Независимая подвеска передних колес. Устройство передней подвески - какие бывают варианты
Подвеска автомобиля представляет собой совокупность элементов, обеспечивающих упругую связь между кузовом (рамой) и колесами (мостами) автомобиля. Главным образом подвеска предназначена для снижения интенсивности вибрации и динамических нагрузок (ударов, толчков), действующих на человека, перевозимый груз или элементы конструкции автомобиля при его движении по неровной дороге. В то же время она должна обеспечивать постоянный контакт колеса с дорожной поверхностью и эффективно передавать ведущее усилие и тормозную силу без отклонения колес от соответствующего положения. Правильная работа подвески делает управление автомобилем комфортным и безопасным. Несмотря на кажущуюся простоту, подвеска является одной из важнейших систем современного автомобиля и за историю своего существования претерпела значительные изменения и усовершенствования.
Попытки сделать передвижение транспортного средства мягче и комфортнее предпринимались еще в каретах. Изначально оси колес жестко крепились к корпусу, и каждая неровность дороги передавалась сидящим внутри пассажирам. Повысить уровень комфорта могли лишь мягкие подушки на сиденьях.
Зависимая подвеска с поперечным расположением рессоры
Первым способом создать упругую «прослойку» между колесами и кузовом кареты стало применение эллиптических рессор. Позже данное решение было позаимствовано и для автомобиля. Однако рессора уже стала полуэллиптической и могла устанавливаться поперечно. Автомобиль с такой подвеской плохо управлялся даже на небольшой скорости. Поэтому вскоре рессоры стали устанавливать продольно на каждое колесо.
Развитие автомобилестроения повлекло и эволюцию подвески. В настоящее время насчитываются десятки их разновидностей.
Основные функции и характеристики подвески автомобиля
У каждой подвески существуют свои особенности и рабочие качества, которые напрямую влияют на управляемость, комфорт и безопасность пассажиров. Однако любая подвеска вне зависимости от своего типа должна выполнять следующие функции:
- Поглощение ударов и толчков со стороны дороги для снижения нагрузок на кузов и повышения комфорта движения
- Стабилизация автомобиля во время движения за счет обеспечения постоянного контакта шины колеса с дорожным покрытием и ограничения чрезмерных кренов кузова
- Сохранение заданной геометрии перемещения и положения колес для сохранения точности рулевого управления во время движения и торможения
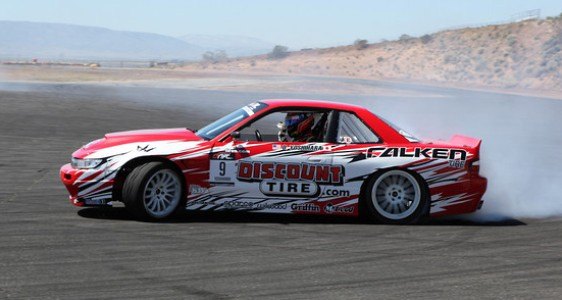
Жесткая подвеска автомобиля подходит для динамичной езды, при которой требуется мгновенная и точная реакция на действия водителя. Она обеспечивает небольшой дорожный просвет, максимальную устойчивость, сопротивляемость крену и раскачиванию кузова. Применяется в основном на спортивных автомобилях.
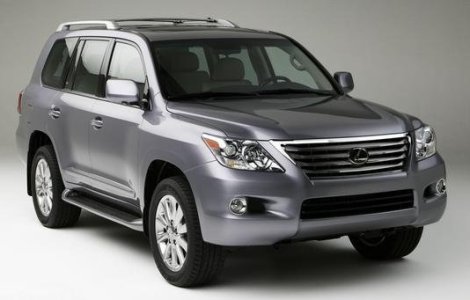
В большинстве легковых авто применяется мягкая подвеска. Она максимально сглаживает неровности, однако делает автомобиль несколько валким и хуже управляемым.
Если требуется регулируемая жесткость, на автомобиль монтируется винтовая подвеска. Она представляет собой стойки-амортизаторы с изменяемой силой натяжения пружины.
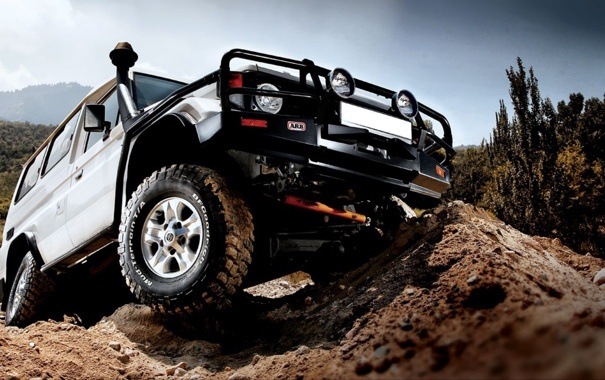
Ход подвески — расстояние от крайнего верхнего положения колеса при сжатии до крайнего нижнего при вывешивании колес. Ход подвески во многом определяет «внедорожные» возможности автомобиля. Чем больше его величина, тем большее препятствие можно преодолеть без удара об ограничитель или без провисания ведущих колес.
Устройство подвески
Любая подвеска автомобиля состоит из следующих основных элементов:
- Упругое устройство – воспринимает нагрузки от неровностей дорожной поверхности. Виды: пружины, рессоры, торсионы, пневмоэлементы и т.д.
- Демпфирующее устройство — гасит колебания кузова при проезде через неровности. Виды: все типы амортизаторов.
- Направляющее устройство — обеспечивает заданное перемещение колеса относительно кузова. Виды: рычаги, поперечные и реактивные тяги, рессоры. Для изменения направления воздействия на демпфирующий элемент в спортивных подвесках pull-rod и push-rod применяются рокеры.
- Стабилизатор поперечной устойчивости — уменьшает поперечный крен кузова.
- Резино-металлические шарниры — обеспечивают упругое соединение элементов подвески с кузовом. Частично амортизируют, смягчают удары и вибрации. Виды: сайлент-блоки и втулки.
- Ограничители хода подвески — ограничивают ход подвески в крайних положениях.
Классификация подвесок
В основном подвески подразделяются на два больших типа: зависимые и независимые. Данная классификация определяется кинематической схемой направляющего устройства подвески.
Зависимая подвеска
Колеса жестко связаны посредством балки или неразрезного моста. Вертикальное положение пары колес относительно общей оси не изменяется, передние колеса – поворотные. Устройство задней подвески аналогичное. Бывает рессорная, пружинная или пневматическая. В случае установки пружин или пневмобаллонов необходимо применение специальных тяг для фиксирования мостов от перемещения.
