Pourquoi un vilebrequin est-il nécessaire dans un moteur ? Grande encyclopédie du pétrole et du gaz
Le moteur est une unité complexe dans laquelle il n’y a aucune pièce mineure. L'un de ces composants est le vilebrequin. D'une part, il ne s'agit pas d'un dispositif complexe, mais d'une pièce simple ; d'autre part, le vilebrequin est l'une des pièces principales du moteur.
A quoi sert le vilebrequin ?
Toute automobile est un moteur à pistons. Le principe de son fonctionnement est simple : un mélange air-carburant est fourni au cylindre, qui s'enflamme et augmente de volume. Une pression excessive apparaît, ce qui pousse le piston hors du cylindre. En même temps, le piston fait mouvement vers l'avant, qui doit être converti en rotation afin de le transmettre à la boîte de vitesses, puis à l'arbre de roue ou à l'arbre de transmission.
L'endroit où l'arbre repose sur le bloc moteur est l'endroit où se trouvent les roulements principaux, et aux points situés entre la bielle et l'arbre se trouvent les roulements de vilebrequin. Les roulements principaux et les roulements de vilebrequin sont constitués de deux demi-coquilles recouvertes d'un alliage de roulement. Selon le type de cet alliage, les coquilles ont force différente et propriétés et sont donc utilisés dans d'autres types de moteurs. Par exemple, les alliages d'étain sont le plus souvent utilisés dans les applications de faible puissance. moteurs à essence, car ils fonctionnent bien sur les poteaux en acier aux surfaces non durcies, mais ont une mauvaise résistance à la chaleur.
C'est précisément la fonction que remplit le vilebrequin : il convertit un type de mouvement mécanique en un autre, à savoir : translation en rotation.
Le matériau à partir duquel les vilebrequins sont fabriqués n'est pas un simple acier, c'est pourquoi le coût du produit est si élevé par rapport au prix d'une simple ébauche métallique. L'acier à partir duquel la tige est fabriquée est allié avec du chrome, du molybdène et d'autres métaux, ce qui confère au produit une résistance particulière. De plus, le processus de fabrication lui-même est important, depuis la disposition des fibres de la pièce jusqu'à la méthode de fabrication - pressage ou forgeage.
Les alliages de cuivre contiennent grand nombre des bronzes au plomb qui peuvent résister à des charges portantes élevées. Pour cette raison, B moteurs diesel ou des moteurs à essence très chargés. De cette façon, la poussée est suffisamment forte pour empêcher la casserole de tourner ou de bouger. Certains panneaux ont ce qu'on appelle. Serrures qui s'insèrent dans les évidements réalisés dans les douilles. Concernant leur rôle, les propositions sont très partagées. Ceci est considéré soit comme une protection supplémentaire contre la torsion des bagues, soit comme un moyen d'indiquer l'insertion correcte de demi-coquilles à performances déséquilibrées.
Nous avons compris à quoi sert l'arbre, mais la question demeure : où est le vilebrequin ? Le vilebrequin est situé au bas du moteur ; il est recouvert par le bas et rempli d'huile moteur. L'arbre est fixé dans des roulements qui le maintiennent et ne lui permettent pas de bouger ; parfois des butées supplémentaires sont utilisées pour le renforcer. Mais il existe une exception : dans les moteurs boxer, le vilebrequin est situé plus haut, au centre du moteur à combustion interne.
Cotyle tourné - cela pourrait-il être la cause de verrous manquants ?
Des verrouillages supplémentaires dans les panneaux peuvent-ils réellement les empêcher de s'enrouler ? Les moteurs d'aujourd'hui disposent de moins en moins de mécanismes de verrouillage. Cela ne signifie cependant pas que l’absence de ces verrous a entraîné un problème de torsion. Utilisation intensive et haute puissance les moteurs rendent les bagues faciles à saisir et même à tourner. Cela signifie que même le contour des tuyaux à l'ancienne ne peut pas les empêcher de tourner.
Des voitures sans serrures brûlaient. Dans un moteur plus récent, le problème de panoramique est si marginal qu'on peut supposer qu'il ne s'agit pas d'un problème. Alors, comment est-il possible qu'un groupe motopropulseur de 2,0 litres avec plus de puissance et d'effort, malgré les mêmes bagues, n'ait aucun problème avec celles-ci ? Le vin ne repose tout simplement pas directement dans la poêle. Les panneaux ne les protègent pas de la rotation. Cependant, il est impossible de cacher le fait qu’une poêle aussi lisse est beaucoup moins chère à produire. Est-ce aussi bon que cette perceuse avec des serrures supplémentaires ?
Qu'est-ce qu'un vilebrequin et comment ça marche ?
Les pistons du moteur bougent de manière inégale - tandis que les jours tombent, d'autres montent - cela garantit un fonctionnement fluide et une répartition uniforme de la charge dans le temps. Le vilebrequin limite la course des pistons après la combustion du carburant et les ramène à leur position d'origine pour comprimer le mélange. D'une part, il est relié au mécanisme de distribution de gaz, d'autre part, il transmet le couple à la transmission.
De ce fait, une mauvaise lubrification entraîne une destruction plus rapide du palier lisse de la dernière bielle. De plus, une pompe à huile inefficace entraînera également des problèmes avec le turbocompresseur et entraînera une usure plus importante que prévu. Il y a clairement peu de problèmes avec les acétabis, mais ils n’ont pas complètement abandonné.
Bien entendu, la conception elle-même et, surtout, le matériau à partir duquel les bagues sont fabriquées sont extrêmement importants pour leur résistance, mais le manque de lubrification adéquate est la principale raison de leur usure rapide. Pour prolonger la durée de vie des bagues, notamment dans le cas de moteurs turbocompressés fortement chargés, il est souvent nécessaire de remplacer huile moteur. Des limailles métalliques persistantes obstruent les passages d’huile moteur et empêchent la bonne lubrification des composants. Cela est particulièrement vrai avec les moteurs connus pour avoir des problèmes pour dégager les arbres à cames ou les pompes à carburant.
Le vilebrequin est composé de plusieurs tourillons :
- Les principaux sont situés exactement le long de l'axe central de l'arbre et ne se déplacent pas lors de la rotation.
- Entre eux se trouvent des tourillons de bielle, qui sont décalés par rapport à l'axe selon des angles différents et strictement définis et, lorsqu'ils tournent, décrivent un cercle. Ce sont eux qui assurent l’interaction entre l’arbre et le piston.
- Les cols sont reliés les uns aux autres par des « joues » - des plaques en métal épais. Les joues, en plus de celles de fixation, remplissent une fonction anti-résonance - lors de la rotation, l'arbre peut résonner et s'effondrer, mais les joues ne permettent pas que cela se produise.
C'est difficile à décrire avec des mots apparence de cette pièce, si vous souhaitez représenter avec précision le vilebrequin, une photo ou un schéma est la meilleure option.
Plus nous changeons l'huile de ces moteurs souvent, plus le risque de grippage de l'un des buissons sera moindre. À propos du soi-disant. huiles longues et leurs intervalles de remplacement tous les 30 000. km. Je vous conseille d'oublier si nous voulons que le moteur de la voiture fonctionne correctement et parfaitement.
La pompe à huile est un autre élément qui a une grande influence sur l’état des bagues. Essentiellement, c’est comme si le cœur pompait le sang vers tous les organes du corps. Si la pression fournie par l'huile au système est trop faible, même de l'huile moteur fraîchement remplie ne protégera pas les bagues contre les dommages. Pire encore, compte tenu de sa disponibilité incomplète, la capture du moteur n'est pas non plus difficile.
Vilebrequin
Le vilebrequin sert à convertir les forces (transmises par les pistons et les bielles à ses manivelles) en couple perçu par l'arbre du générateur. Les manivelles du vilebrequin sont situées à un angle de 120° l'une par rapport à l'autre, à l'exception des manivelles des troisième et quatrième cylindres. Dans ce cas, les manivelles des troisième et quatrième, deuxième et cinquième et, enfin, des premier et sixième cylindres, respectivement, sont également dirigées (Fig. 22).
Il est important de se rappeler que même le remplacement de la pompe à huile par une neuve ne peut pas protéger la voiture des dommages au moteur. Il arrive que le mécanicien ne vérifie pas que la nouvelle pompe fonctionne à la bonne pression. Si un problème avec le turbocompresseur ou la voiture est présent dans la voiture après l'installation d'une nouvelle pompe, cela peut atteindre 90 %. Bien entendu, la qualité de la poêle elle-même influence également grandement sa longévité. Actuellement, le marché polonais est dominé par 3 à 4 grandes entreprises impliquées dans la production de ce type de composants.
