Système de contrôle électronique du moteur. Le principe de fonctionnement de l'ESUD
Système de gestion électronique du moteur
Le principe de fonctionnement du système de gestion électronique du moteur est que l'unité électronique contrôle (ECU) reçoit des informations continues sur tous les paramètres de fonctionnement des systèmes et mécanismes du moteur, ainsi que sur environnement. Évaluant instantanément l'information, l'ECU émet une commande pour injecter une certaine quantité de carburant et fournir une décharge haute tension aux électrodes de la bougie à un moment strictement défini.
Les changements de température du moteur et de l'air, de la vitesse du vilebrequin et de la pression d'air sont instantanément détectés et transmis à l'ECU, qui modifie la commande "dose de carburant et calage de l'allumage". Peu importe que la température ait changé d'un degré et que le nombre de tours du vilebrequin ait diminué d'un ou deux. L'unité de contrôle "calculera" tout exactement et changera sa commande.
Riz. 28. Schéma du système de contrôle électronique du moteur
Si l'unité électronique n'a pas reçu de données de l'un des capteurs, elle prendra le "méchant morceau de fer sur un crayon", notera le dysfonctionnement et "se faufilera" vers le propriétaire ou le maître du service automobile. Le système contrôle son travail, diagnostique les défauts, les enregistre. Elle peut même éteindre un circuit qui ne fonctionne pas en utilisant une sauvegarde. Et ce n'est pas de la fiction, mais le mode de fonctionnement prévu du système.
Les principaux dysfonctionnements des systèmes de contrôle électronique du moteur
Tous les dysfonctionnements des systèmes de contrôle électronique du moteur peuvent être divisés en deux types principaux.
Le premier type de faute consiste en l'impossibilité de démarrer le moteur et, par conséquent, un mouvement indépendant, au moins jusqu'au lieu de réparation. Dans ce cas, une dépanneuse est appelée pour livrer la voiture à la station-service.
Le deuxième type de panne dans lequel il est possible de se rendre à l'endroit réparation éventuelle, mais ce mouvement se fera avec le "mauvais" fonctionnement d'urgence d'un système ou d'un nœud séparé. Dans le cas du second type de dysfonctionnement, il est d'abord recommandé de prendre conseil auprès d'un spécialiste par téléphone sur l'opportunité d'un déplacement autonome.
Le fait est que dans certains cas, "rouler" vers le lieu d'une assistance qualifiée peut complètement désactiver le système, suivi de réparations majeures et du remplacement des pièces. Par conséquent, le conducteur d'une voiture moderne doit sérieusement réfléchir avant de décider de conduire en mode d'urgence.
Le moteur ne démarre pas.
La raison peut être une pompe à carburant qui ne fonctionne pas, un fusible grillé, un relais de pompe défectueux, un capteur débit massique air, rupture ou perte de contact dans le circuit électrique de la buse.
Le dépannage consiste à vérifier les circuits électriques de la pompe à carburant, à remplacer le relais de la pompe et le fusible grillé, à nettoyer les connecteurs de l'injecteur de la saleté et à restaurer le circuit électrique.
Le moteur tourne par intermittence, cale, tire mal.
La raison peut être un mauvais contact des connecteurs du capteur, de la pompe à carburant, des injecteurs, de la contamination filtres à carburant, fuite d'air dans le système.
Pour éliminer les dysfonctionnements, il est nécessaire de vérifier les connecteurs des capteurs, la pompe à carburant, les injecteurs, de remplacer les éléments filtrants et d'éliminer les fuites du conduit d'admission.
Fonctionnement des systèmes de gestion électronique du moteur
Lorsque vous conduisez une voiture avec un système de contrôle électronique du moteur, vous devez être attentif aux lectures des instruments, suivez les voyants du tableau de bord. Le système de contrôle informe le conducteur en temps opportun des problèmes émergents dans le fonctionnement de ses composants électroniques. La lampe rouge interdit le fonctionnement de la voiture jusqu'à ce que la cause de son inclusion soit clarifiée et que le dysfonctionnement soit éliminé. La couleur jaune (orange) de la lampe avertit qu'un dysfonctionnement peut se produire, mais il est encore temps de l'empêcher.
Recommandations pour le fonctionnement dans des conditions défavorables conditions climatiques, ainsi que certaines règles pour effectuer des travaux dans le compartiment moteur d'une voiture avec un système de contrôle électronique du moteur, sont les mêmes que celles décrites précédemment (voir "Fonctionnement des systèmes d'injection de carburant").
Un système de gestion du moteur est un système de commande électronique qui fait fonctionner deux ou plusieurs systèmes de moteur. Le système est l'un des principaux composants électroniques de l'équipement électrique du véhicule.
Le générateur du développement des systèmes de gestion moteur dans le monde est la société allemande Bosch. Les progrès technologiques dans le domaine de l'électronique, les normes strictes de sécurité environnementale conduisent à une augmentation constante du nombre de systèmes moteurs sous contrôle.
Le système de gestion du moteur retrace son histoire jusqu'au système combiné d'injection et d'allumage. Un système de gestion de moteur moderne intègre beaucoup plus de systèmes et de dispositifs. En plus des systèmes d'injection et d'allumage traditionnels, le système électronique contrôle : le système d'alimentation en carburant, le système d'admission, le système d'échappement, le système de refroidissement, le système de recirculation des gaz d'échappement, le système de récupération des vapeurs d'essence, le servofrein à dépression.
Le terme "système de gestion du moteur" est couramment utilisé pour désigner un système de gestion du moteur à essence. À moteur diesel un système similaire est appelé système de contrôle diesel.
Le système de gestion du moteur comprend des capteurs d'entrée, une unité de commande électronique et des actionneurs de systèmes de moteur.
Les capteurs d'entrée mesurent des paramètres spécifiques du moteur et les convertissent en signaux électriques. Les informations reçues des capteurs constituent la base du contrôle du moteur. Le nombre et la nomenclature des capteurs sont déterminés par le type et la modification du système de contrôle. Par exemple, les capteurs d'entrée suivants sont utilisés dans le système de gestion du moteur Motronic-MED : pression de carburant dans le circuit basse pression, pression de carburant, vitesse du vilebrequin, effet Hall, position de la pédale d'accélérateur, débitmètre massique d'air (si équipé), cliquetis, température du liquide de refroidissement, température de l'huile, température de l'air d'admission, position du papillon, pression du collecteur d'admission, capteurs d'oxygène, etc. Chacun des capteurs est utilisé au profit d'un ou plusieurs systèmes moteurs.
Les actionneurs font partie de systèmes moteurs spécifiques et assurent leur fonctionnement. dispositifs exécutifs Système de carburant sont une pompe à carburant électrique et une soupape de dérivation. Dans le système d'injection, les éléments contrôlés sont les injecteurs et la vanne de régulation de pression. Le fonctionnement du système d'admission est contrôlé par l'actionneur de papillon et l'actionneur de volet d'admission.
Les bobines d'allumage sont des actionneurs du système d'allumage. Le système de refroidissement d'une voiture moderne comporte également un certain nombre de composants à commande électronique: un thermostat (sur certains modèles de moteur), un relais de pompe à liquide de refroidissement supplémentaire, une unité de commande de ventilateur de radiateur, un relais de refroidissement du moteur après l'arrêt.
Dans le système d'échappement, un chauffage forcé des capteurs d'oxygène et du capteur d'oxyde d'azote est effectué, ce qui est nécessaire pour leur travail efficace. Les actionneurs du système de recyclage des gaz d'échappement sont électrovanne commande de l'alimentation en air secondaire, ainsi que du moteur de la pompe à air secondaire. Le système EVAP est contrôlé par l'électrovanne de purge du canister.
Le principe de fonctionnement du système de contrôle moteur repose sur le contrôle intégré du couple moteur. En d'autres termes, le système de gestion du moteur ajuste la quantité de couple en fonction du mode de fonctionnement spécifique du moteur. Le système distingue les modes de fonctionnement du moteur suivants :
- lancement;
- échauffement;
- ralenti;
- Circulation;
- changement de vitesse;
- freinage;
- fonctionnement du système de climatisation.
La modification de la valeur de couple s'effectue de deux manières - en ajustant le remplissage des cylindres en air et en ajustant le calage de l'allumage.
Les voitures Lada Priora sont équipées d'un système de contrôle électronique du moteur (ECM) avec une unité de commande électronique (ECU) 21126-1411020-10 (-11 ou -12) de type Bosch M 7.9.7 (Bosch M 10 ou January-7 , respectivement). Les moteurs utilisent un système d'injection distribuée séquentielle (avec injection phasée) avec retour d'information. Ce système, associé à un convertisseur de gaz d'échappement et à un système de récupération des vapeurs de carburant, garantit le respect des normes Euro-3 et Euro-4 tout en conservant des qualités dynamiques élevées et une faible consommation de carburant.
Le circuit électrique du système d'injection de carburant est illustré à la figure 1.
Figure 1 Connexions du faisceau du système de commande du moteur (ECM) :
1 - ECU ; 2 - bloc du faisceau ECM au faisceau du tableau de bord ; 3 - bloc de fusibles principal ; 4 – capteur de vitesse ; 5 - capteur de route accidentée ; 6 - chute de pression d'huile d'urgence de la lampe de signalisation du capteur ; 7 - capteur de position la soupape d'étranglement; 8 - capteur de température du liquide de refroidissement ; 9 – le manomètre de l'indice de température du liquide de refroidissement; 10 - capteur de débit d'air massique; 11 - régulateur mouvement oisif; 12 - relais de la pompe à carburant électrique; 13 - fusible du circuit d'alimentation de la pompe à carburant électrique (15 A); 14 - relais d'allumage; 15 - fusible du relais d'allumage (15 A); 16 - Fusible du circuit de puissance du calculateur (7,5 A) ; 17 - capteur de position du vilebrequin; 18 - capteur de concentration d'oxygène de contrôle; 19 - capteur de phase ; 20 - capteur de cliquetis ; 21 - électrovanne pour la purge de l'adsorbeur ; 22 - capteur de concentration d'oxygène de diagnostic; 23 - bobines d'allumage ; 24 - bougies d'allumage; 25 - buses; 26 - bloc du faisceau de câblage des bobines d'allumage au faisceau ECM; 27 - bloc du faisceau ECM au faisceau de câbles des bobines d'allumage; 28 - bloc du faisceau ECM au faisceau d'injecteurs; 29 - bloc du faisceau d'injecteur au faisceau ECM; A - à la borne "plus" la batterie; B1, B2 - points de mise à la terre du faisceau du système d'allumage; C1 - point de masse du faisceau de bobine d'allumage
Avertissements
1. Débranchez le fil de la borne négative de la batterie avant de retirer tout composant de l'ECM.
2. Ne démarrez pas le moteur si les cosses de câble de la batterie sont desserrées.
3. Ne déconnectez jamais la batterie du réseau de bord de la voiture lorsque le moteur tourne.
4. Lors de la charge, déconnectez la batterie du réseau de bord de la voiture.
5. N'exposez pas l'ECU à des températures supérieures à 65 ° C en état de fonctionnement et supérieures à 80 ° C en état de non-fonctionnement (par exemple, dans une chambre de séchage). Si cette température est dépassée, l'ECU doit être retiré du véhicule.