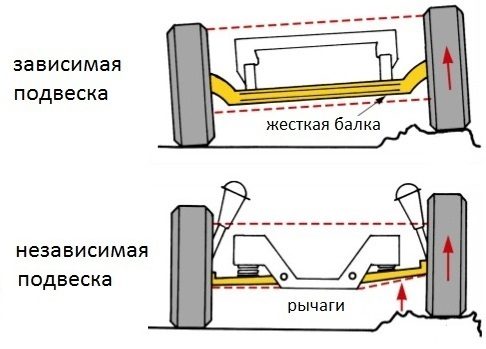
- простая и надежная в эксплуатации
- высокая грузоподъемность
- плохая управляемость
- плохая устойчивость на больших скоростях
- меньшая комфортабельность
Независимая подвеска
Колеса могут изменять вертикальное положение относительно друг друга, оставаясь в той же плоскости.
- хорошая управляемость
- хорошая устойчивость автомобиля
- большая комфортабельность
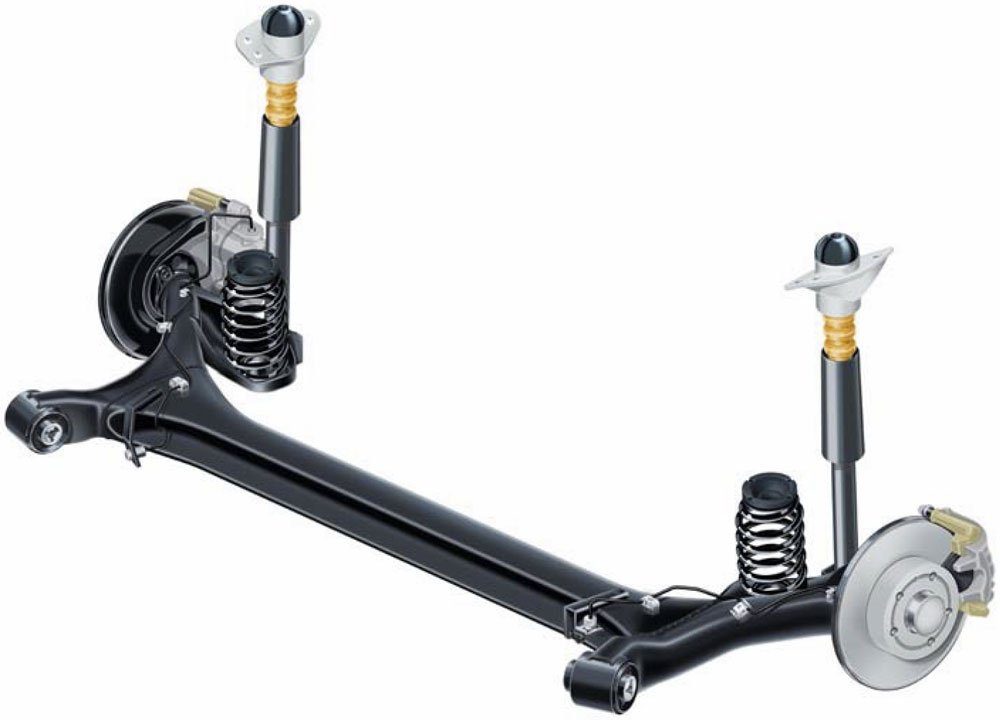
Полузависимая подвеска или торсионная балка — это промежуточное решение между зависимой и независимой подвеской. Колеса по прежнему остаются связанными, однако существует возможность их небольшого перемещения относительно друг друга. Данное свойство обеспечивается за счет упругих свойств П-образной балки, соединяющей колеса. Такая подвеска в основном применяется в качестве задней подвески бюджетных автомобилей.
Виды независимых подвесок
МакФерсон
— самая распространенная подвеска передней оси современных автомобилей. Нижний рычаг соединен со ступицей посредством шаровой опоры. В зависимости от его конфигурации может применяться продольная реактивная тяга. К ступичному узлу крепится амортизационная стойка с пружиной, ее верхняя опора закрепляется на кузове.
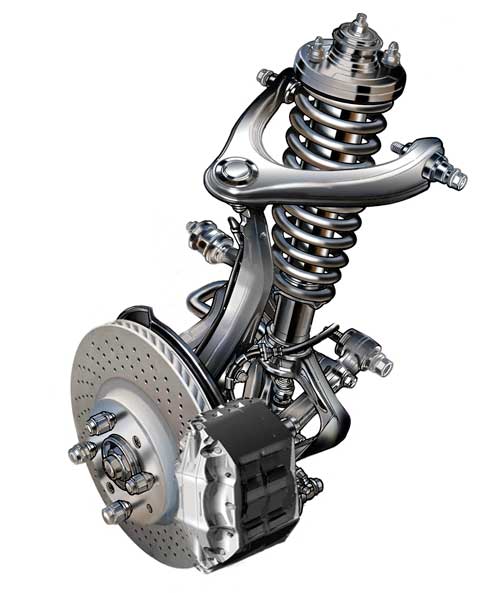
Поперечная тяга, закрепленная на кузове и соединяющая оба рычага, является стабилизатором, противодействует крену автомобиля. Нижнее шаровое соединение и подшипник чашки стойки-амортизатора дают возможность для поворота колеса.
Детали задней подвески выполнены по тому же принципу, отличие заключается лишь в отсутствии возможности поворота колес. Нижний рычаг заменен на продольные и поперечные тяги, фиксирующие ступицу.
- простота конструкции
- компактность
- надежность
- недорогая в производстве и ремонте
- средняя управляемость
Двухрычажная передняя подвеска
Более эффективная и сложная конструкция. Верхней точкой крепления ступицы выступает второй поперечный рычаг. В качестве упругого элемента может использоваться пружина или торсион. Задняя подвеска имеет аналогичное строение. Подобная схема подвески обеспечивает лучшую управляемость автомобиля.
Пневматическая подвеска
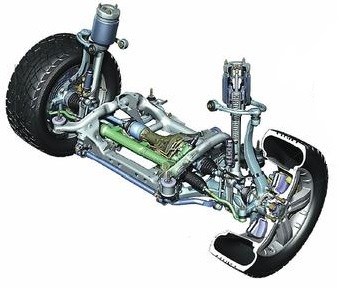
Роль пружин в этой подвеске выполняют пневмобаллоны со сжатым воздухом. При пневматической подвеске есть возможность регулировки высоты кузова. Также она улучшает показатели плавности хода. Используется на автомобилях класса люкс.