Leur qualité d’avis des utilisateurs est tout à fait comparable. Le problème est que de plus en plus de publicités apparaissent, encourageant l'achat de bagues produites par des entreprises inconnues d'Extrême-Orient. Étant donné que les métaux utilisés pour fabriquer les bagues peuvent clairement différer dans leurs propriétés, cela ne vaut pas la peine de prendre des transactions risquées. De plus, le coût d'un ensemble de bonnes casseroles est d'environ 150 à 200 zlotys. Beaucoup travail plus cher mécanicien qui doit extraire et démonter le moteur puis le remettre quand même.
Pour réduire le poids et améliorer le refroidissement, les tourillons de bielle sont creux. Les cols molaires ne possèdent pas de tels trous. Pour faire passer l'huile lubrifiante dans le vilebrequin des tourillons principaux aux bielles adjacentes, des trous obliques d'un diamètre de 20 mm sont percés à travers les joues les reliant. Des tubes en acier dont les extrémités sont évasées des deux côtés sont fermement placés dans ces trous. Dans le col de la quatrième molaire, il n'y a pas de trou oblique et il n'y a qu'un trou de 60 mm de profondeur, destiné au démoulage de la doublure inférieure.
S'il est nécessaire de le redistribuer en raison de la mauvaise qualité du cotyle, alors cette opération est inutile. De plus, la structure et la fonction des composants tels que : les pistons les bielles les vilebrequins et les pièces associées seront abordés. Système manivelle-piston La fonction d'un moteur à manivelle est de convertir le mouvement alternatif d'un piston en rotation du vilebrequin. Le piston est comprimé par le vilebrequin à l'aide d'une bielle qui, pendant le fonctionnement, est incluse dans le mouvement du moteur. Le mouvement du piston donne à la bielle un mouvement progressif et la manivelle du vilebrequin fait tourner la bielle autour de la tige de piston reliant la tige de piston à la tige de piston. Piston Moteur piston combustion interne est une partie mobile de la chambre de combustion. Le but principal du piston est de vaincre la pression provoquée par le gaz à travers son fond. Le piston transmet ensuite la force ci-dessus ainsi que la charge de sa propre résistance d'inertie à l'axe de piston, ainsi qu'à la bielle et au vilebrequin. Auparavant, les pistons étaient en fonte ou en alliage. Cependant, l'inconvénient de la fonte est sa densité assez élevée et sa conductivité thermique relativement faible. Les matériaux les plus courants pour les pistons sont les alliages d’aluminium avec des alliages de silicium, de magnésium, de cuivre et de nickel. Cela maintient le poids suffisamment faible pour que l'ensemble du carter soit moins sollicité en raison de forces d'inertie plus faibles. La conception du piston doit être suffisamment résistante aux charges mécaniques élevées. De plus, il doit prendre en compte la possibilité de : la dissipation thermique du dessus chaud, chauffé par les gaz à haute température, vers les parois refroidies du cylindre, l'entraînement des pistons du cylindre et la pression latérale imposée par la cinétique du carter, la coopération avec le chemise de cylindre avec d'éventuelles petites pertes par frottement. 3 Un piston de moteur de voiture se compose des pièces principales suivantes : partie inférieure avec sa périphérie, appelée zone de feu, une zone annulaire avec des rainures pour les segments de piston, une chemise qui assure le bon sens du piston dans le cylindre, des moyeux pour les axes de piston. Conception à pistons. Source : propres recherches. Bas du piston. Il s'agit de la partie du piston la plus sollicitée, son contact avec les autres pièces ainsi qu'avec les parois du cylindre doit assurer une bonne évacuation de la chaleur excédentaire. Dans les moteurs particulièrement lourds, le fond des pistons est davantage refroidi en pulvérisant de l'huile à l'intérieur ou en utilisant des passages d'huile supplémentaires qui mettent l'huile sous pression dans la pièce moulée. Le bas du piston est influencé par des facteurs tels que : les caractéristiques du moteur, l'organisation du processus de combustion, l'emplacement des soupapes, des bougies ou des dispositifs d'injection. Zone d'extinction d'incendie Il s'agit de la partie cylindrique des parois latérales fixée directement au fond du piston. Sa tâche principale est de séparer les segments de piston des gaz chauds dans la chambre de combustion et dans l'espace de travail du cylindre. Dans les moteurs modernes, la hauteur de la zone d'incendie est comprise entre 6,5 et 8 % du diamètre du cylindre. Ce n'est que dans les moteurs diesel 4 avec une chambre de combustion complètement encastrée dans le piston que cette hauteur atteint 15 % du diamètre du cylindre. Zone des segments Il s'agit du côté de la paroi du piston qui comporte des rainures circulaires qui maintiennent les segments de piston. Leur travail consiste à sceller le piston dans le cylindre et à éliminer l'excès d'huile de la chemise de cylindre. L'ajustement entre les rainures et les bagues a une influence décisive sur la puissance effective du moteur ainsi que sur la consommation de carburant et d'huile. Les rainures des segments racleurs comportent des trous disposés radialement qui drainent l'excès d'huile dans le piston. Le joint torique est situé dans la rainure la plus proche du bas du piston. Cet anneau scelle la chambre de combustion, empêchant les gaz de combustion de pénétrer dans la chambre depuis le carter moteur. Lorsque le mélange air-carburant s'enflamme, la pression des gaz d'échappement agit sur le piston, le faisant se déplacer vers le vilebrequin. La bague racleur de compression est située entre le joint torique et la bague racleur. Son objectif est d'arrêter les gaz qui ont pénétré dans le joint torique et de gratter l'excès d'huile de la surface du cylindre. L'anneau racleur est l'anneau le plus bas. Le segment d'huile est utilisé pour éliminer l'excès d'huile de la paroi du cylindre lorsque le piston se déplace. L'huile retourne au bloc moteur par les fentes de l'anneau et du piston. Dans les moteurs à deux temps, cet anneau n'est pas nécessaire car l'huile est fournie avec le carburant et sa combustion est intentionnelle. Segments de piston sceller la chambre de combustion, transférer la chaleur du piston au cylindre et contrôler la consommation d'huile. Pour que l'anneau puisse remplir sa fonction, il doit être élastique lorsqu'il est exposé à des températures élevées. A cet effet, l'anneau inséré dans le cylindre doit comporter une fente dans la serrure. La taille de l'espace de verrouillage dépend du diamètre de l'anneau et du matériau dans lequel l'anneau est fabriqué. La bague a exactement une certaine forme pour adhérer avec précision aux parois du cylindre afin d’assurer l’étanchéité requise. La forme d'anneau appropriée est obtenue par le processus d'ovalisation. Un autre facteur important est la force de pression annulaire sur les parois du cylindre. Cette force dépend généralement de l’élasticité du matériau dans lequel l’anneau est fabriqué. La plupart des anneaux sont en fonte grise. La fonte est facile à appliquer sur la paroi du cylindre et peut être facilement appliquée sur d'autres matériaux pour augmenter sa résistance. Anneau de compensation. Anneau de compression Le joint torique est le plus proche de la chambre de combustion et est exposé aux substances les plus corrosives et aux plus hautes températures. température de fonctionnement. Les segments de compresseur transfèrent jusqu'à 70 % de la chaleur du piston au cylindre via le segment de compression. Typiquement, cet anneau a une forme rectangulaire ou sphérique. L'anneau du cylindre possède une surface de roulement incurvée qui permet de lubrifier l'anneau et la paroi du cylindre. La surface incurvée réduit le risque de rupture de la couche d'huile causée par une pression annulaire excessive sur le cylindre. Bague racleur compensatrice. Source : propres recherches. 6 Segment racleur de compression Le segment racleur de compression est un autre segment situé au bas du piston. Son but est de créer une couche d'huile d'épaisseur constante qui permet de lubrifier la bague de compression. Certaines bagues ont ce qu'on appelle. le nez, c'est-à-dire la coupe qui rend l'huile meilleure. Une mauvaise installation du segment racleur du compresseur entraîne une consommation d'huile plus élevée car le segment, au lieu de gratter l'huile dans le vilebrequin, la pousse dans la chambre de combustion. Anneau racleur. Anneau racleur L'anneau racleur a deux surfaces de travail étroites, et entre elles se trouvent des trous ovales ou ronds dans lesquels l'excès d'huile est évacué dans le bloc moteur. Les anneaux d’huile sont généralement fabriqués à partir d’un matériau moulé par injection. De nombreux anneaux d'huile utilisent un ressort de tension pour augmenter la pression sur les parois du cylindre. Le matériau des anneaux est principalement de haute qualité fonte grise. Ses caractéristiques : haute élasticité, bonnes propriétés résistance au glissement, excellente résistance à l'abrasion et températures élevées et une bonne usinabilité. L'anneau le plus haut, celui qui est le plus sollicité, est souvent chromé. La couche de chrome dure et résistante à la corrosion réduit l'abrasion de l'anneau et les bonnes propriétés de glissement suppriment la douceur du cylindre. Bobine de piston Cette pièce est principalement utilisée pour le mouvement axial du piston dans le cylindre, bien qu'elle ait également certaines fonctions d'étanchéité. De plus, en raison de la grande surface de contact avec la douceur du cylindre, c'est le principal moyen d'évacuer la chaleur du piston à travers les parois du cylindre vers le système de refroidissement du moteur. Les axes de piston se trouvent dans le manchon de piston. En raison de la différence de température de fonctionnement entre le haut et le bas de la chemise, celle-ci est conçue dans une forme légèrement conique, ne se transformant en forme cylindrique que lorsque le moteur est complètement réchauffé. Axe de piston La force du gaz agissant sur le piston et la masse d'inertie du piston et de la tige de piston sont transmises à la bielle par l'axe de piston. Les extrémités de la goupille sont insérées dans le moyeu du piston, et partie centrale comprend une tête de bielle. Il s'agit d'un joint dans lequel il est également possible de déplacer la tête de bielle dans la direction de l'axe de l'axe dans l'espace entre le manchon de piston et la partie de bielle. 