiez le niveau d'huile dans le réservoir du mécanisme de levage de la plate-forme ; si nécessaire, faites l'appoint ou remplacez-le (selon le calendrier).
Inspection vérifier l'état du cadre, du plancher, du rembourrage du siège, des serrures des fenêtres et des trappes de la main courante, des supports. Vérifiez l'état, la fixation et le fonctionnement des feux de position, des lampes d'éclairage de l'indicateur de route et du numéro de route. Vérifier l'état des portes et leurs mécanismes d'ouverture par inspection ; vérifier le fonctionnement des vitres électriques, des serrures, des portes, du capot, du couvercle du coffre ; vérifier l'état du tableau de bord, du revêtement de carrosserie (pour les voitures particulières); vérifier le fonctionnement de l'alarme depuis l'habitacle jusqu'au conducteur. Vérifiez la suspension pneumatique et le fonctionnement des régulateurs de position du corps. Vérifiez par inspection l'état des fermes, des longerons de la base de la caisse. Vérifier l'état et la fixation des composteurs (dans les bus).
14.1.2. Liste des travaux types TO-2
Effectuez la liste complète des opérations TO-1 et en plus le travail suivant.
Moteur, y compris les systèmes de refroidissement, la lubrification. Vérifiez l'étanchéité du système de refroidissement du moteur, du système de chauffage et du réchauffeur de démarrage ; état et fonctionnement des stores (stores), radiateur, thermostat, robinets de vidange; vérifier la fixation du radiateur, son revêtement, ses stores, sa hotte; vérifier la fixation du ventilateur, de la pompe à eau et du carter de distribution (chaîne, courroie); état et tension des courroies d'entraînement ; étanchéité du système de lubrification ; fixation des culasses de moteur et des crémaillères d'axes de culbuteurs; espaces entre les tiges de soupape et les culbuteurs ; fixation des canalisations du silencieux; fixation du carter moteur, régulateur de vitesse du vilebrequin; état et montage des supports moteur.
Embrayage. Vérifier la fixation du carter d'embrayage ; l'action du ressort rétractable, la course libre et complète de la pédale, le fonctionnement de l'embrayage et de l'amplificateur d'entraînement.
Transmission. Vérifier visuellement l'état et le serrage de la boîte de vitesses ; l'action du mécanisme de changement de vitesse ; si nécessaire, réparez la boîte de vitesses et ses composants ; vérifier l'état, le fonctionnement et la fixation de l'entraînement de changement de vitesse.
Boîte de vitesses hydromécanique. Vérifier la fixation des chapeaux de palier et du boîtier du convertisseur de couple sur le carter de la boîte de vitesses ; réglage correct des modes de changement de vitesse automatique; pression d'huile dans le système ; état de fonctionnement du capteur de température d'huile ; état et fixation du capteur tachymétrique.
Transmission par cardan. Vérifier le jeu dans les charnières et les joints cannelés de la transmission, l'état et la fixation du support intermédiaire et des plaques de support des roulements à aiguilles ; fixation des arbres à cardan à bride.
Essieu arrière. Vérifier visuellement le serrage des connexions et l'état du carter essieu arrière; état et fixation de la boîte de vitesses de l'essieu arrière et des engrenages des roues ; serrer l'écrou de la bride d'entraînement de l'engrenage principal (avec l'arbre à cardan retiré); fixer les brides des arbres d'essieux.
Direction, essieu avant. Vérifier l'état et le montage correct de la poutre d'essieu avant ; étanchéité du système de direction assistée; ajuster si nécessaire.
Dispositifs d'allumage. Vérifiez l'état et, si nécessaire, nettoyez la surface de la bobine d'allumage, les fils basse et haute tension de la poussière, de la saleté et de l'huile ; dévisser les bougies et vérifier leur état ; vérifier l'état et, si nécessaire, retirer le disjoncteur-distributeur du moteur ; nettoyer la surface extérieure de la poussière, de la saleté et de l'huile ; nettoyer la surface intérieure du distributeur, vérifier l'état des contacts du disjoncteur et, si nécessaire, ajuster l'angle de l'état fermé des contacts ; lubrifiez l'arbre, l'arbre du levier, le feutre et la bague de came. Installez le disjoncteur-distributeur sur le moteur. S'il y a un système d'allumage à transistor de contact, sans retirer l'interrupteur du moteur, nettoyez la surface extérieure de la poussière, de la saleté et de l'huile, essuyez la surface intérieure du chapeau du distributeur, essuyez les contacts, lubrifiez l'arbre, le feutre, l'axe du levier et douille de came.
Dispositifs d'éclairage et de signalisation. Vérifier la fixation et le fonctionnement des feux de position, des feux arrière et du feu stop, des clignotants, des lampes du tableau de bord et du signal sonore ; installation, fixation et fonctionnement des phares, régler la direction du flux lumineux des phares. Nettoyez la surface et les bornes de l'interrupteur à pédale d'éclairage et de l'interrupteur de feu stop de la saleté.