Гидравлическая подвеска
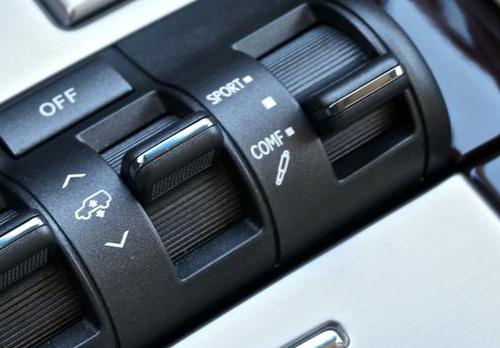
Амортизаторы подключены к единому замкнутому контуру с гидравлической жидкостью. Гидравлическая подвеска дает возможность регулировать жесткость и высоту дорожного просвета. При наличии в автомобиле управляющей электроники, а также функции адаптивной подвески она самостоятельно подстраивается под условия дороги и вождения.
Спортивные независимые подвески
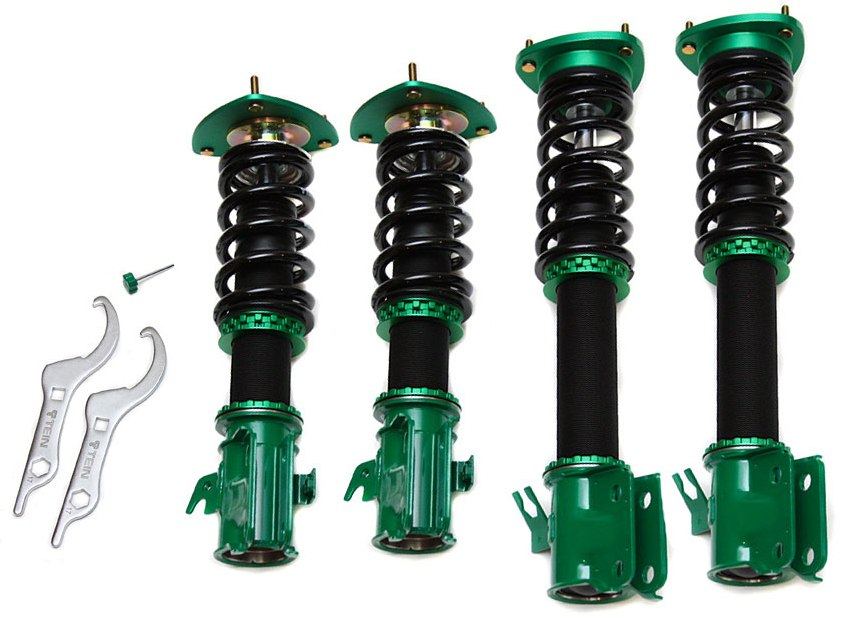
Винтовая подвеска, или койловеры – амортизационные стойки с возможностью настройки жесткости прямо на автомобиле. Благодаря резьбовому соединению нижнего упора пружины можно регулировать ее высоту, а также величину дорожного просвета.
Подвески типа push-rod и pull-rod
Данные устройства разрабатывались для гоночных автомобилей с открытыми колесами. В основе — двухрычажная схема. Основная особенность заключается в том, что демпфирующие элементы расположены внутри кузова. Конструкция данных типов подвески очень схожа, отличие заключается лишь в расположении воспринимающих нагрузку элементов.
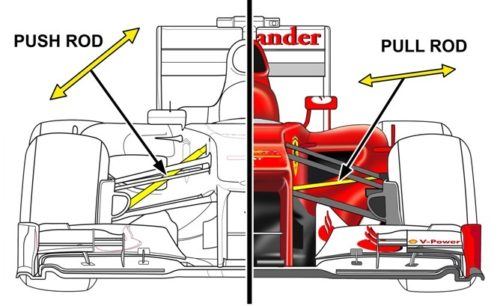
Спортивная подвеска push-rod: воспринимающий нагрузку элемент – толкатель, работает на сжатие.
Спортивная подвеска pull-rod: воспринимающий нагрузку элемент работает на растяжение.
Такая конструкция снижает центр тяжести и обеспечивает лучшую устойчивость автомобиля. Подвеска pull-rod имеет более низкий центр тяжести, чем push-rod. Однако на практике их общая эффективность примерно одинакова.
Подвеска колес появилась значительно раньше автомобиля. Впервые она появилась еще на конных экипажах, предназначенных для более комфортного передвижения на большие расстояния. Количество колес таких экипажей было не менее четырех, поэтому их конструкторы вынуждены были предусмотреть возможность вертикального перемещения колес относительно кузова для преодоления неровных дорог.
Именно тогда появились первые конструкции подвесок, которые потом практически без изменений использовались в самых первых автомобилях, скорость которых не превышала 30 км/час. Но автомобили совершенствовались, скорости их движения быстро возрастали, и подход к конструкциям подвесок менялся.
Если на начальном этапе автомобилестроения подвеска рассматривалась только в качестве средства повышения комфортабельности движения, то с ростом скорости автомобилей всѐ большее внимание приходилось уделять вопросам управляемости. В третьем десятилетии 20 века проявилась тенденция создания независимой системы сначала передних, а впоследствии и задних колес автомобилей.
В настоящее время на легковых автомобилях применяется только независимая подвеска передних колес, которая может сочетаться с независимой, полунезависимой и зависимой системой задних. Несмотря на обилие применяемых в настоящее время схем, все они в настоящее время содержат следующие основные элементы:
- Направляющие элементы, обеспечивающие заданную траекторию перемещения колес относительно кузова;
- Упругие элементы, обеспечивающие необходимое усилие перемещения колес;
- Элементы, обеспечивающие гашение колебаний.
К направляющим элементам можно отнести рычаги, стойки, шаровые опоры и резинометаллические шарниры.
К упругим элементам можно отнести пружины, рессоры, торсионы и пневматические камеры.
К элементам, гасящим колебания можно отнести амортизаторы всех типов.
Изложенная выше классификация элементов в значительной мере условна, так как в разных типах подвесок некоторые детали могут совмещать несколько функций.
В качестве примера можно рассмотреть рессору, которая применялась ещё в каретах. Рессора может выполнять роль сразу всех трех основных элементов, так как взаимное трение ее листов позволяет достичь эффекта гашения колебаний, а участки рессор несимметричной формы можно использовать в качестве рычагов.
Именно этими свойствами рессор и объясняется их широкое распространение. Тем не менее, такое разделение основных элементов позволяет лучше понять зависимость изменения ее характеристик от замены какого-либо из вышеперечисленных элементов. То есть положение колес зависит от направляющих элементов, жесткость устройства подвески зависит от упругих элементов, а эффективность гашения колебаний – от амортизаторов.
Наиболее распространенные конструкции и устройство передней подвески
В настоящее время на легковых автомобилях малого и среднего классов наиболее распространенной является устройство типа Мак – Ферсон.
Устройство переднего узла такого типа показана на рисунке.
Главная особенность подвесок этого типа – совместное использование нижнего рычага и телескопической вертикальной стойки. В этой системе основная нагрузка от веса автомобиля передается на кузов в месте верхнего крепления телескопической стойки, так как упругий элемент (на рисунке пружина) располагается непосредственно на стойке.