7 Le boulon est soumis à des contraintes de flexion, principalement causées par la pression du gaz et les forces du corps. Dans des boulons normaux, c'est-à-dire tubulaires, il y a une tension supplémentaire due à l'aplatissement de la section transversale de l'anneau. Par conséquent, la goupille doit être en plastique à l’intérieur, mais sa surface doit être aussi dure que possible. Ces conditions correspondent à des aciers au carbone ou faiblement alliés ayant subi un traitement thermique approprié. Pour empêcher la goupille de se déplacer axialement, ce qui pourrait causer de graves dommages au lissage du cylindre, elle est utilisée comme protecteur de circlip dans les rainures sur le bord extérieur de l'alésage de la goupille ou du manchon. Un autre type de protection consiste à intégrer des axes dans les bielles. Les conditions de fonctionnement des broches sont défavorables car elles sont soumises à des forces importantes et changeantes périodiquement, en plus d'être très chaudes et les surfaces d'appui étant légèrement lubrifiées. En raison de la manière dont le roulement est assemblé, on distingue les types d'axes suivants : flottants, tournant librement dans le piston et actuellement les plus couramment utilisés, serrés dans le piston et tourne uniquement dans la bielle, serrés dans la bielle tige et tourne uniquement dans le piston. Bielle La bielle est un composant important du moteur et a trois tâches : elle relie le vilebrequin au vilebrequin, elle modifie le mouvement inverse du piston en rotation du vilebrequin, elle transmet les forces générées après le mélange dans la chambre de combustion est enflammé au vilebrequin, le couple. Prise en compte du transfert d'énormes forces longitudinales apparaissant lors de l'allumage dans la chambre de combustion au-dessus du fond. À cela s'ajoute la force d'accélération et de décélération créée par la vitesse de déplacement constamment changeante du piston, d'autant plus qu'avec toutes les forces de flexion, il en résulte un effet pendulaire. Pour ces raisons, la bielle doit avoir une résistance mécanique énorme, mais pour des raisons évidentes elle doit être la plus légère possible. Conception et forme de la bielle : à l’extrémité supérieure se trouve la tête de bielle. Une bielle est fixée à la tête, comprenant un axe de piston reliant le piston et la bielle. À cet égard, l'axe « flotte » dans la tête de bielle ou dans le manchon d'axe de piston, ou les deux. Dans certaines conceptions, le manchon ne sort pas et l'axe de piston est ensuite fixé mécaniquement ou thermiquement par la tête de piston, en chauffant la tête ou en refroidissant l'axe, puis en relâchant l'axe dans son manchon de piston. Il relie la tête à la manivelle. Le pied de bielle avec le capuchon de pied forme l'extrémité inférieure de la bielle. Cette fixation se produit dans ce qu'on appelle. écraser l'arbre, c'est-à-dire dans cette partie que la manivelle s'incline en s'éloignant de l'axe de l'arbre. Le point de fixation lui-même s'appelle le vilebrequin. L'autre moitié de ce roulement est un plateau, qui est un élément de roulement qui ne se chevauche pas. Utilisation de bagues, c'est-à-dire des paliers lisses au point de raccordement du vilebrequin, se justifie par la grande capacité de charge de ce type de palier, sa suppression du bruit et sa durabilité. De plus, le palier lisse prend moins de place et de poids par rapport aux autres types de roulements. Dans les deux cas, la raison de leur utilisation réside dans les moindres besoins en lubrification. D'un point de vue conception, il est important que, contrairement aux bagues, le roulement soit indissociable, son montage et son démontage nécessitent l'utilisation d'un vilebrequin composé de nombreuses pièces ; Vilebrequin Le vilebrequin permet le mouvement alternatif des pistons et des bielles pour faire tourner le volant. Les vilebrequins agissent sur le vilebrequin, et les pistons et bielles transmettent les forces d'inertie générées par la rotation de l'arbre et le mouvement alternatif des pistons et bielles aux arbres de vilebrequin. Ces forces provoquent une flexion et une torsion de l’arbre. Un calcul précis de ces contraintes dans le vilebrequin d’un moteur de voiture est presque impossible. Les dimensions d'un arbre correctement conçu sont si grandes que les contraintes maximales mesurées par les forces du gaz et les forces d'inertie sont faibles par rapport à la résistance du matériau de l'arbre. Les défaillances aléatoires d'arbres sont toujours causées par la fatigue provoquée par les vibrations résultant de l'action de forces de gaz variables et de forces d'inertie. Bus pétrolier. 10 Arbre principal et vilebrequins La taille des joints est déterminée par les mêmes paramètres que les tailles des manetons, à savoir la pression unitaire, la vitesse circulaire et la rigidité de l'arbre. Du fait que la rigidité de l'arbre dépend principalement du diamètre des charnières principales, ce diamètre est rendu aussi grand que possible. A noter que dans les moteurs de chariot élévateur, le raccourcissement des anneaux de support principaux peut raccourcir le moteur car dans ce cas la longueur du moteur détermine la longueur du vilebrequin, tandis que dans les moteurs en ligne le diamètre du cylindre est déterminant. Cette relation, qui implique l'alignement de deux moteurs de fourche côte à côte sur un seul axe, est due au fait que les moteurs de chariot élévateur sont principalement construits avec des déplacements courts, car cela permet de réduire le poids et le poids possible. Bras Dans les arbres supportés par chaque cylindre, les bras sont généralement usinés entièrement sur des surfaces perpendiculaires à l'axe de l'arbre, car les bras de manivelle étroitement espacés sont incapables de produire un forgeage suffisamment précis. Il est également difficile d'équilibrer le contrepoids sur de tels bras, et donc dans ces arbres, le contrepoids est le plus souvent fixé aux bras. Les axes d'arbre de bague d'huile sont généralement constitués de trous coudés reliant des paires d'axes de pivotement aux axes principaux. À travers ces trous, l'huile lubrifiante s'écoule dans les manetons. Les trous d'huile sont réalisés conformément à principe général afin de ne pas croiser et réduire la raideur du vilebrequin. Pour des raisons technologiques, les passages doivent être courts et la sortie côté traversée de la petite cale d'huile doit être facilement débarrassée des copeaux métalliques pour éviter les mauvaises surprises lors du fonctionnement. La solution moteur la plus courante en termes de système de cylindres est un moteur à quatre cylindres. Le vilebrequin d'un tel moteur est fabriqué à l'aide de la technologie de fabrication de haute précision la plus largement utilisée utilisant l'emboutissage. Ces arbres ont les supports principaux de chaque concasseur, et les extrémités des manivelles sont profilées de manière appropriée et coupées au centre, ainsi qu'un contrepoids à mâchoires large et solide, maintenant fermement les vilebrequins de l'arbre. Certains vilebrequins de moteurs à quatre cylindres sont souvent fabriqués avec seulement quatre contrepoids. Ils sont placés sur deux bras extérieurs et deux bras extérieurs. La position du vilebrequin est similaire à celle d'un moteur six cylindres dans la mesure où les vilebrequins ne sont pas inclinés à 120°, mais sont légèrement ajustés pour un angle de rotation de 15° des deux rangées de cylindres. Les arbres sur paliers principaux du point de vue de la rigidité de l'arbre et du moteur sont une solution très utile, mais pas toujours applicable. Dans les anciennes conceptions de moteurs à quatre cylindres à quatre cylindres, l'arbre de support était souvent utilisé comme double manivelle. Cela a été rendu possible grâce à moins de « puissance moteur » et à un « renforcement » du corps. Rarement utilisés dans les automobiles, les moteurs à deux cylindres peuvent avoir le vilebrequin résolu de deux manières : les manetons peuvent être du même côté, l'un en face de l'autre. Cette seconde solution, en raison de la forte irrégularité de la distance d'amorçage, n'est pas utilisée dans moteurs de voiture. Dans le premier cas, le vilebrequin peut être supporté dans un boîtier rigide sur deux supports avec un grand contrepoids au milieu, ou trois supports avec quatre contrepoids. Le module suivant discutera en détail des composants inclus dans un système de chronométrage et montrera la conception des composants individuels et leur utilisation prévue. Le moteur intégré comporte des cylindres disposés en rangée.