6. Ne déconnectez pas ou ne connectez pas les connecteurs du faisceau de câbles à l'ECU lorsque le contact est mis.
7. Avant d'effectuer une soudure à l'arc électrique sur une voiture, débranchez les fils de la batterie et les connecteurs des fils de l'ordinateur.
8. Effectuez toutes les mesures de tension avec un voltmètre numérique, résistance interne qui n'est pas inférieur à 10 MΩ.
2. Travail, le dispositif du système d'injection de carburant du moteur VAZ 2170 2171 2172 Priora.
La quantité de carburant fournie par les injecteurs est contrôlée par un signal d'impulsion électrique de l'ECU. Il surveille les données sur l'état du moteur, calcule le besoin en carburant et détermine la durée requise d'alimentation en carburant par les injecteurs (durée d'impulsion - cycle de service). Pour augmenter la quantité de carburant fournie, l'ECU augmente la durée d'impulsion et pour réduire l'alimentation en carburant, elle la raccourcit.
L'ECU a la capacité d'évaluer les résultats de ses calculs et de ses commandes, de se souvenir des modes de fonctionnement récents et d'agir en conséquence. "L'auto-apprentissage" ou l'adaptation de l'ECU est un processus continu, mais les paramètres correspondants sont stockés dans la RAM de l'unité électronique et, par conséquent, jusqu'à la première mise hors tension de l'ECU.
Le carburant est fourni par l'un des deux diverses méthodes: synchrone, c'est-à-dire à une certaine position du vilebrequin, ou asynchrone, c'est-à-dire indépendamment ou sans synchronisation avec la rotation du vilebrequin. L'injection synchrone de carburant est la méthode la plus couramment utilisée. L'injection de carburant asynchrone est principalement utilisée en mode de démarrage du moteur. L'ECU active les injecteurs en série. Chacun des gicleurs est activé tous les 720° de rotation du vilebrequin. Cette méthode vous permet de doser plus précisément le carburant dans les cylindres et de réduire le niveau de toxicité des gaz d'échappement.
La quantité de carburant fournie est déterminée par l'état du moteur, c'est-à-dire son mode de fonctionnement. Ces modes sont fournis par l'ECU et sont décrits ci-dessous.
Lorsque le vilebrequin du moteur commence à défiler avec le démarreur, la première impulsion du capteur de position du vilebrequin provoque une impulsion de l'ECU pour allumer tous les injecteurs à la fois, ce qui permet d'accélérer le démarrage du moteur.
L'injection initiale de carburant se produit à chaque démarrage du moteur. La durée de l'impulsion d'injection dépend de la température. Sur un moteur froid, l'impulsion d'injection est plus longue pour augmenter la quantité de carburant ; sur un moteur chaud, la durée de l'impulsion est réduite. Après l'injection initiale, l'ECU passe au mode de commande d'injecteur approprié.
Mode de démarrage.
Lorsque le contact est mis, l'ECU active le relais de la pompe à carburant électrique, ce qui crée une pression dans la conduite d'alimentation en carburant vers la rampe d'injection.
L'ECU vérifie le signal du capteur de température du liquide de refroidissement et détermine la quantité de carburant et d'air nécessaire au démarrage.
Lorsque le vilebrequin du moteur commence à démarrer, l'ECU génère une impulsion phasée pour activer les injecteurs, dont la durée dépend des signaux du capteur de température du liquide de refroidissement. Sur un moteur froid, la durée d'impulsion est plus longue (pour augmenter la quantité de carburant fournie), et sur un moteur chaud, elle est plus courte.
Mode enrichissement à l'accélération.
L'ECU surveille les changements brusques de position du papillon (signal du capteur de position du papillon) ainsi que le signal du capteur de débit d'air massique et fournit du carburant supplémentaire en augmentant la durée de l'impulsion d'injection. Le mode riche en accélération n'est utilisé que pour le contrôle transitoire du carburant (mouvement de l'accélérateur).
Mode coupure de carburant pendant le freinage moteur.
Lors du freinage avec le moteur en prise et l'embrayage engagé, l'ECU peut complètement couper les impulsions d'injection de carburant pendant de courtes périodes. L'arrêt et l'ouverture de l'alimentation en carburant dans ce mode se produisent lorsque certaines conditions sont créées pour la température du liquide de refroidissement, la vitesse du vilebrequin, la vitesse du véhicule et l'angle d'ouverture du papillon.
Compensation de la tension d'alimentation.
Lorsque la tension d'alimentation chute, le système d'allumage peut donner une faible étincelle et le mouvement mécanique de «l'ouverture» de la buse peut prendre plus de temps. Le calculateur compense cela en augmentant le temps de stockage d'énergie dans les bobines d'allumage et la durée de l'impulsion d'injection.
Ainsi, lorsque la tension de la batterie (ou la tension du réseau de bord du véhicule) augmente, le calculateur réduit le temps d'accumulation d'énergie dans les bobines d'allumage et la durée d'injection.
Mode coupure de carburant.
Lorsque le moteur est arrêté (contact coupé), le pistolet ne fournit pas de carburant, empêchant ainsi l'allumage spontané du mélange dans un moteur en surchauffe. De plus, aucune impulsion n'est envoyée pour ouvrir les injecteurs si l'ECU ne reçoit pas d'impulsions "de référence" du capteur de position du vilebrequin, c'est-à-dire cela signifie que le moteur ne tourne pas.
L'alimentation en carburant est également coupée lorsque le régime moteur maximal autorisé de 6200 min-1 est dépassé pour empêcher le moteur de fonctionner à des régimes trop élevés.
L'unité de commande électronique (ECU ou contrôleur) est située sous le tableau de bord et constitue le centre de commande du système de gestion électronique du moteur. Il traite en continu les informations provenant de divers capteurs et gère les systèmes qui affectent les émissions de gaz d'échappement et les performances du véhicule.
L'ECU reçoit les informations suivantes :
- position et fréquence de rotation du vilebrequin ;
– position des arbres à cames ;
- consommation massique d'air par le moteur ;
– température du liquide de refroidissement ;
– température de l'air d'admission ;
– la position du papillon des gaz ;
– teneur en oxygène des gaz d'échappement ;
– présence d'une détonation dans le moteur ;
– amplitude des oscillations de la caisse de la voiture ;
- Vitesse du véhicule;
- tension dans le réseau de bord de la voiture ;
– une demande d'allumage du climatiseur (sur les voitures en version variante).
Sur la base des informations reçues, l'ECU contrôle les systèmes et appareils suivants :
- alimentation en carburant (injecteurs et pompe à carburant électrique) ;
- système de mise à feu;
– régulateur de ralenti ;
– un adsorbeur de système de captage des vapeurs d'essence ;
– le ventilateur du système de refroidissement du moteur ;
– embrayage du compresseur de climatisation (sur les véhicules en version variante) ;
- système de diagnostic.
L'ECU active les circuits de sortie (injecteurs, divers relais, etc.) en les court-circuitant à la masse via ses transistors de sortie. La seule exception est le circuit de relais de la pompe à carburant électrique, qui est alimenté par un relais de puissance. À son tour, l'enroulement du relais est contrôlé par l'ECU en fermant l'une des sorties à la masse.
L'ECU est équipé d'un système de diagnostic intégré. Il peut reconnaître les dysfonctionnements de l'ECM en alertant le conducteur par le voyant d'avertissement CHECK ENGINE. De plus, l'ECU stocke les codes de diagnostic qui indiquent le dysfonctionnement d'un élément particulier du système et la nature de ce dysfonctionnement afin d'aider les spécialistes à diagnostiquer et à réparer.
L'ECU contient les types de mémoire suivants :
– mémoire morte programmable (PROM);
– mémoire vive (RAM);
– mémoire électriquement reprogrammable (EPROM).
Mémoire morte programmable (PROM).
Il contient un programme général qui contient une séquence de commandes de fonctionnement (algorithmes de contrôle) et diverses informations d'étalonnage. Ces informations sont les données d'injection, d'allumage, de contrôle du ralenti, etc., qui dépendent du poids du véhicule, du type et de la puissance du moteur, du rapport de transmission et d'autres facteurs. La PROM est également appelée mémoire d'étalonnage. Le contenu de la PROM ne peut pas être modifié après la programmation. Cette mémoire n'a pas besoin d'alimentation pour sauvegarder les informations qui y sont enregistrées, qui ne sont pas effacées lorsque l'alimentation est coupée, c'est-à-dire cette mémoire est non volatile.
Mémoire vive (RAM).
C'est le "carnet" de l'ECU. Le microprocesseur du contrôleur l'utilise pour stocker temporairement les paramètres mesurés qu'il utilise pour les calculs et les informations intermédiaires. Le microprocesseur peut y saisir des données ou les lire si nécessaire.
La puce RAM est montée sur le circuit imprimé du contrôleur. Cette mémoire est volatile et nécessite une alimentation sans coupure pour être maintenue. Lorsque l'alimentation électrique est interrompue, les codes d'anomalie de diagnostic et les données calculées contenues dans la RAM sont effacées.
Mémoire électriquement reprogrammable (EPROM).
Il est utilisé pour le stockage temporaire des codes de mot de passe du système antivol de la voiture (antidémarrage). Les codes de mot de passe reçus par l'ECU de l'unité de commande de l'antidémarrage sont comparés aux codes stockés dans l'EEPROM, à la suite de quoi le démarrage du moteur est autorisé ou interdit.
L'EEPROM enregistre les paramètres de fonctionnement du véhicule tels que le kilométrage total du véhicule, la consommation totale de carburant et le temps de fonctionnement du moteur.