Нижний рычаг треугольной формы контролирует траекторию перемещения колеса и передает на силовые элементы кузова продольные и поперечные усилия, возникающие при движении автомобиля. Такая система очень хорошо сочетается с приводом передних колес, так как ось вращения колеса проходит выше нижнего ее рычага.
Преимущества узла типа Мак – Ферсон следующие:
- Простота конструкции, позволяющая уменьшить количество деталей и их массу;
- Возможность увеличения ширины моторного отсека;
- Относительно малая трудоемкость обслуживания и ремонта.
Однако такой узел не лишен недостатков:
- Характер изменения угла развала при работе не оптимальный;
- Значительное изменение углов установки колес при изменении загрузки автомобиля;
- Верхняя точка крепления стоек ограничивает возможность понижения линии капота.
В автомобилях, на которых устанавливается такая передняя подвеска, чаще всего используют пружины в качестве упругих элементов. Амортизатор телескопического типа конструктивно выполняет дополнительно функцию направляющего элемента, поэтому штоки амортизаторов Мак – Ферсон имеют увеличенный диаметр.
Для компенсации изгибающих усилий, действующих на амортизатор, пружину на нем часто устанавливают под углом к оси штока (см. рисунок). Для уменьшения крена автомобиля при прохождении поворота предусматривается стабилизатор поперечной устойчивости. Чаще всего применяют стабилизатор торсионного типа из изогнутого стального прутка круглого сечения. Загнутые концы стабилизатора шарнирно соединяют с рычагами или стойками левого и правого колес.
Промежуточные опоры стабилизатора закрепляют на кузове или специальном подрамнике. При крене автомобиля балка стабилизатора работает на скручивание и перераспределяет часть усилия с наиболее нагруженного колеса на менее нагруженное, уменьшая таким образом крен автомобиля.
Соединение нижнего рычага с поворотным кулаком осуществляется через шаровую опору. Такое соединение позволяет не только изменять угол между поворотным кулаком и рычагом, но и поворачивать колесо при изменении направления движения.
Устройство шаровой опоры показано на рисунке:
Для того чтобы облегчить усилие поворота передних колес, в верхней опоре стойки применяют специальный опорный подшипник. Наиболее часто применяют упорный шарикоподшипник.
Для того чтобы стойка в процессе работы имела свободное угловое перемещение, опора содержит либо эластичный резиновый элемент, либо специальный шарнир. Схема устройства верхней опоры и действующих на нее сил показана на рисунке.
Под воздействием ударных знакопеременных нагрузок на подшипник может происходить усталостное разрушение деталей подшипника, что приводит к нарушению его работы.
Внешними признаками неисправности подшипника являются посторонние звуки при повороте колес под нагрузкой. В этом случае подшипник необходимо заменить. Кроме того, в процессе эксплуатации автомобиля может произойти разрушение резиновых элементов опоры.
Описание товара
Рычажные механизмы, часть 6 Рычаги и коромысла
В кривошипно-шатунных механизмах в качестве выходного звена, или в качестве промежуточного звена применяются рычаги, коромысла или кулисы, которые в отличие от ползуна движущегося поступательно, совершают качательное движение относительно оси соединяющей их со станиной. Однако при выполнении одинакового вида движения рычаги, коромысла и кулисы могут иметь совершенно различную конструкцию, которая зависит, прежде всего, от назначения и области применения, а точнее области техники в которой используется рычажный или кривошипно-шатунный механизм, в состав которого входят эти звенья.
Рычаг – это звено рычажного механизма, которое будучи шарнирно установлено на неподвижно закрепленной оси совершает относительно нее качательное движение, получая при этом привод чаще всего от шатуна или тяги, с которыми он также шарнирно соединен.
Коромысло – это одноплечий рычаг, установленный на неподвижной оси и получающий привод от шатуна или тяги.
Рычаги
Рычаги не менее часто, чем коленчатые валы, шатуны и ползуны используются в рычажных механизмах, поскольку позволяют не только обеспечивать выполнение механизмом его функционального назначения, будучи его выходным звеном, но помимо этого, будучи его промежуточным звеном, позволяют изменять величину и направление передаваемого движения, а в ряде случаев и переносить его в параллельную или перпендикулярную плоскость.
На Рис. 1 показана конструкция различных типов рычагов, которые наиболее часто применяются в машиностроении. На Рис. 1а показана конструкция двуплечего рычага, отверстия для соединения которого с ведущим и ведомым звеном находятся с одной стороны от оси его качания. На Рис. 1б показана конструкция двуплечего рычага, отверстия для соединения которого с ведущим и ведомым звеном находятся с различных сторон от оси его качания. На Рис. 1в показана конструкция двуплечего рычага, отверстия для соединения которого с ведущим и ведомым звеном расположены под углом друг к другу и находятся с различных сторон от оси его качания. На Рис. 1г показана конструкция трехплечего рычага, отверстия для соединения которого с ведущим и ведомым звеном расположены под углом друг к другу и находятся с различных сторон от оси его качания. На Рис. 1д показана конструкция двуплечего рычага отверстия для соединения которого с ведущим и ведомым звеном расположены под углом друг к другу и находятся с одной стороны от оси его качания, а ведущее и ведомое плечи выполнены в виде единого элемента. На Рис. 1е показана конструкция двуплечего рычага тяжело нагруженного рычажного механизма, у которого ведомые плечи, расположенные с противоположной стороны оси качания рычага по отношению к оси отверстия в ведомом плече, передают движение двум ведомым тягам. На Рис. 1ж показан двуплечий рычаг, в котором, расположенные под углом друг к другу ведущее и ведомое плечи выполнены с отверстиями, оси которых расположены перпендикулярно оси качания рычага. На Рис. 1и показана конструкция двуплечего рычага, имеющего сборную конструкцию и состоящего из ведущего и ведомого плеч выполненных в виде отдельных деталей жестко закрепленных на валу посредством клеммных соединений затягиваемых болтами, при этом наличие вала, обеспечивающего осевое смещение плеч рычага, позволяет рычагу передавать движение в параллельных плоскостях. На Рис. 1к показана конструкция двуплечего рычага, имеющего аналогичное назначение с предыдущим примером (смещение передаваемого движения в параллельную плоскость), но выполненного в литом варианте и имеющего удлиненную центральную ступицу в отверстии которой располагаются подшипники качения на которых рычаг устанавливается на оси, закрепленной на станине.
Рис. 1. Конструкция рычагов наиболее
часто применяемых в машиностроении.
Рычаги, показанные на Рис. 1а –1ж выполненные методом сварки, применяются обычно в единичном и мелкосерийном производстве. В крупносерийном и массовом производстве рычаги выполняются методом штамповки или литья. На Рис. 2 показана конструкция литых рычагов. На Рис. 2а литой рычаг, применяемый в автомате перекоса лопастей вертолета, а на Рис. 2б литой рычаг, применяемый в подвеске легкового автомобиля.