Chaque vilebrequin comporte deux joues dont les plans aux extrémités sont réalisés en forme d'octogone allongé. Les surfaces des joues sont traitées proprement sur tous les côtés. Les bords supérieur et inférieur des joues sont traités le long des rayons et du côté des tourillons de bielle, ils ont une surface conique.
Le vilebrequin comporte six bielles et sept tourillons principaux, ces derniers reposant sur les roulements du châssis du moteur.
Le tourillon central, quatrième et principal du vilebrequin est le plus chargé, par conséquent, pour réduire la pression spécifique sur le roulement, il est plus long que les autres.
Le septième tourillon principal du vilebrequin est persistant et possède un collier avec une surface d'extrémité polie à son extrémité.
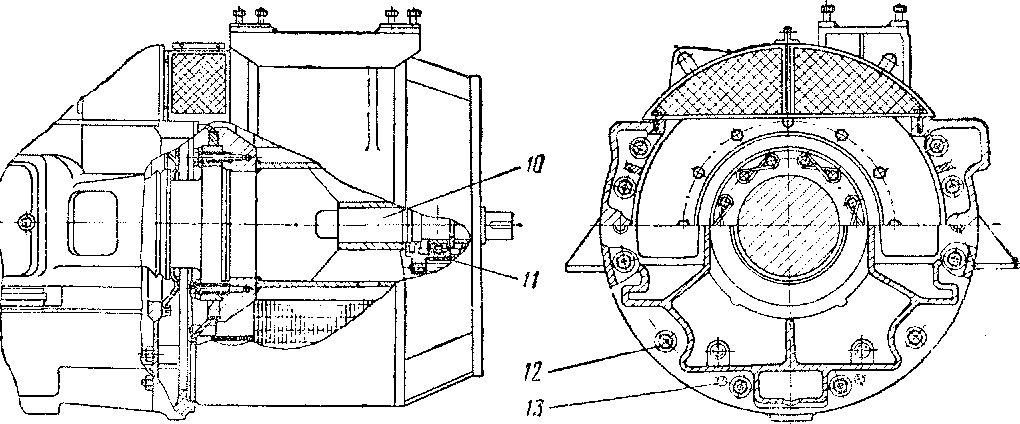
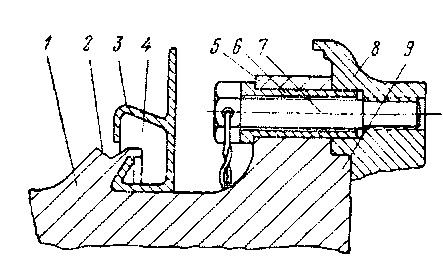
Figue. 23. Connexion du vilebrequin à l'induit du générateur : 1 - vilebrequin ; 2 - collier conique ; 3 - boîtier de joint de vilebrequin ; 4 - cavité annulaire ; 5 grandes brides de vilebrequin ; c - douille ; 7 - boulon; « - bride d'induit du générateur principal ; 9 - collier de centrage ; 10 - arbre d'extrémité ; 11 - sous-type de rouleau ; 12 - goupille de montage du stator ; 13 - broche de commande
Derrière le collier de butée du septième tourillon principal se trouve un engrenage d'entraînement divisé qui transmet la rotation à l'arbre à cames, au régulateur, aux pompes à carburant et à eau. Le nombre de dents d'engrenage est de -60. L'engrenage est monté sur une clavette parallèle pour laquelle des rainures sont découpées sur le tourillon d'arbre et sur la moitié de l'engrenage. Pour maintenir la précision de l'installation des moitiés d'engrenage, il y a deux broches aux extrémités de ces moitiés. Pour réduire la pression spécifique et assurer un engagement en douceur, les dents de l'engrenage sont obliques. L'engrenage est pressé contre le vilebrequin par deux chapes amovibles qui agrippent les surfaces cylindriques de l'engrenage des deux côtés. Les plans des extrémités des chapes ne coïncident pas avec le plan des extrémités des moitiés d'engrenage, mais lui sont parallèles. Les moitiés de chaque joug sont serrées ensemble avec deux boulons, un de chaque côté. Les boulons traversent les trous des chapes, une partie de la surface latérale pénètre dans les rainures fraisées sur les surfaces cylindriques aboutées des moitiés d'engrenage et fixent avec précision la position relative des chapes sur l'engrenage. Les têtes de boulons sont rondes avec une découpe sur la surface latérale qui les protège de la rotation. Les écrous des boulons de fourche sont en forme de château et sont fendus après serrage.
Le collier conique 2 (Fig. 23) du vilebrequin 1 derrière la chape est réalisé par étapes avec une transition en douceur de la surface cylindrique à la surface conique. Lorsque le vilebrequin tourne, l'huile jaillit de la surface du collier dans le châssis du moteur. Le bossage interne du logement 3 du joint de vilebrequin pénètre dans l'évidement annulaire sous la surface cylindrique du deuxième cône avec un jeu de 0,8 mm sur toute la surface de l'évidement. L'air provenant de la roue du ventilateur du générateur dans la cavité annulaire 4 traverse les espaces entre la rainure annulaire du vilebrequin et le bossage du carter et expulse l'huile de la surface du plus petit cône du vilebrequin dans le châssis du moteur.
A l'extrémité du vilebrequin se trouve une bride 5, renforcée par un congé côté arbre. La bride est conçue pour y fixer rigidement la bride 8 de l'induit du générateur principal. Pour centrer les brides d'accouplement, il y a un collier de centrage saillant 9 sur la surface d'extrémité extérieure de la bride de vilebrequin, et un évidement correspondant dans la bride du rotor du générateur. 12 trous ont été percés dans les deux brides de contact.
Les trous dans les deux brides sont alésés ensemble et des bagues en acier avec des colliers de butée y sont enfoncées. Les boulons 7 traversent librement les bagues 6 et sont vissés dans les trous de la bride d'induit du générateur. Des trous sont percés dans les têtes de boulons pour les épingler par paires avec du fil après serrage.
Dans les bagues 6 du côté du collier, il y a des trous avec des filetages, qui sont utilisés pour installer un extracteur lors de l'extraction des bagues.
Il y a deux autres trous filetés dans la bride du vilebrequin. Ces trous sont situés entre les bagues des deux côtés de la bride et ne sont utilisés que lors de la déconnexion de l'induit de l'alternateur du vilebrequin. Deux boulons vissés dans ces trous, en appui contre la bride d'induit du générateur, déplacent cette dernière jusqu'à ce que les douilles 6 sortent des trous de la bride d'induit. A l'extrémité opposée, le vilebrequin comporte également une bride 12 (voir Fig. 22), destinée au montage d'un disque rotatif en acier. Sur la surface cylindrique de cette bride se trouvent trois rainures semi-cylindriques dont les axes sont situés à un angle de 120° les uns par rapport aux autres et coïncident avec les axes géométriques des tourillons de bielle de l'arbre. Les rainures sont réalisées pour faciliter le traitement des cavités internes des tourillons de bielle.
Le disque rotatif 1 (Fig. 24) est relié à la bride du vilebrequin par six boulons dont deux bien ajustés. L'ajustement du disque sur le collier d'arbre est serré. Les écrous des boulons sont des écrous crénelés et, après serrage, sont clavetés séparément.
Sur la surface cylindrique du disque rotatif, à égales distances autour de la circonférence, 12 trous borgnes 2 sont percés, qui servent de douilles pour l'installation du levier lors du lancement (retour) du vilebrequin manuellement. A l'extrémité extérieure du disque rotatif, deux supports 3 sont emboutis, menant l'entraînement de l'arbre d'entraînement de la pompe à huile et du ventilateur du réfrigérateur. Un trou traversant est percé au centre du disque pour la tige de cet arbre.
Le diamètre des tourillons principaux du vilebrequin est de 240 mm, celui des tourillons de bielle est de 210 mm ; rayon de manivelle 165 mm.
Le vilebrequin est fabriqué selon GOST 704-52 en acier au carbone 35 GOST 1050-52.