Équipement de compteur de vitesse. Vérifier l'installation correcte de l'arbre flexible d'entraînement du compteur de vitesse, qui doit être fixé avec des supports et ne pas présenter de coudes prononcés, en particulier près de ses extrémités. En faisant tourner le tambour avec des chiffres - indicateurs de kilométrage, vérifiez l'exactitude de la lecture de la vitesse en un point (effectué si un équipement de diagnostic est disponible). La vérification des performances des compteurs de vitesse s'effectue en comparant ses lectures avec les lectures de l'appareil installé sur le support de diagnostic. Vérifier la bonne étanchéité du compteur de vitesse et de son entraînement conformément aux instructions en vigueur.
Travaux de lubrification et de nettoyage. Lubrifiez les unités de friction de la voiture conformément à la carte chimiotologique. Vérifier le niveau d'huile dans la pompe à carburant haute pression et la commande de régime moteur. Vidanger les sédiments des boîtiers de filtre à huile. Nettoyez et rincez la soupape de ventilation du carter. Rincer l'élément filtrant du filtre à air du moteur et du compresseur ; changer leur huile. Changez (selon le programme) l'huile dans le carter, lavez l'élément filtrant du filtre grossier et remplacez l'élément filtrant du filtre nettoyage fin huiler ou nettoyer le filtre centrifuge. Retirez et nettoyez les filtres de la pompe de direction assistée et le filtre du servofrein. Nettoyer les reniflards et ajouter ou remplacer (selon le calendrier) de l'huile dans les carters des unités et les réservoirs de la transmission hydraulique du véhicule conformément à la carte chimiotologique. Retirez et nettoyez le filtre à sédiments de carburant et le filtre fin à carburant. Pour les véhicules équipés d'un moteur diesel, déposer et laver les boîtiers des préfiltres et filtres fins à carburant et remplacer les éléments filtrants. Inspectez et, si nécessaire, nettoyez le puisard de la pompe à carburant de l'eau et de la saleté. Rincer les éléments filtrants du séparateur d'eau. Vidanger le condensat des cylindres de frein à air. Sur les véhicules équipés d'un moteur diesel, vidangez les sédiments du réservoir de carburant.
Vérification de la voiture après le service. Après l'entretien, vérifiez le fonctionnement des unités, composants et appareils de la voiture en déplacement ou sur un support de diagnostic.
Travaux supplémentaires sur camions à benne basculante et tracteurs. Vérifiez le fonctionnement du dispositif de levage de la plate-forme, ainsi que l'état de fonctionnement de sa butée de sécurité ; l'état et la fixation du faux-châssis, de la prise de force et des autres composants et parties de la plate-forme et de son dispositif de levage ; l'état du hayon de la plate-forme et le fonctionnement de son dispositif de verrouillage ; l'état des canalisations, des tuyaux et l'étanchéité des connexions du système hydraulique du dispositif de levage de la plate-forme. Vidanger les sédiments du corps de l'élévateur hydraulique, laver l'élément filtrant du réservoir d'huile, vérifier le niveau d'huile dans celui-ci ; faire l'appoint ou changer (selon le programme) l'huile si nécessaire. Pour les véhicules tracteurs, vérifier l'état et la fixation des pièces de la sellette d'attelage ou du dispositif de remorquage ; lubrifier ces appareils.
Travaux spécifiques sur les bus et les voitures. Vérifier l'état et la fixation des pièces de la base de la carrosserie, des cadres, des parois latérales, du revêtement intérieur, des cloisons, des portes, des marches, des marches, du sol, des cadres de fenêtres, des sièges, des trappes de ventilation du plafond et des mains courantes ; état des revêtements spéciaux anti-corrosion et de la peinture de carrosserie. Si nécessaire, nettoyez les points de corrosion et appliquez un revêtement protecteur. Vérifiez l'état du siège du conducteur et du mécanisme de réglage de sa position, la porte de la trappe de l'indicateur d'itinéraire, le capot ou la porte compartiment moteur; état et fonctionnement des dispositifs d'éclairage intérieur, ainsi que des systèmes de ventilation et de chauffage ; état et fonctionnement des mécanismes d'ouverture des portes ; si nécessaire, retirez-les pour vérifier l'état des pièces. Vérifier la fixation des composants et des pièces de la suspension pneumatique et du stabilisateur stabilité au roulis; état et fonctionnement des serrures et des charnières du capot et des couvercles de coffre ; effectuer (selon le calendrier) la désinfection de l'intérieur et le lavage eau chaude avec une composition détergente des murs, plafonds, mains courantes, fenêtres, portes, coussins et dossiers de sièges.