Рис. 2. Конструкция литых рычагов
В ряде случаев рычаги используются как промежуточное звено, позволяющее передать движение со смещением в параллельную плоскость. На Рис. 3а показана конструкция рычага, в которой для этой цели ведущее и ведомое плечи параллельны друг другу и смещены на определенное расстояние. В данном случае рычаг 1 на подшипниках скольжения 2 шарнирно установлен на оси 3, закрепленной на корпусной детали 4, при этом оси 5 и 6 расположенные в отверстиях ведущего и ведомого плеч рычага соединяют его с соответствующими звеньями рычажного механизма, в который входит рычаг. Для точного расположения рычага 1 на оси 3 установлены регулировочные кольца 7, а стопорение рычага на оси осуществляется стопорным кольцом 8.
Рис. 3. Конструкция рычагов, плечи которых параллельны друг
другу и смещены на определенное расстояние.
На Рис. 3б показана конструкция сборного рычага состоящего из ведущего 1 и ведомого 2 плеч, которые жестко закреплены на валике 3 посредством клеммных соединений. Валик 3 на подшипниках скольжения 4 установлен в отверстии кронштейна 5, закрепленного на станине 11 технологического оборудования, Ведущее плечо 1 рычага посредством оси 6 шарнирно соединено с ведущей тягой 8, а ведомое плечо 2 рычага посредством оси 7 шарнирно соединено с ведомым звеном 9 рычажного механизма. Положение валика 3 относительно кронштейна 5 обеспечивается регулировочными кольцами 10.
Рис. 4. Конструкция сборных рычагов.
В оборудовании автоматического действия рычажные механизмы зачастую используются совместно с элементами зубчатых передач и кулачковыми механизмами, при этом в их состав могут входить сборные рычаги. На Рис. 4 показаны варианты конструкции таких рычагов. На Рис. 4а показана конструкция сборного рычага состоящего из непосредственно рычага и закрепленного на нем зубчатого сектора. На Рис. 4б показана конструкция сборного рычага состоящего из рычага и закрепленного на нем плоского кулачка. В обоих случаях для надежной и точной фиксации и зубчатого сектора и кулачка в рычаге предусмотрены соответствующие центрирующие и базирующие поверхности.
Рис. 5. Конструкция рычагов применяемых в приспособлениях для механической обработки.
Рычаги различной конструкции широко применяются в приспособлениях для механической обработки. На Рис. 5 показаны варианты стандартизированных конструкций рычагов применяемых в приспособлениях для механической обработки:
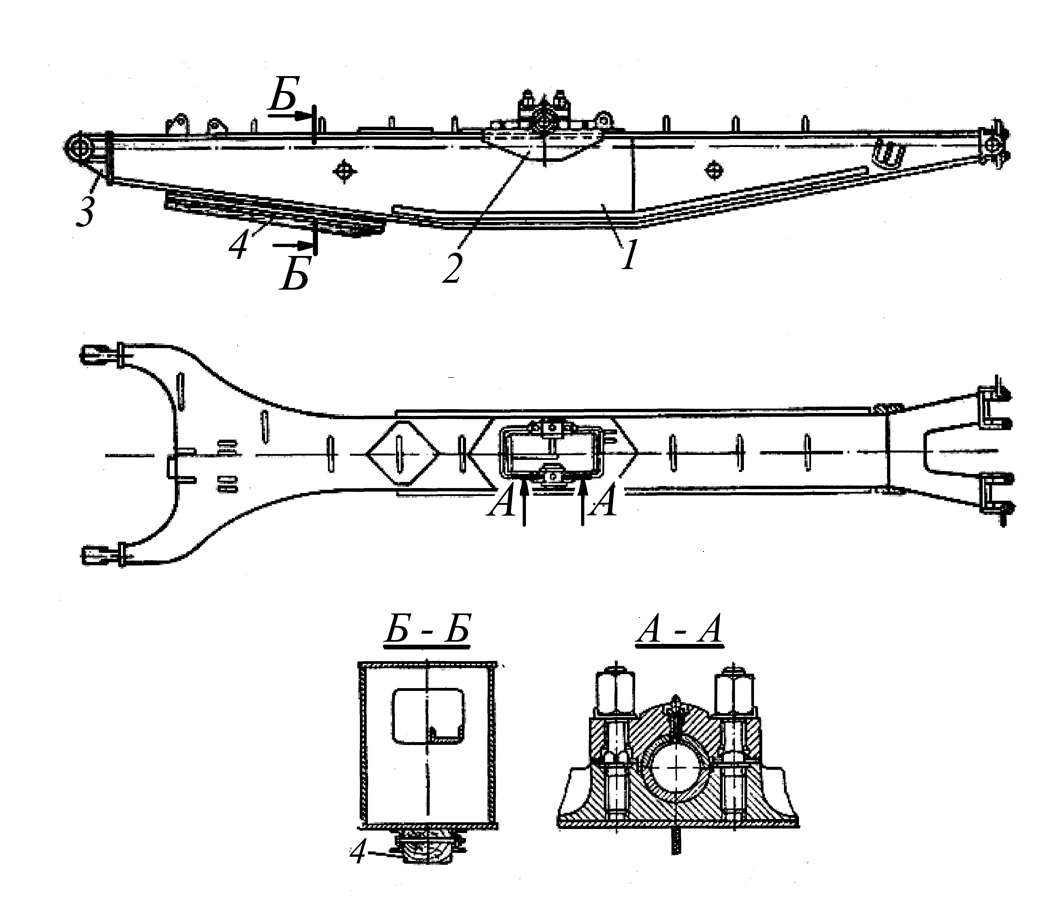
Рычажные механизмы широко применяются в строительной и дорожной технике (кранах, экскаваторах, бульдозерах), в этом случае, рычаги входящие в их состав имеют габаритные размеры от нескольких метров до десятков метров и поэтому изготавливаются методом сварки. На Рис. 6 показана конструкция сварной стрелы экскаватора которая состоит из балки 1, кронштейна 2 для установки вала седлового подшипника, амортизатора 3 и пяты 4.
Рис. 7. Конструкции резинометаллических
шарнирных соединений.
В шарнирных соединениях рычагов с шатунами и тягами используются подшипники скольжения и качения, игольчатые подшипники, оригинальные и стандартные шаровые соединения, конструкции которых рассмотрены в статье «Шарнирные соединения». В ряде случаев шарнирные соединения рычагов с шатуном или тягой испытывают не только поперечные усилия, но и работают на кручение, что имеет место, например в шарнирных соединениях рычагов с тягами в подвеске автомобиля. В этих случаях используются резинометаллические шарниры (см. Рис. 7).