Entretien et réparation. La rotation de l'arbre dans des roulements soumis à des charges alternées provoque une usure inégale des tourillons principaux et de bielle, conduisant à la formation d'une ovalité et d'une conicité de la surface des tourillons. Une ovalité excessive des tourillons entraîne une friction et une extrusion accrues de la couche de remplissage Babbitt, ce qui conduit à son tour à l'affaissement des tourillons d'arbre individuels et, par conséquent, à la formation de fissures sur les tourillons et les tourillons et à la rupture de l'arbre. Par conséquent, lors du fonctionnement d'une locomotive diesel, il est nécessaire d'établir une surveillance périodique et une surveillance régulière de l'état des tourillons principaux et de bielle du vilebrequin, de surveiller régulièrement l'état de l'huile utilisée et de ne pas utiliser d'huile à haute teneur en huile. impuretés mécaniques, teneur en cendres et faible viscosité, qui affectent une usure plus rapide des tourillons.
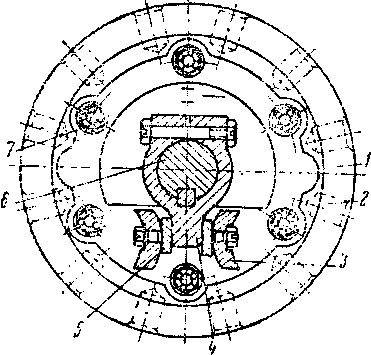
Fii. 24. Disque rotatif : 1- disque ; 2- trous borgnes : supports ; -1 - entraînement de pompe à huile ; 5 - cracker remplaçable ; je" - arbre d'entraînement de la pompe à huile ; 7 boulons pour fixer le disque rotatif
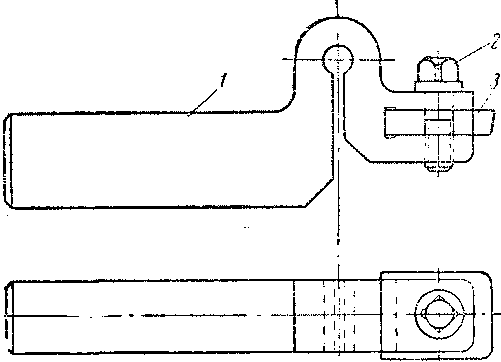
Figue. 25. Coupe-ressort : 1 - tige de coupe ; 2 - vis de fixation ; 3 - insert de coupe pobedite
Pour déterminer l'ovalité et le faux-rond des tourillons principaux, on utilise un indicateur dont le support est fixé sur l'axe de montage du roulement, et le pied est installé sur le tourillon à une distance d'environ 15 mm du congé, assurant sa libre mouvement de haut en bas. Faites pivoter l'échelle pour régler la flèche indicatrice sur la position zéro. Tout en tournant le vilebrequin, remarquer la déviation de l'aiguille indicatrice tous les 45° (faire une note à la craie sur la joue d'arbre adjacente à l'opposé de l'emplacement de chaque mesure). Ensuite, l'indicateur est transféré et la patte est installée à une distance de 15 mm du deuxième congé du même col. Faites tourner le vilebrequin d'un tour en remarquant l'écart de l'aiguille indicatrice par rapport à la position de la balle tous les 45 (les marques sont faites à la craie sur l'autre joue). Tous les tourillons de vilebrequin sont vérifiés de la même manière. Dans ce cas, la position de l'arbre dans laquelle les premier et sixième cols de manivelle sont en position verticale supérieure est prise comme position zéro (initiale) pour chaque col. La mesure est considérée comme effectuée correctement ; si la flèche indicatrice, après un tour complet de l'arbre, prend sa position zéro d'origine.
A l'aide des marques faites sur les joues, les emplacements d'ovalité et de battement de tous les tourillons molaires sont déterminés. Il est à noter que les mesures d'ovalité et de faux-rond des tourillons effectuées dans le bâti moteur ne permettent de juger qu'approximativement de l'état des tourillons de vilebrequin. L'état réel des tourillons de vilebrequin doit être déterminé à un niveau moyen et rénovation majeure sur la plaque de commande. Le diamètre des tourillons de maneton du vilebrequin est mesuré avec une pince micrométrique mesurant 200-225 mm dans trois plans le long de la longueur du tourillon avec la manivelle positionnée en position de manivelle. m.t. et en position horizontale. Sur la base des résultats de mesure obtenus, l'ovalité et la conicité des tourillons de bielle sont déterminées.
S'il y a une ovalité et une conicité des tourillons principaux et de bielle de plus de 0,20 mm, ainsi qu'un faux-rond des tourillons principaux dépassant 0,30 mm, l'arbre doit être réparé. La correction des tourillons de vilebrequin dans le châssis du moteur n'est pas recommandée, car les moindres erreurs et imprécisions de mesure lors des réparations peuvent entraîner une violation de l'axe géométrique des tourillons d'arbre principal, une augmentation de leur faux-rond et une inclinaison des tourillons de bielle.
Pour que les axes de tous les tourillons principaux coïncident et pour éliminer le faux-rond, le vilebrequin est installé sur un tour DIP-500 pour le tournage et le meulage ou la finition ultérieurs de tous ses tourillons principaux à la taille requise. Dans ce cas, la rainure des congés des tourillons principaux et de bielle doit être réalisée avec la fraise à ressort illustrée ci-contre. figue. 25.
Tous les tourillons principaux sont généralement usinés selon la même taille de réparation ; À titre exceptionnel, il est permis de traiter des cols individuels à la taille la plus proche. Les graduations de réparation pour les tourillons principaux sont fixées tous les 0,5 mm et pour les bielles, tous les 0,25 mm.
En cas d'usure légère, les tourillons principaux et de bielle peuvent être amenés aux dimensions géométriques requises par usinage. L'exactitude de la forme cylindrique est vérifiée par des tours. Dans ce cas, pour terminer les premier, deuxième, troisième, cinquième et sixième tourillons, le même tour 6 (Fig. 26), de longueur égale à la longueur du tourillon, est utilisé. Pour les quatrième et septième journaux, les tours 5 et 7 sont utilisés.
Les tours sont coulés en bronze ou en aluminium et usinés le long du diamètre des tourillons principaux avec une marque de 0,10 mm, nécessaire au grattage et à l'ajustement fin du tour lui-même au calibre. Comme on peut le voir sur la Fig. 26, les tours 5, 6 et 7 sont une sorte de doublure couvrant 113 tours de cou. Le tour a deux poignées sur le dessus.
Pour affiner les tourillons principaux et de bielle, le vilebrequin doit être installé sur un support spécial, qui est une plaque à trois supports. Le vilebrequin est installé sur les lunettes avec les premier, quatrième et septième tourillons principaux et est vérifié pour l'absence d'ovalité, de conicité, de faux-rond des tourillons, de faux-rond de la bague de centrage et d'absence de biais des tourillons de bielle. Avant finition, les tourillons principaux sont sciés sur toute la surface avec une petite scie personnelle. Ensuite, la surface du recouvrement est recouverte d'une fine couche uniforme de peinture azur et le recouvrement est installé sur le col, en le tournant 2 à 3 fois sur le col de la tige. Après avoir retiré le tour 5, utilisez une scie fine (velours) pour couper les traces de peinture sur le col. Le limage s'effectue ainsi jusqu'à ce que l'empreinte de peinture soit localisée sur tout le col sous forme de petites taches régulières. Parallèlement au limage du col, son diamètre est constamment mesuré à l'aide d'une pince micrométrique mesurant 225-250 mm, déterminant la forme correcte du col. C'est ainsi que sont terminés tous les journaux principaux, à l'exception du quatrième et du septième, pour lesquels des tours prolongés sont utilisés. La finition des tourillons principaux est considérée comme terminée à condition que leur ovalité, leur faux-rond et leur conicité au total n'excèdent pas 0,03 mm.