14.1.3. Entretien saisonnier
En tant que type de maintenance planifiée séparément, la SA est recommandée pour le matériel roulant exploité dans des zones de climats très froids, froids, chauds secs et très chauds secs. Pour voie du milieu Le CO, en règle générale, est combiné avec le TO-2 avec une augmentation correspondante de l'intensité de la main-d'œuvre. Les normes d'intensité de travail pour le CO (à partir de l'intensité de travail de TO-2) sont : 50 % pour les régions climatiques sèches très froides et très chaudes ; 30 % pour les zones froides et chaudes ; 20% pour les autres domaines.
Liste des oeuvres. Rincer le système de refroidissement du moteur. Vérifiez l'état et le fonctionnement des vannes du système de refroidissement et des dispositifs de vidange des systèmes d'alimentation et de freinage. Retirez la batterie pour la recharger et ajustez la densité de l'électrolyte. Rincer le réservoir de carburant et purger les conduites de carburant (en automne). Rincez les radiateurs de chauffage de cabine (carrosserie) et le chauffage de démarrage. Déposer le carburateur et la pompe à carburant, rincer et vérifier l'état et le fonctionnement au stand (en automne); rincer la pompe à carburant haute pression, vérifier l'état et, si nécessaire, régler au stand; nettoyez le générateur et le démarreur, soufflez la cavité interne; si nécessaire, démonter, remplacer les pièces usées et lubrifier les roulements. Regraisser l'arbre flexible de l'entraînement mécanique du tachymètre et les pignons droits du tachymètre électrique. Vérifier l'étanchéité du compteur de vitesse et de son entraînement. Vérifiez l'état de fonctionnement du capteur d'activation de l'embrayage du ventilateur du système de refroidissement et des capteurs d'alarme pour la température du liquide dans le système de refroidissement et la pression d'huile dans le système de lubrification. Vérifier l'étanchéité et l'intégralité de l'ouverture des volets des radiateurs. Effectuer une vidange saisonnière selon la carte chimiothologique. Vérifiez l'état des joints des portes et des fenêtres, installez des couvertures isolantes.
Travaux spécifiques sur les véhicules roulant au gaz liquéfié. Avant d'effectuer le CO, vidanger le gaz des bouteilles, dégazer les bouteilles avec un gaz inerte. Vérifiez la pression de réglage de la soupape de sécurité de la bouteille de gaz. Soufflez les canalisations avec de l'air comprimé. Vérifier le fonctionnement du limiteur de vitesse maximum du vilebrequin. Effectuer un contrôle du manomètre avec enregistrement des résultats dans le journal des contrôles. Soufflez les conduites de carburant avec de l'air comprimé. Une fois par an, lors de la préparation des véhicules pour le fonctionnement : retirez le réducteur de gaz, le mélangeur de gaz, l'évaporateur, la vanne principale et le filtre à gaz principal du véhicule ; démonter, laver, assembler et régler sur le support ; si nécessaire, dépanner et vérifier l'étanchéité ; retirer les couvercles des robinets de consommable, de remplissage et de remplissage maximum, vérifier l'état des pièces ; ajustez la soupape de sécurité sur le support et scellez-la ; vérifier le manomètre, sceller et apposer un tampon avec la date du prochain contrôle. Une fois tous les 2 ans : inspecter la bouteille de gaz avec les raccords ; effectuer des essais hydrauliques et pneumatiques. Peignez le cylindre et appliquez une marque avec la date de la prochaine enquête.
14.2. Maintenance
14.2.1. Les réparations courantes sont effectuées selon les besoins pour assurer le fonctionnement des véhicules avec la restauration ou le remplacement des unités individuelles, des assemblages et des pièces (à l'exception des éléments de base) qui ont atteint l'état maximal autorisé.
14.2.2. Le plus souvent, les réparations courantes sont combinées avec l'entretien. La réparation en cours de la voiture devrait assurer son kilométrage jusqu'au TO-2.
14.2.3. Pour réduire les temps d'arrêt des véhicules dans la réparation en cours, celle-ci est effectuée en remplaçant les unités individuelles, les assemblages et les pièces. Pour la mise en œuvre des réparations courantes, les frais de main d'œuvre sont prévus au rythme de tous les 1000 km de parcours.
14.2.4. Les travaux d'entretien réglementés (typiques) ne sont fournis que pour les bus et les taxis, qui sont soumis à des exigences accrues en matière de sécurité routière. La liste de ces travaux est élaborée directement dans l'entreprise.
14.3. Révision
14.3.1. Pendant la durée de vie utile de la voiture, en règle générale, une révision est attribuée.
14.3.2. La révision est effectuée s'il est nécessaire de remplacer (réparer) le châssis (carrosserie) de la voiture, le moteur et deux ou trois autres unités, en règle générale, pas plus d'une fois pendant la durée de vie de la voiture.
14.4. Normes de fréquence, de durée et de complexité des réparations
Les taux kilométriques du matériel roulant et de ses principales unités avant révision (en milliers de km) sont donnés dans le tableau. 14.1.