ERPZU enregistre également certaines violations du moteur et de la voiture :
– temps de fonctionnement du moteur avec surchauffe ;
– durée de fonctionnement du moteur avec du carburant à faible indice d'octane ;
– durée de fonctionnement du moteur avec dépassement de la vitesse maximale autorisée ;
– temps de fonctionnement du moteur avec ratés de mélange air-carburant dont la présence est signalée par le voyant du système de gestion du moteur ;
- Temps de fonctionnement du moteur avec un capteur de cliquetis défectueux ;
– durée de fonctionnement du moteur avec un capteur de concentration d'oxygène défectueux ;
- le temps de déplacement de la voiture avec dépassement de la vitesse maximale autorisée pendant la période de rodage ;
– temps de déplacement du véhicule avec un capteur de vitesse défaillant ;
- le nombre de déconnexions de la batterie lorsque le contact est mis.
L'EEPROM est non volatile, elle peut stocker des informations sans alimenter le contrôleur.
L'ECU est situé sous la console du tableau de bord.
Pour remplacer l'unité de commande électronique, vous aurez besoin d'un tournevis cruciforme.
2. Retirez le revêtement droit du tunnel de sol (voir "Démontage et montage des revêtements du tunnel de sol").
3. Saisissez les deux languettes et tirez le support de fixation le long du plan du connecteur jusqu'à ce qu'il s'arrête. 4. Déconnectez le bloc avec les fils de l'ordinateur.
5. Dévissez (pas complètement) deux écrous de fixation d'un bras d'EBU.
Remarque : C le côté opposé Le support de l'ECU n'est pas fixé avec un écrou.
6. Déplacez le support avec l'ordinateur vers la droite et, en le soulevant légèrement, retirez l'ordinateur de la voiture.
7. Installez l'ordinateur dans l'ordre inverse du retrait.
Avertissement:
Une unité électronique défectueuse ne peut être remplacée que par une nouvelle unité dans laquelle la fonction antivol n'est pas activée. Avec un tel remplacement, l'ECU permettra de démarrer le moteur quel que soit l'antidémarrage. Pour activer la fonction antivol, effectuer la procédure d'apprentissage de l'antidémarrage. Pour activer la fonction antivol du nouveau contrôleur, il est nécessaire d'effectuer la procédure d'apprentissage (voir "Apprentissage des clés de l'antidémarrage") en utilisant les outils de formation et de travail disponibles. clés.
4. Capteurs de température du liquide de refroidissement Lada Priora.
Le capteur de température du liquide de refroidissement est une thermistance (une résistance dont la résistance change avec la température).
Le capteur est vissé dans le boîtier du thermostat et connecté à l'ordinateur. A basse température, la résistance du capteur est élevée, et à haute température- faible (tableau 4.1).
L'ECU calcule la température du liquide de refroidissement à partir de la chute de tension à travers le capteur. Sur un moteur froid, la chute de tension est élevée, et sur un moteur chaud, elle est faible.
Tableau 4.1 Dépendance de la résistance du capteur de température du liquide de refroidissement à la température
La température du liquide de refroidissement affecte la plupart des caractéristiques contrôlées par l'ECU.
Pour remplacer le capteur, vous aurez besoin d'une clé "19".
1. Débranchez un fil de la fiche négative de la batterie de stockage.
2. Vidanger partiellement le liquide de refroidissement du radiateur.
3. Pour plus de commodité, retirez le filtre à air (voir "Retrait et installation du filtre à air").
4. Essorez une pince en plastique... 5. ... Et déconnectez un bloc d'une tresse de fils de la jauge de température d'un liquide de refroidissement.
6. Desserrez le serrage du capteur avec une clé ... 7. ... et dévissez-le du boîtier du thermostat.
8. Refroidir le capteur à température ambiante. Connectez le testeur en mode ohmmètre aux bornes du capteur et mesurez sa résistance. Mesurez la température actuelle de l'air avec un thermomètre et comparez les valeurs obtenues avec le tableau. 10.5. Si la résistance s'écarte de la norme, remplacer le capteur. 9. Pour mesurer la résistance aux bornes du capteur à différentes conditions de température, abaissez le capteur eau chaude et vérifiez l'évolution de sa résistance au fur et à mesure que l'eau refroidit en surveillant la température de l'eau avec un thermomètre. Valeurs de résistance nominale à différentes valeurs les températures sont indiquées dans le tableau. 4.1.
10. Installez le capteur dans l'ordre inverse du retrait.
11. Remplir de liquide de refroidissement.
Un capteur de cliquetis fixé au sommet du bloc-cylindres détecte les vibrations anormales (cliquetis) dans le moteur.
L'élément sensible du capteur est une plaque piézoélectrique. Lorsqu'une détonation se produit, des impulsions de tension sont générées à la sortie du capteur, qui augmentent avec l'augmentation de l'intensité des impacts de détonation. L'ECU, basé sur le signal du capteur, régule le calage de l'allumage pour éliminer les éclairs de détonation du carburant.
Pour remplacer le capteur, vous aurez besoin d'une clé "13".
1. Débranchez un fil de la fiche négative de la batterie de stockage.
2. Appuyez sur le dispositif de retenue métallique du bloc du faisceau de câbles ... 3. ... et déconnectez le bloc du capteur de cliquetis. Pour plus de clarté, le tuyau de ventilation du carter a été retiré.
4. Desserrez le boulon de fixation du capteur de cliquetis avec une clé ... 5. ... et, après avoir dévissé le boulon à la main, retirez-le avec le capteur de cliquetis.
Remarque Faites attention au marquage du capteur afin d'acheter un capteur de cliquetis similaire pour le remplacement.
6. Installez le capteur dans l'ordre inverse, en vissant le boulon de sa fixation et en le serrant avec un couple de 10,4 à 24,2 Nm.
Le capteur de débit d'air massique (DMRV) est situé entre le filtre à air et le manchon d'alimentation en air.
Le signal du capteur est une tension continue dont la valeur dépend de la quantité d'air traversant le capteur.
Un capteur de température d'air est intégré au DMRV dont l'élément sensible est une thermistance installée dans le flux d'air. À basse température, la résistance du capteur est élevée et à haute température, elle est faible (tableau 10.6).
Tableau 4.2 Dépendance de la résistance du capteur de température d'air sur la température de l'air d'admission (erreur tolérée 10 %)
Si le capteur de température de l'air est défectueux, l'ECU mémorise le code d'erreur et allume le voyant de signalisation, et remplace les lectures du capteur défectueux par une valeur de température de l'air fixe de 33 ° C.
Pour remplacer le capteur, vous aurez besoin : d'une clé « 10 », d'un tournevis cruciforme.
1. Débranchez un fil de la fiche négative de la batterie de stockage.
2. En appuyant sur le loquet en plastique par le bas avec un tournevis ou un doigt ... 3. ... Déconnectez le bloc de faisceau de câbles du capteur de débit d'air massique.
4. Desserrez le collier de fixation du manchon d'alimentation en air... 5. ...et déconnectez le manchon du capteur.
6. Retirez les deux vis de montage... 7. ...et retirez le capteur du filtre à air.
8. Retirez le joint en caoutchouc et inspectez soigneusement l'état de ses bords, car des dommages peuvent entraîner des fuites d'air en contournant le filtre à air. Pendant le mouvement, l'air contient de nombreuses petites particules mécaniques qui peuvent endommager le DMRV et, par conséquent, entraîner des interruptions de fonctionnement du moteur.
9. Avant d'installer le capteur, placez d'abord le joint en caoutchouc dessus, puis fixez le capteur au filtre à air.
Le capteur de vitesse du véhicule est installé sur la boîte de vitesses. Lorsque les roues motrices tournent, le capteur de vitesse génère 6 impulsions par 1 m de course du véhicule et l'ECU détermine la vitesse du véhicule par la fréquence des impulsions.
1. Débranchez un fil de la fiche négative de la batterie de stockage.
2. Appuyez sur le loquet ... 3. ... et déconnectez le bloc avec les fils du capteur de vitesse.
4. Dévissez l'écrou de l'épingle à cheveux de la fixation du capteur de vitesse... 5. ... Et sortez le capteur du boîtier de la transmission.
Le capteur de position du papillon (TPS) est monté sur le côté de l'ensemble de papillon et est connecté à l'axe du papillon des gaz. C'est un potentiomètre dont une extrémité est alimentée par un "plus" de la tension d'alimentation (5 V), son autre extrémité est reliée à la "masse". De la troisième sortie du potentiomètre (du curseur), il y a un signal de sortie vers l'ECU. Lorsque le papillon des gaz est tourné (à partir de l'action sur la pédale de commande), la tension en sortie du capteur change. Lorsque le papillon est fermé, il est inférieur à 0,6 V. Lorsque le papillon s'ouvre, la tension à la sortie du capteur augmente et doit être supérieure à 4,4 V lorsque le papillon est complètement ouvert. En surveillant la tension de sortie du capteur, l'ECU corrige l'alimentation en carburant en fonction de l'angle d'ouverture du papillon (c'est-à-dire à la demande du conducteur). Le TPS ne nécessite aucun réglage, car l'unité électronique perçoit le ralenti (c'est-à-dire la fermeture à plein régime) comme un zéro.
En cas de défaillance du capteur d'accélérateur, l'ECU mémorise le code d'erreur du capteur, allume le voyant d'avertissement "CHECK ENGINE" et calcule la valeur attendue de l'angle d'ouverture du papillon des gaz à partir de la vitesse du vilebrequin et du signal MAF.
Pour remplacer le capteur, procédez comme suit.
1. Débranchez un fil de la fiche négative de la batterie de stockage.
2. Essorez une pince... 3. ... Et déconnectez un bloc d'une tresse de fils des conclusions du capteur.
4. Retirez les deux vis de montage... 5. ...et retirez le capteur de position de l'accélérateur de l'ensemble d'accélérateur.
6. Installez le capteur dans l'ordre inverse du retrait. Faites attention à l'état de la bague d'étanchéité en caoutchouc mousse : si elle est endommagée, remplacez-la par une neuve.
Le contrôleur de régime de ralenti (IAC) régule le régime de ralenti du vilebrequin en contrôlant la quantité d'air fournie pour contourner le papillon des gaz fermé. Il se compose d'un moteur pas à pas bipolaire et d'une vanne conique qui lui est connectée. La valve s'étend ou se rétracte en fonction des signaux de l'ECU. Une aiguille de régulateur complètement sortie (correspondant à 0 pas) bloque le flux d'air. Lorsque l'aiguille est rétractée, un débit d'air est fourni qui est proportionnel au nombre de pas que l'aiguille s'éloigne du siège.
Le remplacement de l'IAC est décrit dans la sec. "Moteur" (voir "Remplacement du régulateur de ralenti").