Рис. 8. Варианты крепления рычагов на валу.
Важным элементом, в значительной мере определяющим не только ресурс работы рычажного механизма, но зачастую и его работоспособность является соединение рычага с валом, передающим ему крутящий момент. Это соединение должно обеспечивать исключение зазора, преждевременного износа или смятия контактирующих поверхностей в процессе эксплуатации, а также простоту и удобство его разборки и сборки. Примеры таких соединений показаны на Рис. 8. На Рис. 8а показано крепление рычага на валу, в котором крутящий момент передается посредством торцевой шпонки совмещенной с шайбой. Это крепление применяется в рычажных механизмах, работающих с небольшими скоростями и знакопеременными нагрузками. При этом торцевую шпонку обычно изготавливают из стали 45 и подвергают закалке до твердости HRC 35- 40 ед., устанавливают ее на вал и рычаг по посадке H11/d11. Соединение просто в изготовлении и надежно при эксплуатации. На Рис. 8б показано клеммное соединение вала с рычагом, в котором передача крутящего момента осуществляется за счет сил трения между наружной поверхностью вала и отверстием рычага, создаваемых при его затяжке стяжным болтом. Для лучшего обжима вала в рычаге профрезерован центральный паз. Соединение, как и предыдущее, применяется в механизмах работающих с небольшими скоростями и знакопеременными нагрузками. На Рис. 8в показано соединение, в котором клеммный зажим вала совмещен с его фиксацией посредством болта, средний участок которого выполнен более точным, чем в обычном случае и плотно прижат к ответной поверхности открытого цилиндрического паза выполненного на валу. Такой болт изготавливается из стали 45 и калится до твердости HRC 35 – 40 ед, а посадка его среднего участка на вал выполняется по H11/d11. Соединение может использоваться для передачи значительных крутящих моментов. Для передачи средних по величине моментов и возможности осуществления небольшой угловой регулировки положения рычага относительно вала применяется соединение, показанное на Рис. 8д . В нем передача крутящего момента осуществляется посредством сил трения между валом и рычагом, которые создаются за счет затяжки двух регулировочных болтов и упора этих болтов в лыски вала. В такой конструкции соединения стержневая часть болта, контактирующая с валом также подвергаются закалке до твердости HRC 35–40 ед. На Рис. 8г показано соединение, в котором передача крутящего момента от вала к рычагу осуществляется посредством клиновой оси, фиксирующей рычаг за счет контакта с ответной лыской выполненной на валу. Это соединение применяется в рычажных механизмах, работающих с большими скоростями и нагрузками. В рычажных механизмах, работающих в условиях знакопеременных динамических нагрузок со значительными скоростями их соединение с валом выполняется с использованием эвольвентного шлицевого соединения с центрированием по боковой поверхности, которое показано на Рис. 8е . Внутренние шлицы в рычаге выполняются методом протягивания, поэтому при индивидуальном или мелкосерийном производстве таких соединений рычагов с валом применение эвольвентных шлицов может быть экономически не оправдано.
Для выполнения специфических требований, предъявляемых к рычажным механизмам, в состав которых входят рычаги и зависящих главным образом от области техники, в которой они используются, причем, независимо от того, являются они выходным или промежуточным звеном, в них могут встраиваться различные дополнительные устройства позволяющие:
- предохранять механизм от перегрузок,
- регулировать длину плеч рычага,
- регулировать угловое положение рычага.
Рассмотрим несколько примеров таких устройств, встраиваемых в рычаги.
Рис. 9. Конструкция предохранительного
устройства встроенного в рычаг легко
нагруженного механизма.
На Рис. 9 показана конструкция предохранительного устройства встроенного в рычаг легко нагруженного механизма, которое обеспечивает прекращение передачи движения рычагом при приложении к его ведомой части усилия больше допустимого. Оно содержит вал 6, на котором шарнирно установлен рычаг 7, также шарнирно соединенный с шатуном 8, рычаг 5 жестко закрепленный на валу 6 посредством шпоночного и клеммного соединений, при этом рычаг 5 шарнирно соединен с защелкой 3, постоянно поджатой пружиной растяжения 1, к пластине 2, закрепленной на рычаге 7. Контакт защелки 3 с пластиной 2 осуществляется посредством зуба входящего в соответствующую впадину. Если на шатун 8 действует повышенное усилие, пружина 1 растягивается и зуб защелки 3 выходит из впадины пластины 2 и движение от рычага 5 рычагу 7 не передается, при этом рычаг 5, будучи закрепленным на валу, продолжает совершать качательное движение. После прекращения действия повышенного усилия зуб защелки 3 опять свободно входит в паз пластины 2 и рычаг 7 начинает двигаться с рычагом 5 как единое целое, передавая при этом движение шатуну 8.
Рис. 10. Предохранитель по усилию встроенный в рычаг кулачкового механизма.
На Рис. 10 показана конструкция предохранительного устройства встроенная в сборный двуплечий рычаг являющийся толкателем кулачкового механизма. Оно содержит закрепленный на валу 1 сборный двуплечий рычаг, состоящий из коромысла 3 с роликом 9 контактирующим с кулачком 10 и двуплечего рычага 2, ведущее плечо которого имеет выступ 4 прижимаемый пружиной 5 к упору 6 коромысла 3, а ведомое плечо 15 рычага 2 шарнирно соединено с корпусом 16 закрепленным на ведомой штанге 17. На рычаге 2 микропереключатель 13 контактирующий с переключающим рычагом 12, а также упор 14 имеющий возможность взаимодействия с переключающим рычагом 12. Ролик 9 коромысла 3 постоянно поджат к кулачку 10 посредством пружины (на Рис. 193 не показана), а взаимодействие коромысла 3 с двуплечим рычагом 2, при повороте коромысла по часовой стрелке, осуществляется посредством планки 11.
Работает устройство следующим образом. При нормальной работе механизма (при отсутствии перегрузок) кулачок 10 через ролик 9 передает качательное движение коромыслу 3, которое контактируя своим упором 6 с выступом 4 двуплечего рычага 2, сообщает последнему качательное движение, а его ведомое плечо 15 взаимодействуя с корпусом 16 закрепленным на штанге 17 сообщает ей поступательное движение (штанга совершает рабочий ход). При качании коромысла 2 по часовой стрелке движение рычага 3 передается посредством планки 11 и ведомое плечо 15 рычага 2 сообщает штанге 17 движение в об-ратном направлении (штанга совершает холостой ход), взаимодействуя с ней посредством корпуса 16. При таком взаимном расположении коромысла 3 и ведущего плеча рычага 2 упор 14 воздействует на рычаг переключения 12, который в свою очередь замыкает микропереключатель 13. При увеличении нагрузки, приложенной к штанге 17 выше допустимой, при совершении ею рабочего хода, последняя останавливается вместе с корпусом 16 и двуплечим рычагом 2, а кулачок 10, продолжая вращение в том же направлении, воздействует на ролик 9, и коромысло 3, преодолевая усилие пружины 5 поворачивается против часовой стрелки. В результате этого упор 14 освобождает рычаг переключения 12 и последний выключает микропереключатель 13, который при этом через систему электроавтоматики останавливает привод станка.