La fréquence, la durée et la complexité de l'entretien et des réparations sont indiquées dans le tableau. 14.2.
Tableau 14.1



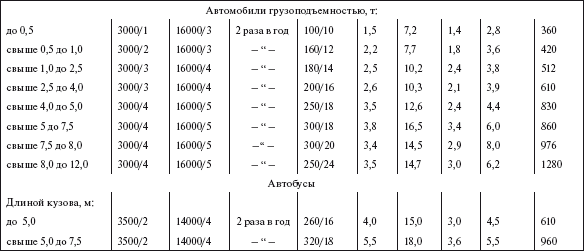
"La fréquence de révision est donnée en milliers de kilomètres.

15. ENGINS DE CONSTRUCTION ROUTIÈRE
Les machines de construction routière basées sur des tracteurs à chenilles et à roues pneumatiques sont incluses dans les groupes d'amortissement suivants:
le cinquième groupe d'amortissement avec une durée d'utilité de plus de 7 ans à 10 ans inclus : tracteurs, bulldozers, grues à flèche, pelles mono-godet, scrapers, niveleuses, rouleaux automoteurs, semi-remorques ;
le quatrième groupe d'amortissement avec une durée d'utilité supérieure à 5 ans jusqu'à 7 ans inclus : groupes compresseurs, charrues à socs ;
le troisième groupe d'amortissement avec une durée d'utilité supérieure à 3 ans à 5 ans inclus : chargeuses, perceuses, convoyeurs.
Les véhicules basés sur un châssis de véhicule sont amortis sur leur durée d'utilité et les directives données à la section 14 pour les marques de véhicules respectives.
15.1. Maintenance
Pour les transports terrestres spéciaux à base de voitures, la procédure d'entretien et la liste des opérations techniques à effectuer sont les mêmes que pour le modèle de base. Les opérations supplémentaires pour les équipements spéciaux installés sur le véhicule doivent être ajoutées à la liste des travaux d'entretien.
La liste et le contenu des opérations technologiques pour les tracteurs, les machines à base de tracteurs et les moteurs de type tracteur sont donnés ci-dessous. De plus, des opérations technologiques de maintenance d'équipements spéciaux sont effectuées en même temps.
15.1.1. Liste des travaux types TO-1
Nettoyer la machine de la poussière, de la terre ou de la neige ; la lessive.
Vérifier l'état et, si nécessaire, régler : la tension de la courroie d'entraînement du ventilateur ; pompe à eau, générateur de système d'éclairage, générateur de système hydraulique de ventilateur, système hydraulique de compresseur ; pression d'ouverture de la soupape de sécurité du système pneumatique ; pression des pneus.
Vidange des sédiments du réservoir de carburant du moteur principal, du filtre à carburant profond et du filtre à carburant fin.
Nettoyage de la batterie ; nettoyage des cosses et cosses oxydées ; lubrification des pièces sans contact avec de la vaseline ; nettoyer les trous d'aération dans les embouteillages ; vérifier le niveau d'électrolyte et, si nécessaire, ajouter de l'eau distillée aux bancs de batteries et serrer ses fixations.
Nettoyage de l'admission d'air, du séparateur de poussière sèche et des cassettes de filtre à air amovibles ; vidanger l'huile de son carter ou nettoyer et laver les cassettes et le réflecteur d'un filtre à air sec.
Nettoyage et lavage : filtre centrifuge du système de lubrification du moteur et trous de ventilation dans les bouchons du réservoir de carburant du moteur principal et du réservoir de carburant du moteur de démarrage ; éléments filtrants du filtre à huile grossier.
Vérification du niveau d'huile et, si nécessaire, ajout dans les carters : pompe à carburant ; régulateur; boîte de vitesses du moteur de démarrage ; boîtes de vitesses; essieu arrière et avant.
Lubrification par graisseurs de roulements : pompe à eau moteur ; serrer l'embrayage ; galets de chenille de la chenille et charnières des leviers et tringles de commande du distributeur hydraulique ; l'arbre de sortie de la boîte de rotation et les galets de la fourchette de débrayage ; ventilateur du système hydraulique ; goupilles sphériques de bielles de direction; axes des pédales de frein, le support supérieur de l'arbre de direction, les axes de la pédale d'embrayage.
Vérifier le niveau de liquide de frein dans le maître-cylindre de frein, faire l'appoint si nécessaire.
Vérification de l'état des goupilles fendues des chenilles; si nécessaire, remplacer les goupilles fendues usées.
15.1.2. Liste des travaux types TO-2
Exécution des opérations TO-1 et, en plus, les travaux suivants.
Vérifier l'état et, si nécessaire, régler : les écarts entre les soupapes et les culbuteurs du mécanisme de distribution du moteur ; la pression d'injection des injecteurs et la qualité de l'atomisation du carburant ; pression d'ouverture des soupapes de sécurité du système hydraulique distance d'arrêt rotation du corps de travail; embrayages pour freins d'orientation et de marche; tension des chenilles.