Le capteur de position du vilebrequin est de type inductif, conçu pour mesurer la vitesse et la position du vilebrequin. Le capteur est monté sur le couvercle la pompe à huile en face du disque de réglage sur la poulie d'entraînement du générateur. Le disque moteur est une roue dentée à 58 cavités équidistantes (6°). Avec cette étape, 60 dents sont placées sur le disque, deux dents sont coupées pour créer une impulsion de synchronisation (impulsion "de référence"), nécessaire pour coordonner le fonctionnement du contrôleur avec le PMH des pistons en 1ère et 4ème cylindres.
Lorsque le vilebrequin tourne, les dents modifient le champ magnétique du capteur, induisant des impulsions de tension courant alternatif. L'écart d'installation entre le noyau du capteur et la dent du disque doit être de (1 ± 0,2) mm. L'ECU envoie des impulsions aux injecteurs en fonction des signaux du capteur.
Pour remplacer le capteur, vous aurez besoin d'une clé "10".
1. Débranchez un fil de la fiche négative de la batterie de stockage.
2. Essorez une pince... 3. ... Et déconnectez un bloc avec des fils du calibre de disposition d'un vilebrequin.
4. Dévissez le boulon de fixation... 5. ... Et sortez le capteur du bras de sa fixation.
6. Mesurez la résistance du capteur. La résistance d'un bon capteur doit être de 500 à 700 ohms. Si les lectures du testeur sont beaucoup plus basses, il y a probablement un court-circuit entre spires dans l'enroulement, et si, au contraire, il est élevé ou le testeur affiche l'infini (voir photo), alors les contacts à l'intérieur du capteur sont cassés ou là est une rupture dans l'enroulement de la bobine d'induction. Dans le premier comme dans le second cas, le capteur doit être remplacé.
7. Installez le capteur dans l'ordre inverse du retrait.
Le capteur de concentration d'oxygène de contrôle est utilisé dans le système d'injection de carburant à rétroaction et est installé dans la partie supérieure du collecteur. Pour corriger les calculs de la durée des impulsions d'injection, on utilise une information sur la présence d'oxygène dans les gaz d'échappement, cette information est fournie par le capteur de concentration en oxygène de commande. L'oxygène contenu dans les gaz d'échappement réagit avec la sonde à oxygène en créant une différence de potentiel en sortie de la sonde. Elle varie d'environ 0,1 V (mélange riche en oxygène et pauvre) à 0,9 V (mélange pauvre en oxygène et riche).
Pour un fonctionnement normal, la température du capteur doit être d'au moins 300 °C. Par conséquent, pour un réchauffement rapide après le démarrage du moteur, un élément chauffant est intégré au capteur.
En surveillant la tension de sortie du capteur de concentration en oxygène, le contrôleur détermine quelle commande pour ajuster la composition du mélange de travail doit être appliquée aux injecteurs. Si le mélange est pauvre (faible différence de potentiel en sortie du capteur), alors le contrôleur donne l'ordre d'enrichir le mélange ; si le mélange est riche (différence de potentiel élevée) - pour épuiser le mélange.
Pour remplacer le capteur de concentration d'oxygène de contrôle, vous aurez besoin d'une clé "22".
1. Débranchez un fil de la fiche négative de la batterie de stockage.
2. Essorez la pince... 3. ... Et débranchez du moteur la tresse le bloc de la tresse des fils du manomètre agissant de la concentration de l'oxygène.
4. Débranchez du protecteur calorifuge du mécanisme de direction le support de la tresse des fils du manomètre agissant de la concentration de l'oxygène. 5. Dévissez le capteur du collecteur...
6. ... et retirer du véhicule.
Noter
Pour retirer le capteur, utilisez des clés hexagonales spéciales à usage intensif. Ils peuvent ressembler à des clés à anneau ou se présenter sous la forme d'une tête haut de gamme avec un secteur divisé pour y enfiler un faisceau de câbles.
7. Installez le capteur dans l'ordre inverse du démontage, après avoir préalablement lubrifié la partie filetée du capteur avec de la graisse au graphite.
Le capteur de concentration d'oxygène de diagnostic est installé dans le collecteur derrière le convertisseur, il fonctionne sur le même principe que le capteur de contrôle et est complètement interchangeable avec celui-ci. Le signal généré par le capteur de concentration d'oxygène de diagnostic indique la présence d'oxygène dans les gaz d'échappement après le convertisseur. Si le convertisseur fonctionne correctement, les lectures du capteur de diagnostic différeront considérablement des lectures du capteur de contrôle.
Le remplacement du capteur de concentration d'oxygène de diagnostic s'effectue de la même manière que le remplacement du capteur de contrôle.
Le capteur de phase est installé sur le couvercle arrière de l'entraînement d'arbre à cames. Le principe de son fonctionnement est basé sur l'effet Hall. Sur la poulie d'arbre à cames (entrée), un disque d'entraînement avec une rainure spéciale (rebord) est fixé par soudage par points. Lorsque le disque passe à travers la fente du capteur, une impulsion de tension est envoyée du capteur à l'ECU niveau faible(environ 0 V), et lorsqu'il entre dans la zone "mesure" du capteur de rebord du disque maître, une impulsion de tension "de référence" (environ 5 V) se produit sur l'ordinateur, qui correspond à la position de le piston du 3e cylindre dans la course de compression.
Pour remplacer le capteur de phase, vous aurez besoin d'une clé à douille de 10.
1. Débranchez un fil de la fiche négative de la batterie de stockage.
2. Appuyez sur le loquet ... 3. ... et déconnectez le bloc du faisceau de câbles du capteur de phase.
4. Dévissez les deux boulons de fixation du capteur... 5. ... retirez le capteur (pour plus de clarté, dévisser les boulons avec une clé à fourche sur un moteur retiré et partiellement démonté est illustré).
6. Installez le capteur dans l'ordre inverse du retrait.
Le capteur de chaussée accidentée est installé dans compartiment moteur sur la coupelle droite du garde-boue. Le principe de fonctionnement du capteur est basé sur l'effet piézoélectrique. Lors de la conduite sur une route accidentée, une charge variable affecte la vitesse angulaire du vilebrequin. Les fluctuations de la vitesse du vilebrequin sont similaires aux fluctuations qui se produisent lors des ratés.
Le capteur de chaussée cahoteuse mesure l'amplitude des vibrations de la carrosserie et envoie un signal au contrôleur. Si le seuil de signal est dépassé, le contrôleur désactive la fonction de diagnostic des ratés d'allumage.
Vous aurez besoin d'un tournevis cruciforme pour retirer le capteur de route accidentée.
1. Débranchez un fil de la fiche négative de la batterie de stockage.
2. Serrez la pince à ressort... 3. ...et déconnectez le bloc du faisceau de câblage des fils du capteur.
4. Retirez les deux vis qui fixent le capteur au support... 5. ...et retirez le capteur.
6. Installez le capteur dans l'ordre inverse du retrait.
D.Sosnin
Tout système électronique contrôle automatique(ESAU) comprend de nombreux convertisseurs différents d'influences non électriques en signaux électriques. Ces dispositifs sont généralement appelés capteurs, car ils fournissent les informations d'entrée nécessaires au fonctionnement de l'ESAU. Dans ce cas, un groupe de capteurs répond aux signaux de commande externes et aux perturbations aléatoires, tandis que l'autre reçoit les signaux du système de commande lui-même et les renvoie au système. Le premier groupe contrôle directement le fonctionnement du système et l'adapte aux influences extérieures aléatoires (perturbations). Le second forme des rétroactions, ce qui contribue à l'amélioration des paramètres et des caractéristiques du système, et augmente l'efficacité de son fonctionnement. Cet article décrit les capteurs les plus couramment utilisés dans les systèmes électroniques de contrôle automatique d'un moteur automobile.
1. Remarques préliminaires
Les schémas (structurels) les plus généralisés des capteurs sont illustrés à la fig. 1a, b, c.
Le capteur (D), en tant que convertisseur d'impact non électrique (NV) en un signal électrique (ES), se compose toujours d'au moins deux parties (Fig. 1a) - un élément sensible (SE), qui a la capacité de percevoir l'impact non électrique d'entrée, et convertir (P) le signal non électrique (NS) de l'élément de détection en un signal électrique (ES).
Les capteurs sont des dispositifs actifs, dans lesquels le signal électrique est généré en raison de la conversion d'énergie interne sans l'utilisation d'énergie électrique externe (Fig. 1b), et passifs, dans lesquels le signal électrique est une conséquence de la modulation de l'énergie électrique externe (SE). énergie (Fig. 1c) . Par exemple, une résistance variable à contact glissant classique (potentiomètre) peut agir comme un capteur d'angle passif.
2. Capteurs d'angle
Le modèle du capteur d'angle potentiométrique est illustré à la fig. 1g Dans un tel capteur passif, l'élément sensible (SE) est l'axe de rotation, sur lequel est installé le contact glissant, et la piste résistive P est le convertisseur de la position angulaire de l'axe (qui est un signal non électrique ( NS) en sortie de l'élément sensible) dans la valeur résistive de sortie (Fig. 1e ). Un signal électrique (ES) en sortie du capteur potentiométrique n'apparaîtra qu'après application d'une énergie électrique externe (EE) sous la forme d'une tension constante sur la piste résistive. Alors le potentiel électrique sur le contact glissant par rapport à l'une des sorties de la piste résistive sera le signal électrique de sortie (ES) du capteur.Sur la fig. 1e montre la caractéristique de conversion linéaire d'un capteur potentiométrique. La caractéristique peut être facilement modifiée et rendue non linéaire, étagée, avec différentes pentes dans les sections, ce qui est largement utilisé dans la fabrication de capteurs avec la caractéristique de conversion requise. Ceci est réalisé à la fois en modifiant la largeur de la piste résistive par sections et en répartissant l'épaisseur de la couche résistive sur celle-ci. Parfois, des potentiomètres multipistes à deux curseurs sont utilisés.
Il est à noter que l'erreur de conversion d'un capteur potentiométrique passif dépend à la fois de la précision de fabrication de l'élément sensible du SE et du convertisseur P, et de la stabilité de la tension continue de l'énergie externe du SE. Par conséquent, le cas échéant haute précision, des mesures de conception spéciales sont appliquées et la tension continue du SE est stabilisée.