Рис. 11. Конструкция сборного рычага, в состав которого введено устройство для компенсации динамических нагрузок.
На Рис. 11 показана конструкция сборного рычага, в состав которого введено устройство для компенсации динамических нагрузок, действующих в направлении противоположном действию технологического усилия передаваемого рычажным механизмом. Этот рычаг содержит ведущее 1 и ведомое 2 плечи, соединенные между собою втулкой скольжения 3, причем ведущее плечо 1 закреплено на втулке неподвижно, а ведомое плечо 2 – с возможностью поворота на ней. Между торцами ступиц плеч 1 и 2 установлены анти- фрикционные кольца 4. Контакт плеч 1 и 2 осуществляется по опорным поверхностям 5 и 6. На поверхностях плеч 1 и 2 рычага выполнены приливы 7 и 8, в отверстиях которых установлена шпилька 9, стягивающая приливы посредством гаек 11 через упругую вставку 10 выполненную в виде втулки.
При работе механизма, в состав которого входит сборный рычаг, технологическое усилие от ведущего плеча 1 ведомому плечу 2 передается через опорные поверхности 5 и 6. При возникновении в процессе работы механизма динамических нагрузок в направлении противоположном действию технологического усилия, ведомое плечо 2 начинает отрываться своей поверхностью 6 от опорной поверхности 5 ведущего рычага 1 и при этом поворачивается против часовой стрелки относительно ведущего плеча 1. В результате этого упругая вставка 10 закрепленная между приливами 7 и 8 сжимается и компенсирует действие на механизм динамической нагрузки, а также эффективно гасит возникающие при этом колебания деталей механизма.
Рис. 12. Конструкция сборного рычага, в состав которого введен торсионный валик
для компенсации динамических нагрузок.
На Рис. 12 показана конструкция сборного рычага, в состав которого введен торсионный валик для компенсации динамических нагрузок, действующих в направлении противоположном действию технологического усилия передаваемого рычажным ме-ханизмом. Этот рычаг состоит из ведущего плеча 1, которое жестко соединено со втулкой 4, шарнирно установленной в опорах 2 и контактирующей с двумя ведомыми плечами 3 рычага, расположенными на ее торцах и соединенными с нею посредством торсионного валика 5, расположенного внутри втулки. При этом ведомые плечи 3 рычага через антифрикционные прокладки 6 поджаты к торцам втулки 4 посредством шпилек 7 и гаек 8. Оба ведомых плеча 3 сборного рычага выполнены с цапфами, которые входят в отверстие втулки 4, при этом цапфы имеют радиусные выступы, а в отверстии втулки 4 выполнены ответные радиусные пазы, образующие с торцами радиусных выступов зазоры. При сборке рычага в составе механизма торсионный валик 5 предварительно закручивают таким образом, чтобы зазор между торцами радиусных выступов цапф ведомых плеч 3 и торцами ответных радиусных пазов втулки 4 выбирался при их контакте во время передачи рычагом технологического усилия.
При работе механизма в который входит сборный рычаг технологическое усилие от ведущего плеча 1 через втулку 4 и торцы ее радиусных пазов передается торцам радиусных выступов на цапфах ведомых плеч 3 и последние совершают качательное движение передавая его выходному звену механизма. При возникновении динамической нагрузки действующей в направлении противоположном действию технологического усилия, ведомые плечи 3 начинают вращаться в противоположную сторону и дополнительно закручивают торсионный валик 5, упругая деформация которого снижает действие инерционных нагрузок на детали механизма.
Рис. 13. Конструкция сборного рычага тяжело нагруженного механизма со встроенным предохранителем по усилию.
Рассмотренные предохранители по усилию встраиваемые в рычаги относятся к типу восстанавливаемых, что делает их использование достаточно эффективным, но к сожалению их применение оказывается невозможным в тяжело нагруженных рычажных механизмах. В рычаги тяжело нагруженных механизмов встраиваются разрушаемые предохранители по усилию. Показанный на Рис. 13 сборный рычаг со встроенным предохранителем по усилию содержит ведущее плечо 1, шарнирно установленное посредством втулки скольжения 2 на оси 3 жестко закрепленной на станине 4, при этом ведомое плечо 6 рычага посредством втулки скольжения также шарнирно установленной на той же оси 3. Соединены оба рычага с помощью срезного штифта 10, установленного во втулки 7, 8 и 9 запрессованные в отверстие ведущего рычага 1 и отверстие ведомого рычага 6. Если усилие передаваемое сборным рычагом превышает допустимую величину, то штифт 10 срезается и связь ведомого плеча 1 с ведущим плечом 6 рычага прекращается и это предотвращает поломку более сложных и дорогостоящих деталей механизма.
Рис. 14. Устройство, встроенное в рычаг малонагруженного рычажного механизма, позволяющее регулировать длину его ведущего плеча.
На Рис. 14 показано устройство, встроенное в рычаг малонагруженного рычажного механизма, позволяющее регулировать длину его ведущего плеча. В этот рычаг, состоящий из ведущего 1 и ведомого 2 плеч и установленный на оси 3, встроен палец 6, шарнирно посредством оси 5 соединенный с ведущей тягой 4 и фиксируемый в требуемом положении в пазу 10 с помощью гайки 9, а в его резьбовое отверстие пропущен регулировочный винт 7. При этом, ведомое плечо 2 рычага шарнирно посредством оси 8 соединено с ведомым звеном рычажного механизма. При выполнении регулировки длины ведущего плеча 1 рычага производится раскручивание гайки 9, затем перемещение в ту или другую сторону пальца 6 по пазу ведущего плеча 1 рычага регулировочным винтом 7 и после этого выполняется последующее стопорение пальца 6 гайкой 9.
Рис. 15. Конструкция устройства встроенного в рычаг тяжело нагруженного рычажного механизма, позволяющее регулировать
длину его ведомого плеча.