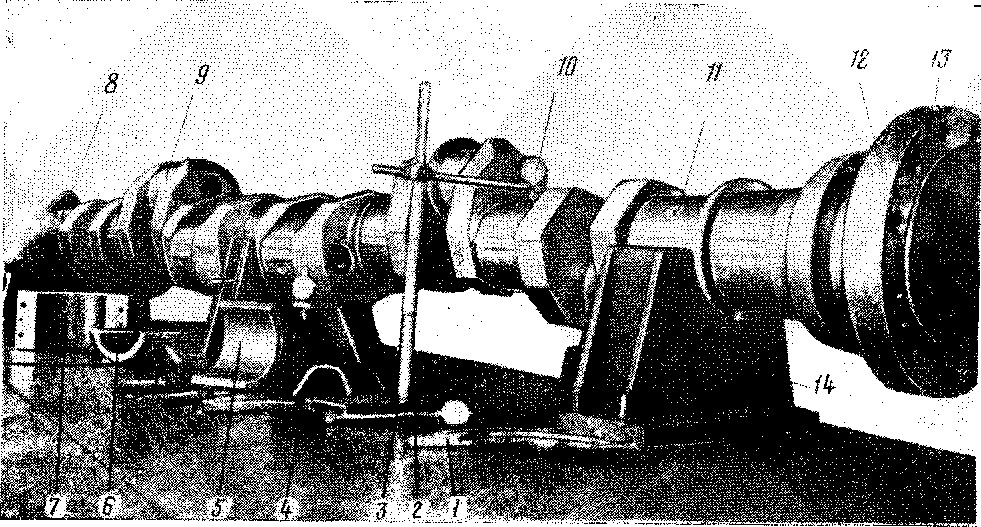
Figue. 26. Installation du vilebrequin sur le plateau de commande : 1 - support micrométrique ; 2 - jauge d'alésage avec indicateur ; 3 - représente l'indicateur ; 4 - indicateur ; 5 - tour pour le quatrième journal principal ; en - tour pour les premier, deuxième, troisième, cinquième, sixième journaux principaux ; 7 - tour pour le septième journal ; 8 - premier tourillon principal du vilebrequin ; 9 - deuxième tourillon de bielle ; 10 - indicateur ; 11 - col de la septième molaire ; 12 - grande bride ; 13 - collier de centrage ; 14-lunette
Pour corriger l'ovalité, la conicité et le désalignement des tourillons de bielle, une machine spéciale disque-radial est nécessaire, et donc les tourillons de bielle sont « le plus souvent corrigés en limant un petit pylône personnel avec ultérieur ! finir par roder 6.
Après la finition, les tourillons principaux et de bielle sont soigneusement polis, d'abord avec d'étroites bandes de toile émeri sèche sur un support, puis sur un tour à l'aide de pinces en bois, dans lesquelles sont placées de larges bandes de papier de verre lubrifiées à l'huile.
Après toutes les opérations ci-dessus, le vilebrequin est vérifié sur la plaque de commande.
Pendant le fonctionnement, il y a eu des cas de déflexion du vilebrequin dus à la fonte des chemises.
En fonction de l'ampleur de la déviation, les vilebrequins peuvent être redressés avec l'autorisation du ministère des Chemins de fer. Le processus d'édition est généralement effectué comme suit.
Le vilebrequin est installé au centre du tour (sans supports) ou sur le plateau (sur les deux supports extérieurs) de manière à ce que le plus grand point de déflexion soit dirigé vers le haut. Un indicateur est installé sur le col ou la joue de l'arbre.
L'amiante humide est appliquée sur le col qui présente la plus grande déviation. Un trou d'un diamètre de 50 à 60 mm est laissé au milieu de l'amiante. Par ce trou, l'arbre est chauffé avec un brûleur à gaz jusqu'à une température de 200-250°. Ensuite, la partie chauffée du cou peut refroidir lentement.
Lorsqu'elle est chauffée, la déviation augmente généralement légèrement, mais lorsqu'elle est refroidie, elle diminue par rapport à la valeur d'origine. Ceci est fait plusieurs fois, en changeant uniquement l'emplacement de chauffage sur le même tourillon jusqu'à ce que le vilebrequin acquière une forme droite. Le processus d'édition prend environ 50 à 60 heures.
Dans le cas où les dépôts ou ateliers ne disposent pas de plateau de commande et de grandes machines spéciales pour faire tourner les tourillons principaux et de manivelle de l'arbre, le classement des tourillons s'effectue dans l'ordre suivant : retirer le cadre du carter ainsi que l'arbre du châssis de la locomotive diesel, puis ouvrez les roulements principaux et mesurez le faux-rond des tourillons des roulements principaux et le faux-rond des grandes et petites brides d'arbre. Étant donné que les brides de l'arbre ne sont jamais affûtées lors des réparations et qu'elles ne s'usent pas lors du fonctionnement de l'arbre, leur axe géométrique coïncide toujours avec l'axe géométrique des tourillons du nouvel arbre. Par conséquent, les surfaces cylindriques des brides sont contrôlées pour déterminer l'axe géométrique de tous les tourillons de l'arbre lors de leur remplissage. Pour réparer, l'arbre est retiré du cadre, placé sur des chevalets en bois, nettoyé avec des grattoirs en cuivre, poncé manuellement avec du papier de verre et vérifié avec un détecteur de défauts électromagnétique pour l'absence de fissures. Tous les tourillons sont ensuite mesurés avec une jauge micrométrique pour déterminer l'usure. Si l'arbre présente une usure supérieure à celle autorisée, les tourillons doivent alors être limés. Lorsque vous commencez à limer les tourillons d'arbre, n'oubliez pas que sur les tourillons principaux, après un travail prolongé, des bandes saillantes se forment dans la partie médiane. Au toucher, vous pouvez déterminer la partie usée du cou, au-dessus de laquelle cette ceinture dépasse, et la partie non travaillée, où cette ceinture est quasiment invisible. Tout d’abord, les collets des première, quatrième et septième molaires sont sciés. Pour ce faire, après avoir retiré le vilebrequin du cadre du carter, retirez les coquilles inférieures des deuxième, troisième, cinquième et sixième roulements. Ensuite, l'arbre est placé sur les trois anciennes chemises inférieures restantes et mesuré avec un indicateur de faux-rond sur les surfaces radiales des deux brides. Ensuite, l'arbre est retiré, posé sur les tréteaux, et les premier, quatrième et septième tourillons sont sciés aux endroits correspondant au plus grand faux-rond (tout d'abord, la partie du tourillon qui n'a pas fonctionné est limée, c'est-à-dire , celui où la ceinture est quasiment invisible). Après cela, l'arbre est à nouveau placé dans le cadre sur les trois mêmes doublures et le faux-rond des brides est déterminé. Le voile devrait maintenant diminuer. Ceci est répété jusqu'à ce que le faux-rond de la grande bride atteigne 0,10 mm et que la petite bride atteigne 0,03 mm. Après cela, nous pouvons supposer que les premier, quatrième et septième tourillons sont approximativement insérés dans le même axe géométrique avec les deux brides.
Ensuite, ils commencent à limer les quatre cols molaires restants. Pour ce faire, déterminez leur faux-rond sur les trois mêmes doublures inférieures, en enregistrant les lectures de l'indicateur sur les joues du cou. Ensuite, la hampe est retirée et les cous sont limés sur les chèvres aux endroits où elles sont battues. De cette manière, le faux-rond de ces tourillons est ramené à 0,03 mm. Habituellement, vous devez placer le vilebrequin dans le cadre et le reculer 10 à 12 fois lors du classement et de la finition des sept tourillons.
Après l'usinage, le vilebrequin subit une inspection complète qui comprend principalement les éléments suivants.
1. Les tourillons principaux et de bielle sont mesurés avec des pinces micrométriques de tailles appropriées, et le diamètre de chaque tourillon est mesuré en trois endroits le long du cou et dans trois points le long de sa circonférence. Dans ce cas, l'ovalité, la conicité et la forme en tonneau de tous les cols ne doivent pas dépasser 0,02 mm. Krr-setness, c'est-à-dire une diminution du diamètre au milieu du cou et le duvet du cou ne sont pas autorisés.
2. Pour vérifier le faux-rond des tourillons principaux, déterminer l'inclinaison des tourillons de bielle, la cambrure des joues de manivelle et d'autres contrôles, le vilebrequin est placé avec les premier, quatrième et septième tourillons principaux sur trois lunettes installées sur le plaque de commande. Le vilebrequin est installé parallèlement au plateau à l'aide des supports de lunettes 14 (Fig. 26), équipés de vis qui assurent le mouvement vertical des lunettes, et est contrôlé par un indicateur. Après avoir installé le vilebrequin sur le plateau avec une précision de 0,01 mm, une marque à la craie est faite sur l'une de ses brides d'extrémité, qui est ensuite utilisée pour déterminer l'emplacement du faux-rond de chaque tourillon mesuré et la rotation complète de l'arbre lors du contrôle . Pour vérifier, utiliser l'indicateur 10, monté sur le support 3. Le pied de l'indicateur est installé sur le dessus du col à une distance de 15 mm du congé. Tout en faisant tourner l’arbre, observez la position de la flèche indicatrice. Ensuite, l'indicateur est transféré sur un autre congé du même col et, en tournant également le vilebrequin d'un tour complet, surveillez la position de la flèche. C'est ainsi que l'on vérifie le runout de tous les journaux principaux. Dans ce cas, l'écart maximum ne dépasse pas 0,03 mm.