Les capteurs potentiométriques ESAU-D comprennent : capteur d'angle de papillon - DPD (voir Réparation et entretien, 2000, n ° 2, p. 52, fig. 7); capteur de position angulaire du rotamètre du débitmètre d'air - DRV (voir Repair & Service, 2000, n° 7, p. 46, fig. 2) ; capteur de position de pédale d'accélérateur (APS); capteurs de position de divers dispositifs rotatifs (par exemple, un tambour rotatif dans l'ensemble de papillon des gaz du système "Motronic", - voir Repair & Service, 2000, n ° 7, p. 49, fig. 5).
Les capteurs classiques de niveau de carburant dans le réservoir d'essence et de pression d'huile dans le moteur à combustion interne sont également potentiométriques. Tous les capteurs potentiométriques ont un signal électrique analogique à la sortie et, lorsqu'ils sont utilisés dans le cadre d'un ESAU numérique, nécessitent l'utilisation de convertisseurs analogique-numérique. La forme de signal standard (exemplaire) pour les capteurs potentiométriques de l'angle de rotation (sur l'exemple de DPD) est illustrée à la fig. 2 en *.
3. Capteurs de contact ESAU-D
Sur le voiture moderne en plus assez potentiométrique un grand nombre de capteurs de contact, composés d'une paire de contacts électriques (convertisseur de capteur) et d'un poussoir mécanique (élément sensible). De tels capteurs sont passifs et fonctionnent sur le principe de la coupure ou de la fermeture d'un circuit électrique et ont donc un signal "oui-non" discret à la sortie, qui est facilement converti en signal numérique.Dans les ESAU-D modernes, les capteurs de contact sont principalement utilisés comme capteurs pour les positions de bord du papillon des gaz dans le cadre d'un capteur pour sa position, ou comme dispositifs séparés. Dans certains cas, le capteur de contact est utilisé comme micro-interrupteur pour la pompe à carburant électrique lorsque le moteur ne tourne pas, mais que le contact est mis. Un tel capteur est installé dans le débitmètre d'air (voir Repair & Service, 2000, n° 2, p. 52, fig. 7).
4. Capteurs à effet Hall
À systèmes modernes contrôle automatique du moteur pour déterminer la vitesse et la position du vilebrequin et des arbres à cames, un capteur à effet Hall est utilisé (Fig. 3).L'essence de l'effet Hall est que si une barre conductrice rectangulaire K, à travers laquelle une constante électricité Iv, placé dans un champ magnétique constant transverse B, puis dans la troisième direction cartésienne, une force électromotrice Ex sera induite sur les faces latérales du barreau, qui, d'après son découvreur, est appelée FEM de Hall. La direction de cet EMF, comme dans le trident d'induction classique (ILBLF), est déterminée par la règle de la main gauche. Sur la fig. 3a montre le modèle de l'élément Hall. Si les lignes de champ magnétique du champ B dans l'espace P sont bloquées par un rideau magnétiquement imperméable, la FEM de Hall disparaîtra. Si l'obturateur, souvent appelé atténuateur magnétique, est retiré, la FEM de Hall réapparaîtra. Ainsi, l'élément Hall avec l'atténuateur magnétique forme un capteur dans lequel l'atténuateur est l'élément sensible, et l'élément Hall est le transducteur. Il est clair que le fonctionnement du capteur Hall nécessite une source de courant continu externe, c'est-à-dire que ce capteur, comme ceux décrits ci-dessus, est passif. Pour un fonctionnement stable et la stabilisation du signal de sortie du capteur, l'élément Hall est assemblé sur une microplaque semi-conductrice avec un circuit électronique (Fig. 3 b). Le circuit microélectronique comprend un amplificateur limiteur W, un conformateur de déclenchement de Schmidt T, un émetteur suiveur VT et un stabilisateur de tension d'alimentation St.
Dans un vrai capteur Hall (Fig. 3c), la microcarte 1 et l'aimant permanent 2.3 sont fixes et séparés par un atténuateur rotatif 4, qui se présente sous la forme d'un cylindre creux avec des fenêtres magnétotransparentes 5. Le signal de sortie d'un tel capteur est une séquence d'impulsions rectangulaires d'amplitude et de forme stables (voir Fig. 2h), qui ne dépendent pas de la vitesse de commutation du capteur. Le nombre d'impulsions par unité de temps et leur durée sont déterminés par la fréquence de rotation de l'atténuateur magnétique et le nombre de fenêtres sur celui-ci.
Le nombre de fenêtres sur l'atténuateur correspond exactement au nombre de cylindres ICE.
La durée de chaque impulsion à un taux de répétition spécifique est déterminée par la taille de la fenêtre de l'atténuateur le long du périmètre de sa circonférence. La fenêtre du premier cylindre est plus large que les autres, de sorte que le point de référence peut être fixé.
Ainsi, à l'aide du capteur Hall et du circuit électronique de traitement de son signal de sortie, il est possible de déterminer trois paramètres d'entrée principaux pour le système d'allumage : la vitesse du vilebrequin du moteur, sa position par rapport au point mort haut pour tout cylindre à à tout moment, et la position du point de référence . L'inertie du capteur et la stabilité des paramètres du signal permettent de contrôler le calage de l'allumage à chaque course, c'est-à-dire pour chaque cylindre séparément.
5. Capteurs piézoélectriques
Dans les ESAU-D modernes, en plus des capteurs passifs décrits ci-dessus, les capteurs actifs sont également largement utilisés. Dans les capteurs actifs, une grande variété d'effets physiques sont réalisés, dans lesquels il y a une conversion d'énergie interne d'un effet non électrique externe en une réponse électrique de sortie.Un exemple de ceci est l'effet piézoélectrique. Le dispositif qui met en œuvre cet effet est illustré à la Fig. 4a et est appelé élément piézoélectrique.
L'essence de l'effet piézoélectrique est que lors de l'action mécanique du NV sur la plaque PC du piézocristal, qui est recouverte des deux côtés d'un film conducteur TC et dont une extrémité est fixée rigidement dans le support de fixation du PD, une différence des potentiels électriques apparaissent sur les revêtements conducteurs du TC (un signal électrique de l'ES), dont la valeur et la forme sont proportionnelles au degré de déflexion de la plaque sous l'influence de la force mécanique d'entrée HB. L'élément piézoélectrique peut être de n'importe quelle forme - une barre rectangulaire, une plaque plate, une rondelle ronde, un cylindre tubulaire, qui est déterminée par la conception du support et l'endroit où la force externe est appliquée à l'élément piézoélectrique. L'élément piézoélectrique est capable de répondre à une grande variété de influences mécaniques, allant d'un seul impact à des vibrations ultrasonores à haute fréquence. L'élément piézoélectrique (transducteur) ainsi que le dispositif de construction pour la perception et la transmission de la force mécanique d'entrée (élément de détection) forment un capteur piézoélectrique. Les avantages d'un tel capteur sont sa petite taille, son principe de fonctionnement sans inertie et actif (aucune source d'énergie électrique externe n'est nécessaire).
Sur une voiture, des capteurs piézoélectriques sont utilisés dans des systèmes à ultrasons pour protéger les vitres de porte contre une ouverture non autorisée, dans un système pour empêcher les collisions entre une voiture et un obstacle, mais l'utilisation principale d'un capteur piézoélectrique est en tant que capteurs ESAU-D. Il existe deux capteurs de ce type : un compteur de pression absolue (vide) dans le collecteur d'admission du moteur (un capteur de charge moteur MAP à jauge de contrainte) et un capteur de cliquetis.
Le transducteur piézoélectrique du capteur de cliquetis (DD) se présente sous la forme d'une rondelle, qui est pressée contre la zone polie du bloc-cylindres au moyen d'un boulon d'accouplement et d'une masse inertielle (Fig. 4 b). Le point d'installation du capteur est déterminé expérimentalement au stade du développement de la conception du moteur (dans le bain de liquide, les nœuds d'ondes ultrasonores sur le bloc-cylindres sont déterminés et celui qui est le plus proche de la chambre de combustion est sélectionné). Pour le modèle développé du bloc, l'emplacement d'installation du capteur de cliquetis reste constant. La forme d'onde standard du capteur de cliquetis est illustrée à la fig. 2 e) Dans l'unité électronique, un tel signal est d'abord filtré, puis l'amplitude de la fonction d'enveloppe est comparée au niveau admissible pour le signal de détonation. Si le niveau prédéterminé est dépassé, l'autorégulateur d'allumage corrige le calage de l'allumage en conséquence.
Le capteur à jauge de contrainte (MAP) de pression absolue, contrairement à la détonation, est un transducteur passif. Sous l'influence d'une force externe dans la cellule de charge, sa résistance ohmique interne change. Structurellement, la jauge de contrainte est une microstructure semi-conductrice, l'élément piézoélectrique dans lequel se trouve une fine plaque de silicone (environ 0,2 mm) (Fig. 4c). Sur cette plaque, quatre zones résistives (résistances ohmiques) sont technologiquement formées, qui sont interconnectées dans un circuit en pont. Une tension stabilisée de +5 V est fournie à une diagonale du pont, et la tension prélevée sur l'autre diagonale est une fonction linéaire de la pression absolue (vide) au-dessus de la plaque de silicone. Afin que la cellule de charge ait la caractéristique de conversion requise, une cavité sous vide étanche est créée sous la plaque de silicone (entre la plaque et le substrat en verre). La pression résiduelle dans la cavité ne dépasse pas 0,1 bar, grâce à quoi la plaque de silicone, comme un diaphragme élastique, se plie vers la cavité sous vide - à la normale pression atmosphérique au-dessus de la plaque, ou se plie complètement vers le haut lorsqu'il est raréfié au-dessus de la plaque - le diaphragme. Les dimensions linéaires de l'élément sensible de la cellule de charge ne dépassent pas 2...3 mm. Si la jauge de contrainte est conçue pour fonctionner avec un ESAU-D numérique, son signal analogique est converti sous la forme illustrée à la Fig. 2i. Comme le capteur Hall, la cellule de charge est réalisée sur un substrat commun avec un microcircuit pour la génération de signal. Un tel capteur est généralement installé directement dans l'unité électronique ESAU-D et connecté à la zone des gaz collecteur d'admission avec un mince tuyau d'aspiration. Mais d'autres options d'installation du capteur MAP sont également possibles. Finir d'être
6. Capteurs inductifs
Dans un certain nombre d'ESAU-D, des capteurs magnétoélectriques actifs (inductifs) sont utilisés à la place du capteur Hall comme capteurs de vitesse et de position angulaire du vilebrequin du moteur.Le modèle de capteur inductif est illustré à la fig. 5a.