Vérification de l'état et, si nécessaire, nettoyage de la surface des porte-balais, des balais et du collecteur de l'alternateur, des contacts de l'interrupteur, des balais et du collecteur du démarreur.
Vérification de la densité de l'électrolyte et du degré de charge de la batterie. Si nécessaire, remplacez la batterie.
Changement d'huile dans les carters : moteur et pompe à carburant ; motoréducteur; boîte de vitesses d'entraînement de la pompe.
Vérification du niveau et, si nécessaire, ajout d'huile dans les carters : train arrière et boîte de vitesses ; pilotage; boîte de vitesses du moteur de démarrage.
Nettoyage et lavage de la grille du tuyau de remplissage d'huile et du reniflard de carter ; bouchons de réservoir de carburant et filtres; élément filtrant du filtre du système hydraulique ; reniflard de réservoir hydraulique ; filtres à carburant grossiers; purificateur d'air; bouchon de vidange magnétique du carter moteur.
Vidange de l'huile accumulée dans le carter d'embrayage. Élimination des dépôts de carbone des fentes du pare-étincelles.
Lubrification par graisseurs : roulements d'embrayage ; roulements de roue avant; axes de bras de direction ; roulement à rouleaux de tension d'entraînement de ventilateur ; palier de ventilateur ; tourillons de fixation du pont avant ; bagues des rouleaux de frein des roues avant et arrière, doigts des craquelins des articulations de la biellette de direction; bagues du cylindre de rotation de roue ; douilles du pivot du levier angulaire et de la goupille du dispositif de remorquage.
Remplacement du fluide de travail dans le système hydraulique.
15.1.3. Liste des travaux types TO-3
Exécution des opérations TO-2 et, en plus, des travaux suivants.
Vérifier et, si nécessaire, régler : les écarts entre les électrodes de la bougie d'allumage du moteur de démarrage et dans les contacts du disjoncteur ; magnéto moteur de démarrage ; embrayages de démarrage du moteur; jeu dans les roulements des roues de guidage; pompe à carburant (au stand), moment où le carburant est fourni par la pompe moteur, leviers de commande du système hydraulique; mécanisme d'arrêt du moteur de démarrage ; convergence des roues avant, direction.
Démontage du générateur et du démarreur ; nettoyage et lubrification des pièces; réglage et banc d'essai.
Vérification du fonctionnement du relais-régulateur sur le support, si nécessaire - réglage du relais.
Vérification de l'exactitude des lectures des appareils de contrôle conformément à la norme.
Nettoyage et lavage : garnitures de friction des embrayages ; garnitures de friction pour freins de déplacement; garnitures de friction pour freins d'orientation; filtre à carburant du moteur de démarrage; réservoir de carburant du moteur principal ; systèmes de refroidissement du moteur ; réservoir de carburant du moteur de démarrage ; réservoir du système hydraulique ; ballons à air; boîtiers de filtre pour le nettoyage grossier et fin du carburant ; filtre du goulot de remplissage du réservoir hydraulique ; raccord d'admission de carburant du carburateur du moteur de démarrage.
Changement d'huile dans les carters : réducteur et régulateur de démarrage du moteur ; pilotage; boîtes de vitesses et essieu arrière ; essieux avant et arrière ; boîte de vitesses de voyage.
Remplacement du fluide de travail dans le système hydraulique.
Lubrification par graisseurs : charnières ; décharge et cylindre du bulldozer; stabilisateurs ; essieu avant, demi-axes à roulement à billes ; roulements; roulement à billes; roues motrices et tendeuses; entrée, arbre de sortie du réducteur de rotation.
Vérifier l'installation des phares.
Vérification de l'état du générateur du système hydraulique. Remplacement des éléments filtrants des filtres fins à carburant.
Enlèvement et lavage du carter d'huile, grille du récepteur d'huile de la pompe à huile du moteur principal ; contrôle de la qualité du serrage des goupilles fendues des paliers de vilebrequin et de bielle.
Lubrification de la chaîne à rouleaux.
15.1.4. Entretien saisonnier
Effectuer les opérations de maintenance agréée la plus proche et, en plus, les travaux suivants.
Rincer le système de refroidissement du moteur, le remplir de liquide dont la qualité correspond à la saison de fonctionnement à venir.
Remplacement de l'huile par un grade correspondant à la saison de fonctionnement à venir dans les carters de : moteur principal ; pompe à carburant; régulateur de moteur principal ; contrôleur de moteur de démarrage ; boîtes de vitesses et essieu arrière ; boîtes de vitesses de l'essieu avant; boîte de vitesses du moteur de démarrage ; pilotage.
Lubrification des roulements et des joints pivotants à l'aide de raccords de graissage avec un lubrifiant approprié pour la saison d'exploitation à venir.
Vérification du fonctionnement du thermostat des volets (rideaux) du système de refroidissement du moteur.