3. Simultanément au contrôle du faux-rond des tourillons principaux, on vérifie le collier de centrage 13, dont le faux-rond radial ne peut être supérieur à 0,03 mm. Vérifier en même temps le faux-rond du collier situé entre les septième et huitième tourillons. Son faux-rond ne dépasse pas 0,05 mm. Le faux-rond de la grande bride ne doit pas dépasser 0,1 mm.
4. L'absence de déformation des tourillons de bielle est vérifiée par rapport à l'axe géométrique des tourillons principaux. Chaque cou est vérifié avec le genou en position verticale et horizontale. Pour effectuer ce contrôle, le vilebrequin est tourné sur les lunettes et installé de manière à ce que deux manivelles situées au même angle prennent une position verticale. Un indicateur 10 est installé sur l'un des tourillons de ces manivelles à une distance de 15 mm du congé et la position exacte de la flèche est notée. Ensuite, l'indicateur est transféré sur un autre congé du même maneton et la déviation de la flèche est à nouveau notée. La différence des écarts de la flèche indicatrice montrera l'inclinaison du tourillon par rapport à l'axe géométrique des tourillons principaux, préalablement installés (voir point 2) parallèlement à la dalle le long de l'indicateur. Ensuite, sans perturber la position du vilebrequin, l'indicateur est transféré sur le tourillon d'une autre manivelle, debout en position verticale, et sa distorsion est déterminée de la même manière. Ensuite, l'arbre est tourné de 90° pour que les mêmes manivelles prennent une position horizontale, un indicateur est installé sur l'un des tourillons, également à une distance de 15 mm du congé, et la déviation de la flèche est notée. La même chose est faite lors du transfert de l'indicateur sur un autre congé du même col. La différence dans les écarts des flèches montrera l'inclinaison du tourillon en position horizontale de la manivelle. Le désalignement des tourillons de bielle restants est vérifié de la même manière, et en position verticale et horizontale pour les vilebrequins neufs ou réparés, la valeur du désalignement ne doit pas dépasser 0,02 mm.
5. L'angle de carrossage des manivelles du vilebrequin est vérifié sur la même plaque de commande également avec l'indicateur 10. Pour ce contrôle, le vilebrequin est installé de manière à ce que les première et deuxième manivelles soient dirigées vers le haut à partir du premier tourillon principal selon un angle de 120° , et leurs tourillons sont dans une position horizontale par rapport au plan de la plaque, qui est déterminée par la position zéro de la flèche indicatrice. Ensuite, l'indicateur est transféré aux tourillons des sixième et cinquième manivelles, qui occupent la même position, et l'angle de carrossage par rapport aux première et deuxième manivelles est déterminé par la déviation de la flèche. L'écart est autorisé de ± 30", ou en mesure linéaire pas plus de 2,5 mm. Lors de la vérification des angles de carrossage des manivelles suivantes, le vilebrequin est installé de manière à ce que les deuxième et troisième manivelles soient situées vers le haut de tout tourillon principal à un angle de 120°. . Ensuite, l'indicateur est transféré aux tourillons des cinquième et quatrième manivelles et, par la déviation de la flèche, détermine l'angle de carrossage par rapport aux deuxième et troisième manivelles. Les angles de carrossage des manivelles suivantes sont déterminés dans le même ordre.
6. La longueur du rayon des manivelles est vérifiée avec l'indicateur 10 et un autre indicateur 4 installé sur un appareil spécial. Pour vérifier, il est nécessaire de placer le vilebrequin dans une position dans laquelle la manivelle testée occupera une position strictement verticale. Ensuite, à l'aide de l'indicateur 10, trouvez le point haut du maneton, mesurez cette distance par rapport au plan du plateau et soustrayez la moitié du diamètre du maneton de la taille obtenue. Ensuite, avec la même installation de l'arbre, le deuxième indicateur 4 permet de retrouver le point supérieur du tourillon adjacent, de mesurer la distance du plan de la dalle à ce point et de soustraire la moitié du diamètre du tourillon. La valeur résultante est soustraite de la mesure précédente. Le résultat de la soustraction sera la longueur du rayon de manivelle égale à 165 ± 0,2 mm.
7. Tous les congés de col, les rainures bouclées et toutes les dimensions linéaires sont vérifiés à l'aide de gabarits spéciaux, d'agrafes, de jauges et d'autres outils spécialement conçus à cet effet.
Le vilebrequin est placé dans le châssis du moteur sur un support spécial, constitué d'une plaque métallique à surface rabotée, posée sur une fondation. La dalle comporte des rainures spéciales dans lesquelles des têtes de boulons sont installées pour fixer deux poutres en fonte. Les plans inférieurs des poutres servent à les fixer à la dalle, et le châssis moteur est installé sur les plans supérieurs. La dalle de support et les poutres d'installation qui y sont fixées sont contrôlées au moins une fois par mois avec une règle de 3 m de long et un niveau d'au moins 300 mm de long. Dans ce cas, l'imprécision ne dépasse pas 0,10 mm par mètre de longueur de mesure.
Avant de poser le vilebrequin dans le châssis du moteur, une fine couche de peinture azur est appliquée sur le lit dans le châssis et dans les capots. Ensuite, les doublures sont mises en place, fermées avec des couvercles et fixées avec des écrous. Dans le même temps, les écrous sont ramenés à leur position normale, déterminée par les repères marqués sur chaque goujon et écrou sur le dessus. Dans cet état, toutes les doublures (à l'exception de celle de poussée) sont vérifiées pour l'ajustement de leurs surfaces arrière aux lits du cadre et du couvercle. Une jauge d'épaisseur de 0,03 mm ne doit pas passer à une profondeur supérieure à 0-15 mm du. bord d'extrémité externe du revêtement. En même temps, vérifiez l'écart à six endroits entre les colliers du revêtement de poussée et les extrémités du lit, où l'écart est autorisé dans la plage de 0,03 à 0,10 mm, ainsi que la différence d'écart. ne doit pas dépasser 0,03 mm. Si les mesures sont satisfaisantes, les couvercles sont retirés et les doublures sont retirées des lits pour inspection. L'empreinte de la peinture azur sur la surface arrière de chaque doublure doit être d'au moins 80 sur toute la surface. Les revêtements sont replacés dans le lit et, à l'aide d'entretoises placées sur les goujons, sont serrés aux écrous des lits.
Pour éviter d'endommager les tourillons du vilebrequin lors de son abaissement dans le cadre, des écrous borgnes en aluminium à sommet conique sont placés sur les goujons des premier, quatrième et butée, qui servent de guides lors de l'abaissement et de la pose de l'arbre dans le cadre. Après avoir posé la tige sur les liners, une deuxième mesure est effectuée avec une jauge d'épaisseur de 0,03 mm entre la face occipitale du liner et le lit du cadre, ainsi qu'entre le col et le remplissage Babbitt sur un arc de 20°. Si la jauge d'épaisseur de 0,03 mm ne s'étend pas depuis l'extrémité sur une longueur supérieure à 15 mm, alors le vilebrequin est correctement posé sur ses roulements. S'il y a des espaces de plus de 0,03 mm, sélectionnez des doublures du groupe suivant qui sont 0,02 à 0,04 mm plus pleines. Les mesures avec une jauge d'épaisseur de 0,03 mm sont effectuées dans quatre positions du vilebrequin en le tournant de 90°.
Le contrôle de l'emplacement du vilebrequin s'effectue à l'aide de peinture. A cet effet, avant de poser l'arbre, tous ses tourillons principaux sont recouverts de peinture azur, l'arbre est placé dans le cadre et tourné de 2 à 3 tours ; retirez ensuite l'arbre du cadre et déterminez l'ajustement des tourillons par l'empreinte de peinture sur les doublures et, si nécessaire, coupez légèrement ces dernières.
Parfois, le vilebrequin est posé le long de « frottements ». Dans ce cas, les tourillons d'arbre sont essuyés et les chemises sont grattées en fonction de la réflexion formée en frottant le tourillon sur la surface du régule. La pose d'arbres avec des « frottements » est considérée comme plus avancée et plus subtile qu'avec de la peinture et est utilisée lors de la pose de vilebrequins sur les moteurs D50.