Comme on peut le voir sur la figure, le principal parties constitutives Un tel capteur est une inductance L à aimant permanent NS (convertisseur) et un disque denté PD dont les dents Z sont en matériau ferromagnétique (élément sensible). La spécificité d'un capteur inductif est la séparation structurelle de ses éléments (disque et transducteur inductif). Ainsi, le capteur ID inductif n'est que la moitié du convertisseur d'une grandeur non électrique (la fréquence circulaire Wd du vilebrequin) en un signal électrique (dans la fréquence F, - suivre Impulsions électriques). L'autre moitié est un disque denté PD.
Le principe de fonctionnement d'un capteur inductif est basé sur la première loi de l'induction électromagnétique et consiste dans le fait qu'une augmentation ou une diminution (changement) du flux magnétique Ф à travers les spires Wd de l'inducteur L provoque l'apparition dans celles-ci (en les spires) d'une force électromotrice (EMF) Ed = WdФ / dt. Selon le modèle ci-dessus (voir Fig. 5a), pour mettre en œuvre le principe décrit dans un capteur inductif réel, sa bobine L est montée sur un barreau magnétique permanent NS. Un pôle de l'aimant (par exemple, nord N) dépasse vers les dents Z du disque ferromagnétique du PD, et l'autre (sud S) vient en butée contre le circuit magnétique cylindrique du MP. Le circuit magnétique MP et l'extrémité saillante (sonde magnétique N) de l'aimant permanent, ainsi que les dents Z du disque ferromagnétique PD, forment l'entrefer de travail du capteur. Lorsque le disque FD (vilebrequin du moteur) tourne, la valeur de l'entrefer de travail change constamment du minimum lorsque la dent est sous la sonde magnétique du capteur (correspond au dessin de la figure), au maximum lorsque la dépression entre les dents tombe sous l'enquête. Une modification de l'entrefer de travail entraîne une modification de sa résistance magnétique, et donc du flux magnétique Ф à travers les spires Wd de la bobine L. Cela conduit à l'apparition d'une FEM alternative, dont le point de changement de signe (point zéro) correspond au milieu du haut (centre) de la dent. Le point zéro peut être facilement fixé avec un simple traitement de l'EMF E dans le circuit électronique. Cela permet de déterminer avec précision la position angulaire de chaque dent du disque (et donc du vilebrequin) par rapport au point de référence. La forme d'onde standard d'un capteur inductif est illustrée à la fig. 2e.
Le capteur inductif est installé de manière à ce que sa sonde magnétique soit à proximité (0,5 ... 1,5 mm) des dents ferromagnétiques du disque, et le disque lui-même est situé soit à l'avant, soit à l'arrière du vilebrequin. Un tel capteur inductif est parfois appelé capteur de régime moteur (DOD), car il permet de déterminer la fréquence Wd de rotation du vilebrequin du moteur à partir de la fréquence F, la répétition des impulsions qu'il génère. De plus, il peut être utilisé pour mesurer l'angle de rotation du vilebrequin entre deux événements caractéristiques en comptant le nombre d'impulsions du capteur entre eux. Dans ce dernier cas, le capteur inductif est appelé capteur d'impulsions angulaires (AIM).
Étant donné que la couronne dentée (démarreur) du volant moteur est en matériau ferromagnétique, elle (engrenage) est souvent utilisée comme disque denté d'un capteur inductif. Dans ce cas, pour déterminer le point de référence, un deuxième capteur inductif (supplémentaire) est installé, qui génère une impulsion par tour de vilebrequin. Excitateur ferromagnétique capteur supplémentaire est une goupille en acier vissée dans le volant par le côté à un certain endroit (Fig. 5 b). Cet endroit correspond au point de position du vilebrequin, à partir duquel il reste autant de degrés angulaires au point mort haut (PMH) du premier piston que celui fourni par le microprocesseur de cet ESAU-D numérique pour calculer le calage de l'allumage (généralement 45 ... 60°). Un tel dispositif est appelé capteur d'origine de référence (LOS) et est utilisé conjointement avec un capteur d'impulsion angulaire (ROI).
Mais les fonctions du capteur d'origine peuvent également être remplies par le capteur d'impulsions angulaires lui-même, si son excitateur est un disque denté avec un espace d'une ou deux dents à l'endroit où la goupille en acier pour le FOND est installée (Fig. 5, c). Un tel capteur est appelé capteur de vilebrequin inductif (DKV). Un exemple de forme oscillographique du signal DKV est représenté sur la fig. 2g.
7. Capteurs de concentration d'oxygène
Sur une voiture moderne, problèmes de neutralisation substances toxiques dans les gaz d'échappement (FOG) sont résolus avec l'utilisation de neutralisants de gaz spéciaux. Ces dispositifs fonctionnent de manière plus fiable en conjonction avec le système d'injection d'essence, qui est équipé d'un capteur de concentration d'oxygène (ou de deux capteurs) dans le conduit d'échappement du moteur (Fig. 6a).
La sonde à oxygène * génère un signal de retour Ud pour le calculateur électronique d'injection (ECU-B) qui (ECU) corrige la composition du mélange TV en fonction du coefficient d'excès d'air a à l'entrée du système. La correction est mise en œuvre en modifiant la durée d'injection d'essence par l'injecteur FV (modification de la durée de l'impulsion de commande St).
Le capteur d'oxygène pour ESAU-D peut être réalisé en trois versions : en tant que source de courant chimique (CPS) avec une force électromotrice contrôlée par la concentration en oxygène ; comme une chimiorésistance**, dont la valeur résistance électrique dépend de la pression partielle d'oxygène dans les gaz d'échappement lavés par le capteur ; comme thermocouple avec thermoEMF en fonction de la concentration en oxygène.
Le capteur d'oxygène en tant que HIT (Fig. 6b) se compose de deux électrodes de platine Pt et d'un électrolyte solide de dioxyde de zirconium ZrO2 entre elles. Le dioxyde de zirconium a une structure poreuse et de minces films de platine (électrodes) déposés des deux côtés (sous vide) sur sa surface, également poreuse avec des trous microscopiques. Selon les flux de gaz, les électrodes sont séparées de manière à ce que l'une d'elles soit dans le milieu extérieur (EAS), et l'autre soit lavée par les gaz d'échappement (FOG).
Ainsi, un système électrochimique est créé [(O "2) Ptj, qui devient actif lorsqu'il est chauffé à une température supérieure à 350 ° C. La nature de l'activité résultante de ce système est associée à la décomposition à haute température des molécules d'oxygène O2 en ions positifs et électrons libres (O2> 2O + + 2f).Une telle réaction a lieu dans les pores de l'électrolyte solide derrière les électrodes poreuses en platine, où en présence d'un catalyseur au platine et à une température supérieure à 350 ° C, de l'oxygène passe à l'état ionisé. Si la concentration en oxygène des deux côtés de l'électrolyte solide en zirconium est la même (O'2 = O "2), alors la différence de potentiels électriques sur les électrodes de platine est nulle (le nombre de porteurs de charge électrique dans les zones opposées est la même). Avec une diminution de la concentration en oxygène dans les gaz d'échappement (O2 "\u003e O" 2) par rapport à l'atmosphère environnante (due à la combustion de O "dans Cylindres ICE), l'équilibre des charges électriques est perturbé, le mouvement des ions oxygène dans l'électrolyte se forme et une force électromotrice (EMF) du capteur apparaît sur les électrodes. La polarité de l'ensemble par rapport à l'électrode externe reliée à la "masse" (au corps) du capteur est positive.
Sur la fig. 6d montre un dessin en coupe d'un capteur de concentration d'oxygène, qui est vissé dans le tuyau 1 du collecteur d'échappement. air atmosphérique(EAC) pénètre dans l'élément actif 4 du capteur par les canaux d'air 6 percés dans le boîtier de montage 8. Les gaz d'échappement (FOG) "lavent" la surface extérieure de l'élément actif 4, vers laquelle ils pénètrent à travers les fentes 16 dans le capot de protection 2. La couche de platine de contact externe 3 de l'élément actif 4 est reliée électriquement au boîtier 8 et en outre par l'intermédiaire de la rondelle d'étanchéité 14 - à la "masse" du moteur. La couche de platine interne 5 (électrode positive) est connectée à la borne 11 du contact de signal de sortie au moyen d'une connexion de contact à pression 7 et d'une broche de connexion 12 avec une rondelle de contact 15. La cavité interne 13 est un isolant en céramique. Le but des autres parties du capteur de concentration d'oxygène (DCC) ressort clairement du dessin.
La caractéristique de conversion du capteur d'oxygène est illustrée à la fig. 6c, et l'exemple de forme de la valeur actuelle du signal DCC est représenté sur la fig. 2a. Avec un coefficient a > 1, la valeur E
La partie résistive du capteur est en oxyde de titane (TiO2), qui est une céramique semi-conductrice cristalline avec une sensibilité de surface élevée à l'oxygène libre à haute température.
La sensibilité des céramiques à l'oxygène est due à la présence de liaisons libres dans le réseau cristallin de l'oxyde de titane, qui peuvent être facilement réduites par les ions oxygène. Les ions oxygène O+, comme dans l'élément zirconium, sont formés dans la couche de surface céramique sous l'influence d'une température élevée (environ 650°C) en présence d'un catalyseur actif. Le rôle de catalyseur est joué par des contacts de platine déposés sous forme de films minces (sous vide) à la surface de la chimiorésistance. Les ions oxygène étant une impureté donneuse «volatile» par rapport au semi-conducteur TiO2, ils quittent facilement le réseau cristallin lorsque la pression partielle d'oxygène externe diminue.Le remplissage ou la libération de liaisons nodales dans le réseau cristallin avec des ions oxygène joue le rôle d'un régulateur de la résistance ohmique du semi-conducteur.
Cependant, la chimiorésistance, en plus d'être sensible aux variations de la concentration en oxygène, a une sensibilité encore plus élevée aux variations de la température de chauffage. Ainsi, lorsque la température double (de 350 à 750°C) et à concentration constante en oxygène autour du capteur en titane, sa résistance ohmique change de cinq ordres de grandeur (de 103 à 108 Ω). Cela conduit à la nécessité d'utiliser à la fois une compensation thermique interne et externe. Lors de la fabrication du capteur, la couche externe d'oxyde de titane est appliquée sur une thermistance semi-conductrice à tige, qui a un coefficient de température de résistance (TCR) de signe opposé par rapport à la chimiorésistance TiO2. De plus, la thermistance est chauffée par un courant électrique externe jusqu'à la température de fonctionnement du capteur, qui peut ainsi être ajustée automatiquement et maintenue relativement constante.