Réglage de la vis de réglage saisonnier du relais-régulateur sur la position correspondant à la prochaine saison de fonctionnement.
Ajustement de la densité d'électrolyte à batterie jusqu'à la norme correspondant à la saison d'exploitation à venir.
Ravitaillement des réservoirs de carburant avec une qualité de carburant correspondant à la saison d'exploitation à venir.
Remplacement des éléments filtrants remplaçables du filtre fin à carburant s'il a atteint plus de la moitié de sa durée de vie.
Allumer (pour la période de fonctionnement printemps-été) ou éteindre (pour la période de fonctionnement automne-hiver) le refroidisseur d'huile moteur et le radiateur du système hydraulique.
Allumer (pour la période de fonctionnement automne-hiver) ou éteindre (pour la période de fonctionnement printemps-été) le chauffage individuel du moteur et le chauffage de la cabine.
Pose (pour la période de fonctionnement automne-hiver) ou dépose (pour la période de fonctionnement printemps-été) de capots isolants pour le moteur et la batterie.
15.2. Maintenance
15.2.1. Pendant les réparations en cours, les opérations TO-3 et les travaux suivants sont effectués.
15.2.2. Démontage d'unités et d'assemblages nécessitant des réparations mineures.
15.2.3. Remplacement des pièces défectueuses.
15.2.4. Remplacement des unités et assemblages inutilisables.
15.2.5. Réglage de tous les composants de la machine.
15.3. Révision
15.3.1. Effectuer tous les travaux d'entretien.
15.3.2. Remplacer tous les composants et ensembles dont il existe un doute sur leurs performances jusqu'à la prochaine réparation en cours.
15.3.3. Effectuer le réglage de tous les composants et assemblages de la machine et les tests nécessaires.
15.3.4. Faire un tour de machine.
15.3.5. Réaliser des travaux de peinture.
15.4. Normes de fréquence, de durée et de complexité des réparations
Les normes de fréquence, de durée et de complexité de la réparation des engins de construction de routes sont indiquées dans le tableau. 15.1.
Tableau 15.1
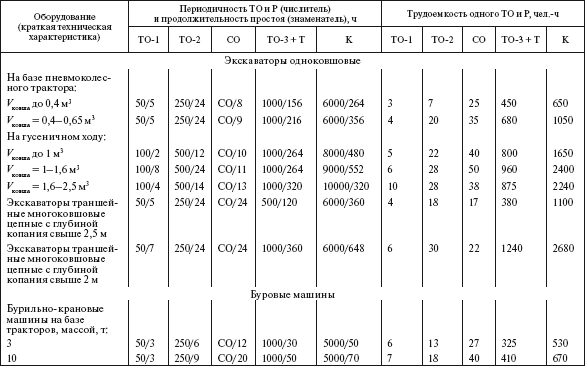





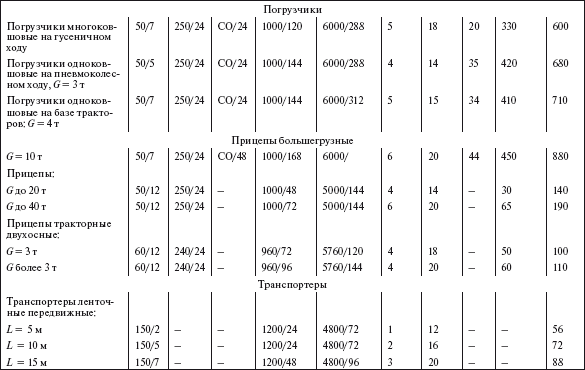

Il existe deux principaux types de travaux de réparation - la réparation actuelle de la machine et la révision de la machine. Les réparations courantes (également appelées maintenance) sont effectuées directement sur le site de la machine, dans le PTO ou dans le RMM de l'entreprise. Pour effectuer des réparations majeures, il est nécessaire de confier la machine à une entreprise de réparation spécialisée.
La réparation actuelle implique l'élimination des défauts mineurs et le remplacement des pièces usées du mécanisme. Dans le cas d'une révision majeure, l'équipement est complètement démonté en composants, puis en pièces. Toutes les pièces sont inspectées et triées selon le principe de "conformité" - en appropriées, inutilisables et sujettes à restauration. Après le remplacement et la réparation des pièces individuelles, la machine est assemblée et soumise à des tests visant à identifier les défauts.
En règle générale, les réparations en cours ne peuvent pas être planifiées à l'avance. La réparation peut être effectuée par méthode globale et individuelle. La méthode globale implique la réparation des pièces et assemblages défectueux avec remplacement par de nouvelles pièces du fonds d'échange ou par des pièces de rechange préréparées. La méthode individuelle implique la réparation des composants défectueux sans remplacer les pièces. Les composants et les pièces retirés lors de la réparation globale sont envoyés à des entreprises de réparation spéciales et les pièces réparées sont renvoyées au fonds d'échange.