Pour obtenir l'espace requis de 0,12 mm dans les « moustaches » des liners, les moitiés inférieure et supérieure des liners sont grattées sur une longueur de 50 mm du plan du connecteur. Les moitiés des chemises sont grattées le long des tourillons d'arbre ou sur des mandrins spéciaux, puis installées dans le cadre et les écrous sont pré-serrés. Les écrous sont serrés avec une clé à douille et un pied-de-biche de 300 mm de long par un seul ouvrier. Pour éviter les déformations des joints des liners et des plans des couvercles, les écrous des quatrième et septième liners doivent être serrés en croix. Lors du serrage final des écrous sur les goujons, utilisez la même clé à douille, mais avec deux pieds-de-biche de 1 000 mm de long. Le serrage est effectué par deux ouvriers. Le serrage des écrous commence généralement par le palier central, le quatrième et le palier principal, puis les roulements adjacents - les troisième, cinquième, deuxième, sixième et septième - sont fixés tour à tour. 1Pour éviter que les écrous ne se mélangent lors d'une révision ou d'une réparation du moteur, des numéros de série de un à dix-huit sont gravés sur chacun d'eux ainsi qu'à l'extrémité du goujon. Le comptage s'effectue à partir du premier insert, tous les nombres impairs étant situés côté sortie, et les nombres pairs côté entrée.
Après avoir serré les écrous des chapeaux de palier principal, les jeux d'huile radiaux entre les tourillons d'arbre et les chemises doivent être compris entre 0,12 et 0,18 lsh. La différence d'espacement sur un col, mesurée des deux côtés de la doublure, ne doit pas dépasser 0,03 mm. Les jeux radiaux dans les revêtements sont généralement mesurés avec une jauge d'épaisseur composée de deux ou trois plaques, ce qui donne des mesures plus précises. Dans la butée, le jeu d'huile et l'écart « moustache » sont vérifiés en plaçant trois ou quatre fils conducteurs d'un diamètre de 1 mm sur le tourillon d'arbre avant de serrer le couvercle, puis en mesurant l'épaisseur des fils aplatis. Le non-parallélisme et l'obliquité des axes géométriques des tourillons d'arbre dans le châssis sont vérifiés à l'aide de fils à plomb et d'indicateurs installés aux deux extrémités du châssis. Dans ce cas, la différence entre les lectures de l'indicateur doit être inférieure à 0,03 mm. Le faux-rond axial du plan de la bride destiné au montage du stator du générateur principal par rapport à l'axe du vilebrequin doit être inférieur à 0,05 mm pour un diamètre de 1,225 mm. L'imprécision est éliminée par grattage. Le faux-rond du collier de montage du cadre par rapport à l'axe du vilebrequin ne doit pas dépasser 0,1 mm. Dans les deux cas, le faux-rond est vérifié à l'aide d'un indicateur fixé au support de la bride de l'arbre. Le vilebrequin est décalé vers pompe à huile et appuyé fermement contre l'épaulement extérieur de la butée. Dans cette position, le faux-rond de la grande bride du vilebrequin, au plan duquel est fixé le rotor du générateur principal, est également vérifié. Ici, le faux-rond ne dépasse pas 0,05 mm. En plus des fils à plomb, le faux-rond du vilebrequin est vérifié avec un indicateur le long de la collerette d'un diamètre de 395 mm par rapport à l'axe des chemises principales ; le faux-rond ne doit pas dépasser 0,03 mm. L'écart axial du septième tourillon du vilebrequin dans la butée doit être de 0,24 à 0,38 mm. Lors de la mesure de la cambrure des joues dans quatre positions au même rayon par rapport à l'axe de l'arbre et dans la même manivelle, l'écart ne dépasse pas 0,05 mm. Une grande cambrure des joues indique une mauvaise installation du vilebrequin. Tourner facilement le vilebrequin par une seule personne à l'aide d'un levier d'environ 300 mm de long indique que le vilebrequin est correctement installé dans ses paliers principaux. Après avoir placé le vilebrequin dans le châssis, un boîtier est placé pour empêcher l'huile d'être projetée vers le générateur principal, et le générateur principal est soudé au moteur.
Installation de générateur. Lors du montage du générateur principal, le stator est relié par des goujons (voir Fig. 23) à la bride du châssis du moteur et pré-fixé avec des écrous. Ensuite, l'armature du générateur est soudée à la bride du vilebrequin et reliée par six bagues et boulons étanches temporaires (technologiques). Après cela, les axes géométriques de l'induit et du vilebrequin sont alignés. L'alignement s'effectue en mesurant la cambrure des joues des quatrième, cinquième et sixième manivelles du vilebrequin. Dans ce cas, une tolérance est définie qui ne dépasse pas 0,05 mm. L'alignement des joues est vérifié avec une goupille micrométrique spéciale (Fig. 27) avec un indicateur dans quatre positions et à un rayon de l'axe de l'arbre, en tournant à chaque fois l'arbre de 80°. Parallèlement, des mesures sont effectuées des entrefers entre la surface de l'induit et les pôles principaux du stator. Ces écarts doivent être inférieurs à 4 mm ± 10 %.
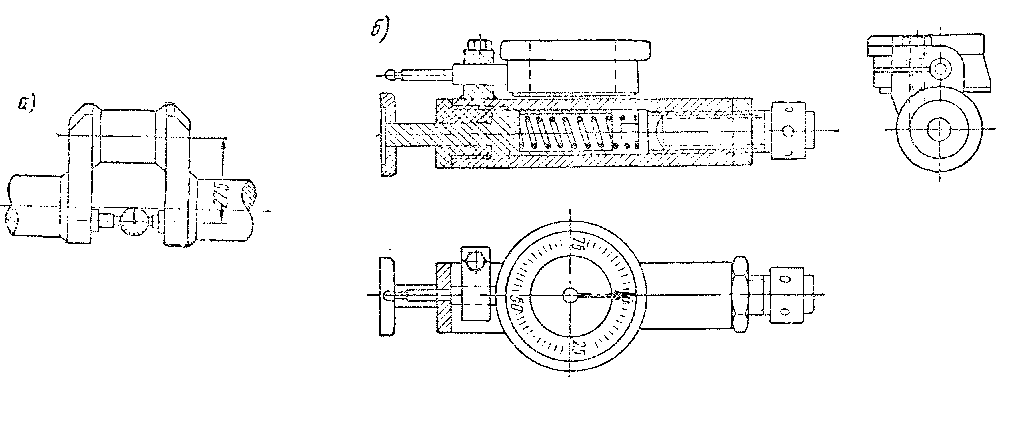
Figue. 27. Contrôle du vilebrequin par carrossage des joues : o - schéma de pose du pion micrométrique ; b - broche micrométrique
Si les résultats ne sont pas satisfaisants, les goujons fixant le stator du générateur sont desserrés et le stator est décalé par rapport au châssis, en fonction des mesures précédentes, ou la bride du châssis est grattée. Comme on le sait, les goujons du stator pénètrent dans les trous des brides du cadre avec un espace, ce qui permet de décaler le stator du générateur par rapport au cadre de 0,7 à 0,9 mm. Après alignement, des broches de fixation coniques sont installées. Parallèlement à l'alignement, le faux-rond de l'arbre d'extrémité 10 (voir Fig. 23) de l'induit du générateur est vérifié à l'aide d'un indicateur. Ce faux-rond ne doit pas dépasser 0,05 mm. Les jeux d'huile dans les roulements principaux, mesurés avant et après l'alignement, ne peuvent pas varier de plus de 0,01 mm.
Après l'alignement final du stator et de l'induit du générateur principal, les écrous fixant le stator au châssis du moteur sont pré-serrés. Le serrage s'effectue à l'aide d'une clé aveugle à une extrémité de 300 mm de long avec la force vive d'un ouvrier. La procédure de serrage est indiquée sur la Fig. 28.
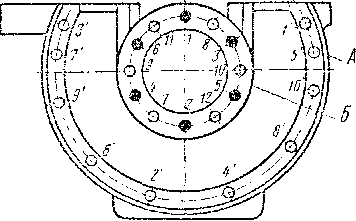
Figue. 28. La procédure de serrage des goujons et boulons lors du montage du générateur sur le moteur :
A - châssis moteur ; B - bride de vilebrequin ; 2",..-trous dans la bride du cadre et la procédure de serrage des écrous ; 1, 2____-trous dans la bride du vilebrequin et la procédure d'installation et de serrage des bagues à ressort et des boulons
Avant l'alignement, les brides d'induit et de vilebrequin ont été reliées les unes aux autres avec six bagues serrées temporairement et pré-serrées avec une clé de 300 mm de long dans l'ordre indiqué sur la Fig. 28. Ensuite, dans le même ordre, serrez-les avec une clé de 2 000 mm de long en utilisant la force de deux ouvriers, en serrant chaque boulon à moitié jusqu'à ce qu'il soit complètement serré. Les six trous libres restants sont élargis, des bagues de montage permanentes et des boulons y sont placés et ils sont serrés dans l'ordre indiqué sur la Fig. 28. Ensuite, les six boulons temporaires précédemment installés sont desserrés et retirés, les trous libérés sont élargis, les bagues et les boulons permanents sont installés et fixés de la même manière que les précédents.