Un capteur d'oxygène en tant que thermocouple avec thermoEMF dépendant de la concentration en oxygène est une modification d'un capteur avec une chimiorésistance. La base en céramique est la même - l'oxyde de titane TiO2. Les contacts de sortie sont en platine. Mais maintenant, ce n'est pas un changement de résistivité du semi-conducteur qui est utilisé, mais son contact thermoélectrique avec le métal du connecteur externe. Un thermocouple "TiO2-Pt" est formé, dont la puissance thermoélectrique à température constante dépend de la concentration de porteurs de charge libres dans le semi-conducteur, et qui, à son tour, dépend de la concentration d'oxygène dans environnement externe. Le thermocouple devient un thermocouple actif sensible à la concentration en oxygène. Un tel capteur est chauffé dans le flux de gaz d'échappement, et son température de fonctionnement réglé automatiquement par le chauffage électrique. Dans le même temps, une électrode de thermocouple (le revêtement métallique externe de la céramique) est soumise à un échauffement plus fort, ce qui contribue à augmenter la sensibilité du capteur.
8. Capteurs de température
Les plus courants à bord de la voiture sont les capteurs de température. Avec leur aide, le chauffage de la température de l'essence, des huiles et d'autres fluides techniques, tels que les liquides de refroidissement et de frein, le réfrigérant dans le climatiseur, ainsi que la température des flux d'air et de gaz, est contrôlé. Dans certains cas, la mesure de la température à la surface des pièces métalliques est utilisée. Les capteurs de température peuvent être actifs (thermocouples et thermoéléments) et passifs - une grande variété de dispositifs thermosensibles, tels que des thermistances à semi-conducteurs, des ferrites à perméabilité magnétique variable, des condensateurs, des plaques bimétalliques, etc. .Pour contrôler et mesurer les paramètres de température d'un moteur de voiture ESAU-D utilise des capteurs : température de l'air d'admission DTV (-40
La spécificité de la thermistance frittée en tant que capteur de température (Fig. 7) est qu'elle remplit simultanément les fonctions d'élément sensible et de transducteur résistif.
La thermistance 3 est placée dans un boîtier de protection conducteur de chaleur 2 avec un filetage de fixation pour installer le capteur au bon endroit et avec des contacts électriques 1. Lorsque le moteur se réchauffe, la résistance ohmique de l'élément sensible d'un tel capteur (avec NTC ) diminue, et par conséquent, la chute de tension aux bornes du DTD diminue également. Dans ce cas, l'exemple de forme du signal du capteur correspond à l'oscillogramme représenté sur la fig. 2b.
En conclusion, il convient de noter qu'un certain nombre de capteurs "exotiques" pour ESAU-D sont également connus (voir, par exemple, ). Mais leur application sur moderne voitures extrêmement limité.
Littérature
1. D. Sosnine. Systèmes d'injection de carburant pour moteurs à essence. Service de réparation. 2000, n° 2, p. 49-55.2. Systèmes électroniques de contrôle et de surveillance pour la construction et voitures de route. Edité par B.I. Petlenko. M :. Intext, 1998.
Le capteur de température du liquide de refroidissement est une thermistance (une résistance dont la résistance change avec la température). Le capteur est vissé dans le boîtier du thermostat et connecté à l'ordinateur. À basse température, la résistance du capteur est élevée et à haute température, elle est faible (tableau 10.5).
L'ECU calcule la température du liquide de refroidissement à partir de la chute de tension à travers le capteur. Sur un moteur froid, la chute de tension est élevée, et sur un moteur chaud, elle est faible.
Tableau 10.5 Dépendance de la résistance du capteur de température du liquide de refroidissement à la température
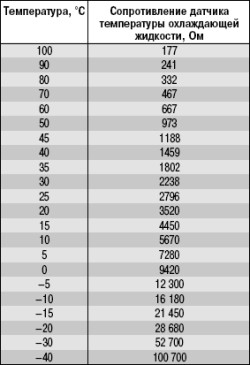
La température du liquide de refroidissement affecte la plupart des caractéristiques contrôlées par l'ECU.
Pour remplacer le capteur, vous aurez besoin d'une clé "19".
2. Vidanger partiellement le liquide de refroidissement du radiateur.
3. Pour plus de commodité, retirez le filtre à air (voir "Retrait et installation du filtre à air").
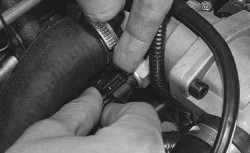
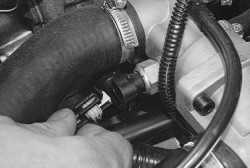
4. Appuyez sur le dispositif de retenue en plastique...
5. ... et débranchez le connecteur du faisceau de câbles du capteur de température du liquide de refroidissement.
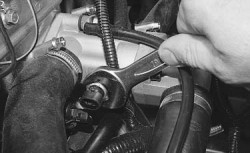
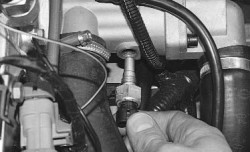
6. Desserrez le serrage du capteur avec une clé ...
7. ... et dévissez-le du boîtier du thermostat.
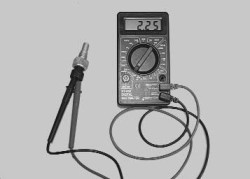
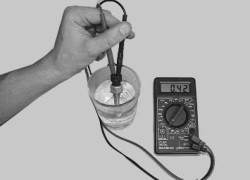
8. Refroidir le capteur à température ambiante. Connectez le testeur en mode ohmmètre aux bornes du capteur et mesurez sa résistance. Mesurez la température actuelle de l'air avec un thermomètre et comparez les valeurs obtenues avec le tableau. 10.5. Si la résistance s'écarte de la norme, remplacer le capteur.
9. Pour mesurer la résistance aux bornes du capteur dans diverses conditions de température, abaissez le capteur dans de l'eau chaude et vérifiez le changement de sa résistance à mesure que l'eau refroidit, en contrôlant la température de l'eau avec un thermomètre. Les valeurs nominales de résistance à différentes températures sont données dans le tableau. 10.5.
10. Installez le capteur dans l'ordre inverse du retrait.
11. Remplir de liquide de refroidissement.
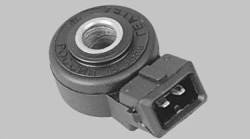
Un capteur de cliquetis fixé au sommet du bloc-cylindres détecte les vibrations anormales (cliquetis) dans le moteur.
L'élément sensible du capteur est une plaque piézoélectrique. Lorsqu'une détonation se produit, des impulsions de tension sont générées à la sortie du capteur, qui augmentent avec l'augmentation de l'intensité des impacts de détonation. L'ECU, basé sur le signal du capteur, régule le calage de l'allumage pour éliminer les éclairs de détonation du carburant.
Pour remplacer le capteur, vous aurez besoin d'une clé "13".
1. Débranchez un fil de la fiche négative de la batterie de stockage.
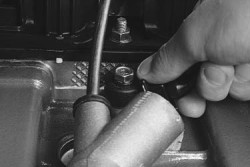
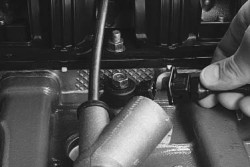
2. Appuyez sur la pince métallique du bloc de faisceau de câbles ...
3. ... et déconnectez le bloc du capteur de cliquetis. Pour plus de clarté, le tuyau de ventilation du carter a été retiré.
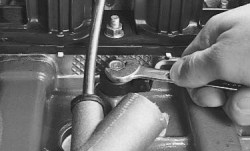
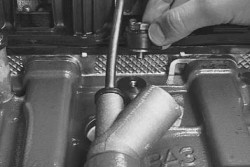
4. Desserrez le boulon de montage du capteur de cliquetis avec une clé ...
5. ... et, après avoir dévissé le boulon à la main, retirez-le avec le capteur de cliquetis.
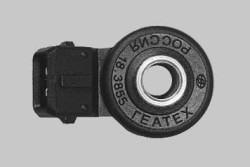
Noter
Faites attention au marquage du capteur afin d'acheter un capteur de cliquetis similaire pour le remplacement.
6. Installez le capteur dans l'ordre inverse, en vissant le boulon de sa fixation et en le serrant avec un couple de 10,4 à 24,2 Nm.
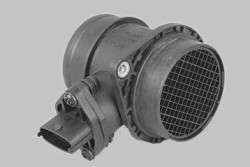
Le capteur de débit d'air massique (DMRV) est situé entre le filtre à air et le manchon d'alimentation en air.
Le signal du capteur est une tension continue dont la valeur dépend de la quantité d'air traversant le capteur.
Un capteur de température d'air est intégré au DMRV dont l'élément sensible est une thermistance installée dans le flux d'air. À basse température, la résistance du capteur est élevée et à haute température, elle est faible (tableau 10.6).
Tableau 10.6 Dépendance de la résistance du capteur de température d'air sur la température de l'air d'admission (erreur tolérée 10 %)
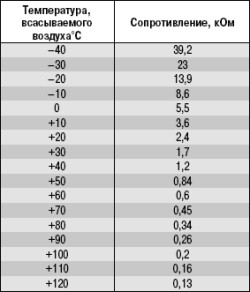
Si le capteur de température de l'air est défectueux, l'ECU mémorise le code d'erreur et allume le voyant de signalisation, et remplace les lectures du capteur défectueux par une valeur de température de l'air fixe de 33 ° C.
Pour remplacer le capteur, vous aurez besoin : d'une clé « 10 », d'un tournevis cruciforme.
1. Débranchez un fil de la fiche négative de la batterie de stockage.
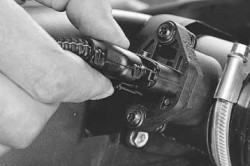
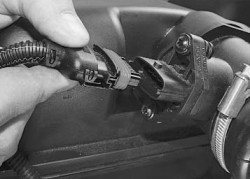
2. En appuyant sur le loquet en plastique par le bas avec un tournevis ou un doigt ...
3. ... Déconnectez le bloc de câblage du capteur de débit d'air massique.
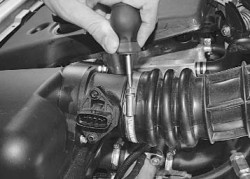
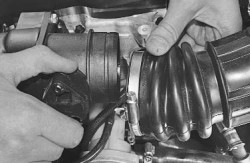
4. Desserrez le collier du tuyau d'air...
5. ... et déconnectez le manchon du capteur.