Quel est l'avantage de la méthode de réparation du courant global ? En règle générale, cette technique vous permet de réduire le temps consacré aux réparations et minimise ainsi les temps d'arrêt de la machine, augmentant ainsi la production. Dans le même temps, le besoin de réparations majeures est minimisé et la capacité de débit du RMM est augmentée.
Avant de commencer des réparations de tout niveau de complexité, il est nécessaire de nettoyer la pièce et la machine. Les nœuds contaminés sont traités avec des grattoirs en bois et inspectés. L'équipement est démonté et les pièces extraites sont défectueuses pour détecter les ruptures, les plis et les fissures. Le démontage de la machine commence par la séparation des carters et le retrait des barrières de protection, des capots et des écrans de sécurité. Les pièces retirées sont placées dans des conteneurs spéciaux et les pièces appropriées ne sont pas démontées afin de ne pas nuire à leurs performances.
Une mesure de sécurité importante qui protège l'équipement contre des dommages supplémentaires: lors du démontage de la machine, tous les pignons, bagues, engrenages, poulies et roulements sont retirés à l'aide de dispositifs spéciaux - extracteurs, poinçons et presses hydrauliques. Lorsque vous utilisez un extracteur, vous ne devez pas permettre des coups inutiles sur les leviers pour allonger les boutons. L'extracteur doit être installé sans distorsion et les pattes doivent capturer qualitativement et complètement les parties nécessaires des pièces.
Si l'ensemble contient des pièces rouillées, il doit être conservé dans du carburant diesel ou du kérosène, puis seulement démonté. Le démontage des nœuds avec une connexion filetée ne permet pas l'utilisation d'une clé avec une rallonge ou, de plus, un simple ciseau. Mais les goupilles fendues, en règle générale, sont coupées avec un ciseau ou retirées avec une goupille fendue spéciale.
Les engrenages des boîtes de vitesses sont soumis à une inspection externe et mis à jour en fonction de l'usure des dents, ainsi que des rainures de clavette et de cannelure.
La réparation, que toute machine doit subir avec une certaine fréquence, peut être courante ou capitale. Ces types de réparations diffèrent les uns des autres par les objectifs poursuivis, la liste des opérations effectuées, l'intensité de la main-d'œuvre, la durée et le coût. Considérez plus en détail les types actuels et principaux de réparation des machines-outils.
Maintenance est effectué afin d'éliminer les dysfonctionnements des composants individuels et des pièces de la machine ou de les restaurer lorsqu'ils sont usés. Dans la grande majorité des cas, les réparations courantes, autrement dites opérationnelles, sont effectuées sur le site d'installation de la machine, ainsi que dans les ateliers de réparation mécanique ou les services de production et techniques de l'entreprise. Cette réparation, en règle générale, n'est pas spécifiquement planifiée en termes de temps, ce qui s'explique par l'impossibilité de prédire avec précision le moment de la défaillance de l'une ou l'autre unité de la machine. L'étendue des travaux effectués lors de la réparation en cours n'est pas figée : seuls les coûts de main-d'œuvre moyens sont prévus, calculés en heures-homme par rapport à 100 heures machine.
La réparation courante des machines-outils peut être effectuée individuellement ou de manière agrégée. Dans le premier cas, les composants et pièces défaillants sont retirés de la machine, restaurés, puis réinstallés. Dans le second cas, les composants et pièces endommagés sont remplacés par de nouveaux composants qui étaient auparavant stockés dans un fonds d'échange spécial.
Les pièces endommagées sont envoyées à un atelier de réparation mécanique, où elles sont restaurées et transférées au fonds d'échange. Un avantage important de la méthode de réparation globale est une réduction significative des temps d'arrêt de l'équipement et, par conséquent, une augmentation de la production de produits. Dans le même temps, les zones de production du PMM peuvent être réduites, car le débit des ateliers augmente.
Révision les machines-outils, en règle générale, sont effectuées dans une organisation de réparation spécialisée (cependant, elles peuvent être effectuées sans retirer la machine - sur le lieu de son fonctionnement). Lors de la révision, l'équipement est démonté en composants et pièces séparés, qui sont défectueux en trois groupes - appropriés, nécessitant une réparation et non soumis à restauration. Ensuite, l'équipement est assemblé à partir de pièces remplacées (nouvelles) et réparées, testées et rodées. Les bénéfices apportés par la refonte sont très importants :
- toutes les caractéristiques de la machine réparée sont ramenées aux normes de précision des passeports ;
- améliore considérablement la qualité des produits fabriqués sur la machine;
- le degré de sécurité des équipements en fonctionnement augmente;
- la productivité du travail et sa commodité sont augmentées, le temps nécessaire à l'entretien de la machine est réduit, il devient possible d'augmenter sa charge;
- l'entreprise économise de l'argent (par rapport à l'acquisition de nouveaux équipements), réduit les dépenses énergétiques.
La révision de la machine s'effectue en plusieurs étapes, alors qu'il est extrêmement important de suivre leur séquence. Tout d'abord, l'équipement est soigneusement nettoyé des contaminants (des grattoirs en bois spéciaux peuvent être utilisés à cet effet). La machine est inspectée puis démontée. Au stade du démontage, une détection des défauts des pièces est effectuée - la recherche de plis, fissures, éclats, autres bris ou signes d'usure.
Le démontage de la machine, à son tour, est également effectué dans une séquence strictement définie. Tout d'abord, les protections, les boîtiers et les couvercles sont retirés, après quoi les spécialistes effectuant la réparation ont accès aux unités défaillantes et aux pièces de la machine. Il existe des règles selon lesquelles l'équipement est démonté:
- les pièces réparables ne sont pas démontées (non dépersonnalisées) afin de ne pas violer leur intégrité et de faciliter le montage ultérieur ;
- les pièces installées avec un ajustement serré (roulements, engrenages, bagues, poulies, pignons, etc.) sont retirées à l'aide de dispositifs spéciaux - extracteurs, presses hydrauliques, poinçons. Lors de l'installation de ces appareils, les distorsions doivent être exclues et lors de leur utilisation, les coups secs ne doivent pas être autorisés;
- les unités présentant des dommages de corrosion importants (rouillés) sont préalablement conservées dans du carburant diesel ou du kérosène et seulement après cela, elles sont démontées ;
- les boulons et les écrous sont dévissés avec des clés de forme et de taille appropriées, les vis sont dévissées avec des tournevis dont les fentes correspondent strictement aux fentes situées dans les têtes de vis;
- les têtes de rivet lors du démontage des joints rivetés sont coupées avec un ciseau et leurs tiges sont assommées avec une barbe spéciale.
Toutes ces règles doivent être respectées pour atteindre l'objectif le plus important - minimiser le risque d'endommagement des pièces et des assemblages de la machine.
Certaines règles s'appliquent également à la détection des défauts des pièces. Ainsi, l'état des roulements est déterminé par le jeu radial, qui est déterminé dans deux plans diamétralement opposés l'un à l'autre. Les engrenages sont contrôlés par la méthode d'inspection externe, tandis que le degré d'usure des dents, des rainures de clavette et des cannelures est évalué.
Pour vérifier les parties filetées des pièces, ces dernières sont dévissées ou vissées à la main afin de déterminer la difficulté de réalisation de ces opérations. Si les pièces se dévissent ou se revissent difficilement, le filetage est rétabli, et si c'est impossible, la pièce est rejetée.
Réparation de fraiseuse
Réparation en cours de la machine
Pour maintenir les équipements de production en bon état, il est nécessaire non seulement d'effectuer la maintenance, mais également d'effectuer des activités telles que la maintenance et la révision. Les deux types d'événements sont fondamentalement différents l'un de l'autre, tant dans les objectifs poursuivis que dans le degré d'intensité de travail, la liste des travaux effectués et le budget (voir "").
La réparation actuelle de la machine (elle est également opérationnelle) est un ensemble de mesures visant à éliminer les dysfonctionnements et les conséquences de l'usure des composants et mécanismes individuels. Dans la plupart des cas, ces travaux ne nécessitent pas le retrait de l'unité de la production, effectué sur le site d'installation ou dans les ateliers de réparation de l'entreprise. Les réparations opérationnelles ne sont pas planifiées à l'avance, car elles sont associées à des pannes imprévisibles. En conséquence, il est impossible et en connaissance de cause de déterminer l'étendue des travaux et le coût de ceux-ci.
La réparation actuelle de la machine implique deux méthodes d'exécution - individuelle et globale. Avec une option de récupération individuelle, tous les composants défectueux sont retirés de la machine, restaurés et montés en place. La méthode de réparation globale implique l'installation de pièces à partir des réserves du fonds d'échange. Quant aux pièces détachées endommagées, elles sont réparées puis reconstituent les stocks du fonds de change. Cette méthode peut réduire considérablement les temps d'arrêt de l'équipement.
Lors de la révision, une révision complète de la structure est effectuée, ce qui nécessite non seulement des zones spécialement équipées, mais également des qualifications spéciales de spécialistes. L'unité est démontée en ses composants, et après vérification de l'adéquation à l'utilisation, les pièces sont divisées en trois groupes - réparables, récupérables et non réparables. Après avoir remplacé les pièces usées, la machine est assemblée, testée et déboguée.
Contrairement à l'actuel, une révision majeure garantit le bon fonctionnement de toutes les unités pendant au moins une douzaine d'années. Quant aux mesures opérationnelles, par rapport à une unité qui a servi 15-20 ans, elles ne donnent pas confiance dans le "demain", car la forte usure générale des mécanismes se fera constamment sentir par des pannes à un endroit ou une autre.