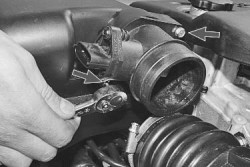
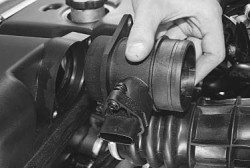
6. Dévissez les deux vis de fixation...
7. ... et retirez le capteur du filtre à air.
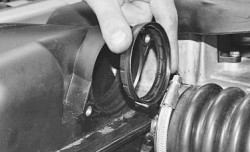
8. Retirez le joint en caoutchouc et inspectez soigneusement l'état de ses bords, car des dommages peuvent entraîner des fuites d'air en contournant le filtre à air. Pendant le mouvement, l'air contient de nombreuses petites particules mécaniques qui peuvent endommager le DMRV et, par conséquent, entraîner des interruptions de fonctionnement du moteur.
9. Avant d'installer le capteur, placez d'abord le joint en caoutchouc dessus, puis fixez le capteur au filtre à air.
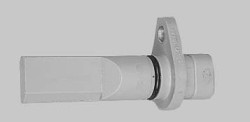
Le capteur de vitesse du véhicule est installé sur la boîte de vitesses. Lorsque les roues motrices tournent, le capteur de vitesse génère 6 impulsions par 1 m de course du véhicule et l'ECU détermine la vitesse du véhicule par la fréquence des impulsions.
1. Débranchez un fil de la fiche négative de la batterie de stockage.
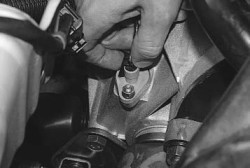
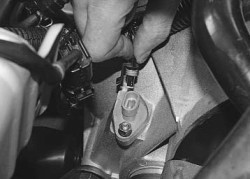
2. Appuyez sur le loquet...
3. ... et déconnectez le bloc avec les fils du capteur de vitesse.
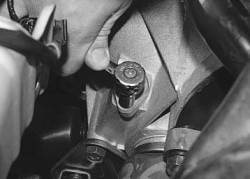
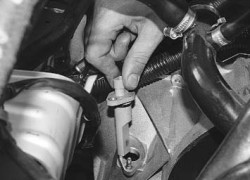
4. Dévissez l'écrou d'une épingle à cheveux de fixation du capteur de vitesse...
5. ... et retirez le capteur du carter de la boîte de vitesses.
6. Installez le capteur dans l'ordre inverse du retrait.
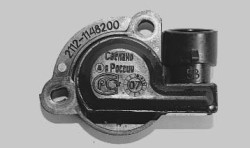
Le capteur de position du papillon (TPS) est monté sur le côté de l'ensemble de papillon et est connecté à l'axe du papillon des gaz. C'est un potentiomètre dont une extrémité est alimentée par un "plus" de la tension d'alimentation (5 V), son autre extrémité est reliée à la "masse". De la troisième sortie du potentiomètre (du curseur), il y a un signal de sortie vers l'ECU. Lorsque le papillon des gaz est tourné (à partir de l'action sur la pédale de commande), la tension en sortie du capteur change. Lorsque le papillon est fermé, il est inférieur à 0,6 V. Lorsque le papillon s'ouvre, la tension à la sortie du capteur augmente et doit être supérieure à 4,4 V lorsque le papillon est complètement ouvert. En surveillant la tension de sortie du capteur, l'ECU corrige l'alimentation en carburant en fonction de l'angle d'ouverture du papillon (c'est-à-dire à la demande du conducteur). Le TPS ne nécessite aucun réglage, car l'unité électronique perçoit le ralenti (c'est-à-dire la fermeture à plein régime) comme un zéro.
En cas de défaillance du capteur d'accélérateur, l'ECU mémorise le code d'erreur du capteur, allume le voyant d'avertissement "CHECK ENGINE" et calcule la valeur attendue de l'angle d'ouverture du papillon des gaz à partir de la vitesse du vilebrequin et du signal MAF.
Pour remplacer le capteur, procédez comme suit.
1. Débranchez un fil de la fiche négative de la batterie de stockage.
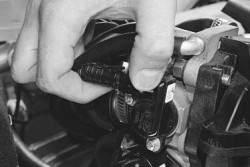

2. Appuyez sur le loquet...
3. ... et débranchez le connecteur du faisceau de câbles des fils du capteur.
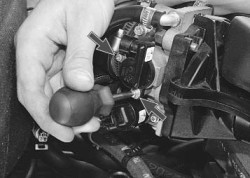
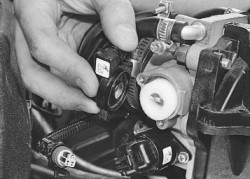
4. Dévissez les deux vis de fixation...
5. ... et retirez le capteur de position du papillon de l'ensemble de papillon.
6. Installez le capteur dans l'ordre inverse du retrait. Faites attention à l'état de la bague d'étanchéité en caoutchouc mousse : si elle est endommagée, remplacez-la par une neuve.
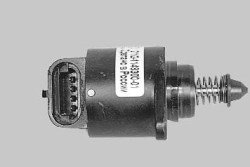
Le contrôleur de régime de ralenti (IAC) régule le régime de ralenti du vilebrequin en contrôlant la quantité d'air fournie pour contourner le papillon des gaz fermé. Il se compose d'un moteur pas à pas bipolaire et d'une vanne conique qui lui est connectée. La valve s'étend ou se rétracte en fonction des signaux de l'ECU. Une aiguille de régulateur complètement sortie (correspondant à 0 pas) bloque le flux d'air. Lorsque l'aiguille est rétractée, un débit d'air est fourni qui est proportionnel au nombre de pas que l'aiguille s'éloigne du siège.
Le remplacement de l'IAC est décrit dans la sec. 5 "Moteur" (voir "Remplacement du régulateur de ralenti", p. 134).
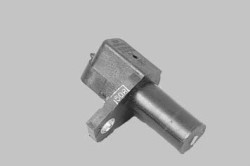
Le capteur de position du vilebrequin est de type inductif, conçu pour mesurer la vitesse et la position du vilebrequin. Le capteur est monté sur le couvercle de la pompe à huile en face du disque de réglage sur la poulie d'entraînement de l'alternateur. Le disque moteur est une roue dentée à 58 cavités équidistantes (6°). Avec cette étape, 60 dents sont placées sur le disque, deux dents sont coupées pour créer une impulsion de synchronisation (impulsion "de référence"), nécessaire pour coordonner le fonctionnement du contrôleur avec le PMH des pistons en 1ère et 4ème cylindres.
Lorsque le vilebrequin tourne, les dents modifient le champ magnétique du capteur, induisant des impulsions de tension alternative. L'écart d'installation entre le noyau du capteur et la dent du disque doit être de (1 ± 0,2) mm. L'ECU envoie des impulsions aux injecteurs en fonction des signaux du capteur.
Pour remplacer le capteur, vous aurez besoin d'une clé "10".
1. Débranchez un fil de la fiche négative de la batterie de stockage.
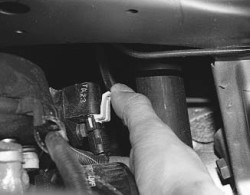
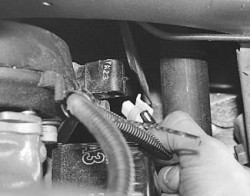
2. Appuyez sur le loquet...
3. ... et déconnectez le bloc avec les fils du capteur de position du vilebrequin.
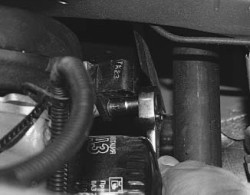
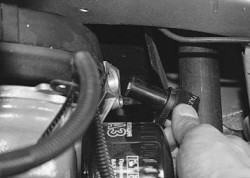
4. Dévisser un boulon de fixation...
5. ... et retirez le capteur de son support de montage.
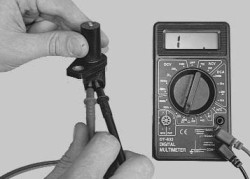
6. Mesurez la résistance du capteur. La résistance d'un bon capteur doit être de 500 à 700 ohms. Si les lectures du testeur sont beaucoup plus basses, il y a probablement un court-circuit entre spires dans l'enroulement, et si, au contraire, il est élevé ou le testeur affiche l'infini (voir photo), alors les contacts à l'intérieur du capteur sont cassés ou là est une rupture dans l'enroulement de la bobine d'induction. Dans le premier comme dans le second cas, le capteur doit être remplacé.
7. Installez le capteur dans l'ordre inverse du retrait.
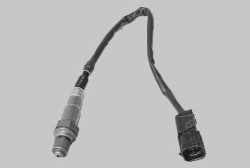
Le capteur de concentration d'oxygène de contrôle est utilisé dans le système d'injection de carburant à rétroaction et est installé dans la partie supérieure du collecteur. Pour corriger les calculs de la durée des impulsions d'injection, on utilise une information sur la présence d'oxygène dans les gaz d'échappement, cette information est fournie par le capteur de concentration en oxygène de commande. L'oxygène contenu dans les gaz d'échappement réagit avec la sonde à oxygène en créant une différence de potentiel en sortie de la sonde. Elle varie d'environ 0,1 V (mélange riche en oxygène et pauvre) à 0,9 V (mélange pauvre en oxygène et riche).
Pour un fonctionnement normal, la température du capteur doit être d'au moins 300 °C. Par conséquent, pour un réchauffement rapide après le démarrage du moteur, un élément chauffant est intégré au capteur.
En surveillant la tension de sortie du capteur de concentration en oxygène, le contrôleur détermine quelle commande pour ajuster la composition du mélange de travail doit être appliquée aux injecteurs. Si le mélange est pauvre (faible différence de potentiel en sortie du capteur), alors le contrôleur donne l'ordre d'enrichir le mélange ; si le mélange est riche (différence de potentiel élevée) - pour épuiser le mélange.
Pour remplacer le capteur de concentration d'oxygène de contrôle, vous aurez besoin d'une clé "22".
1. Débranchez un fil de la fiche négative de la batterie de stockage.
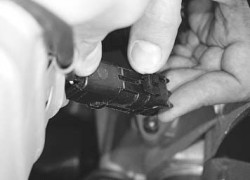
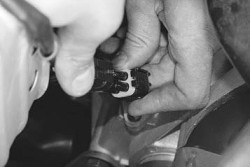
2. Appuyez sur le loquet...
3. ... et déconnectez le bloc du faisceau de câbles du capteur de concentration d'oxygène de contrôle du faisceau du moteur.
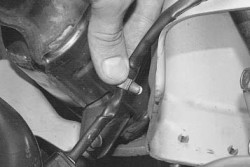