На Рис. 15 показана конструкция устройства встроенного в рычаг тяжело нагруженного рычажного механизма, позволяющее регулировать длину его ведомого плеча. В этот рычаг, состоящий из ведущего 1 и ведомого 2 плеч и шарнирно соединенный посредством оси 4 с ведущей тягой и установленный на оси 3, встроена ось 7, расположенная в окне его ведомого плеча, которая соединяет плечо 2 с ведомой тягой 6. При этом ось рычага 3 жестко закреплена в станине 12. Ось 7 в своей центральной части имеет призматическую форму и расположена в пазу ведомого плеча 2 рычага, что дает ей возможность перемещения, которое обеспечивает изменение ее расстояния от оси 3. Такая конструкция оси 7, перемещение которой в пазу ведомого плеча 2 рычага осуществляется посредством шпильки 8 и резьбовой втулки 9, а фиксация в требуемом положении – посредством болтов 10 и гайки 11, позволяет менять длину ведомого плеча 2 рычага, что бывает необходимо при настройке хода выходного звена рычажного механизма, в который входит рычаг.
Рис 16 Конструкция механизма регулировки длины плеча рычага, при выполнении которой его угловое положение не меняется.
Недостатком конструкции устройств для регулировки длины плеча рычага является то, что при выполнении регулировки меняется угловое положение рычага относительно оси качания, что в ряде случаев недопустимо. На Рис 16 показана конструкция механизма регулировки длины плеча рычага, при выполнении которой его угловое положение не меняется. Этот механизм содержит кривошипный вал 1, на мотылевой шейке которого установлен шатун 2, который посредствам пальца – ползушки 3 шарнирно соединен с промежуточным двуплечим рычагом 5, который с помощью оси 6 шарнирно установлен на станине (на Рис 16 не показана) а его ведомое плечо посредствам оси 7 соединено с ведомой тягой 8. При этом на рычаге 5 шарнирно установлен палец 9, в отверстии которого установлен и зафиксирован в осевом направлении ходовой винт 10, а его резьбовой конец взаимодействует с резьбовым отверстием в пальце 3, который расположен с возможностью перемещения в радиусном пазу 4 рычага 5 и фиксируется в нем аналогично тому, как показано на Рис 197. Регулировка длины ведущего плеча двуплечего рычага 5 осуществляется путем вращении ходового винта 10, в результате чего палец 3 перемещается в радиусном пазу 4, при этом радиусная форма этого паза обеспечивает неизменное положение рычага 5 при выполнении регулировки.
Рис 17 Конструкция устройства для регулировки углового положения рычага относительно его оси качания.
В ряде исполнительных и вспомогательных механизмов технологического оборудования возникает необходимость регулировать исходное положение выходного звена, что может быть обеспечено путем регулировки углового положения рычага независимо от того является он выходным или промежуточным звеном механизма. На Рис 17 показана конструкция устройства для регулировки углового положения рычага относительно его оси качания Он содержит ведущую тягу 1, которая посредствам оси 2 шарнирно соединена с ведущим коромыслом 3, которое также как и ведомый двуплечий рычаг 4, шарнирно установлена на пальце 5, закрепленном на кронштейне 6. При этом коромысло 3 и двуплечий рычаг 4 жестко соединены между собою посредствам болта 7, установленного на рычаге 4 с помощью комплекта сферических шайб 8 и упорного винта 9, осевое положение которого в рычаге 4 фиксируется гайкой 10. Такое соединение рычага 4 и кулисы 3, при неизменное положении последней, позволяет менять угловое положение рыча-
га 4, которое осуществляется путем вкручивания и выкручивания болта 7 и винта 9.
Однако такая регулировка позволяет регулировать положение рычага в узком диапазоне. Большую величину регулировки углового положения рычага можно обеспечить регулировкой длины ведущей тяги, которая осуществляется известными методами.
Коромысла
Коромысла, как уже говорилось, являются одной из разновидностей рычагов, и также широко используются в рычажных механизмах. Они применяются в тех случаях, когда, не меняя направление движения, нужно изменить его величину, или получить более сложный закон движения ведущего звена рычажного механизма. На Рис. 18 показано несколько вариантов использования коромысел в составе рычажных механизмов. На Рис. 18а показана кинематическая схема рычажного механизма, коромысло которого шарнирно соединяет ведущий шатун с ведомым шатуном, увеличивая при этом ход ползуна. На Рис. 18б, в, г показана кинематическая схема рычажного механизма содержащего промежуточное и ведомое коромысла, при этом наличие промежуточного коромысла позволяет получить тре-буемый закон движения ведомого коромысла. На Рис. 18б, в оба коромысла шарнирно соединены с ведомым шатуном рычажного механизма, а на Рис. 18г промежуточное коромысло соединено с ведущим и ведомым шатуном одновременно, а ведомое коромысло соединено с ведомым шатуном.
.
Рис. 18. Кинематические схемы рычажных механизмов, содержащих
коромысла.
На Рис. 19 показана конструкция домкрата выполненного на основе рычажного механизма содержащего в виде основного опорного элемента – коромысло. Он содержит опорный башмак 1, который посредством оси 2 шарнирно соединен с опорным коромыслом 3, а последнее, посредством оси 5 шарнирно соединена с шатуном 4, который посредством оси 8 шарнирно соединен с шатуном 9. Кроме того опорное коромысло 3 посредством оси 7 шарнирно соединено с шатуном 6, а последний, в свою очередь, посредством оси 10 соединен с шатуном 9, а посредством оси 11 с верхним опорным башмаком 12 домкрата. При этом оси 7 и 8 соединены ходовым винтом 14 с рукояткой 15, который контактирует с осью 8 посредством резьбового соединения, а с осью 7 посредством гладкого отверстия и бурта 13. При этом шарнирные соединения коромысла 3 и шатунов 4, 6 и 9 между собою образуют механизм параллелограмма, что в совокупности с соединением осей 7 и 8 посредствам ходового винта 14 позволяет получить выигрыш в усилие и обеспечивает параллельное движение башмака 12 при его подъеме и опускании.
Работает домкрат следующим образом. Вращение рукоятки 15 вместе с ходовым винтом 14 по часовой стрелке приводит к схождению осей 7 и 8 в горизонтальном направлении при этом коромысло 3 поворачиваясь против часовой стрелки, перемещает шатуны 9 и 10 таким образом, что верхний опорный башмак 12 поднимется вверх вместе с поднимаемым грузом. При вращении рукоятки 15 с ходовым винтом 14 в обратном направлении оси 7 и 8 расходятся в горизонтальном направлении, коромысло 3 поворачивается по часовой стрелке, а шатуны 9 и 10, двигаясь соответствующим образом, перемещают вниз опорный башмак 12 вместе с поднятым ранее грузом.
Рис. 19. Конструкция домкрата выполненного на основе
рычажного механизма.
При установке нескольких коромысел на одной оси, которая устанавливается на стойке, они могут жестко крепиться на ней, при этом сама ось может размещаться на станине по-средством подшипников. На Рис. 20 показана конструкция блока управления тормозами трактора, который выполнен на основе нескольких коромысел расположенных на общей оси, установленной посредством кронштейнов на станине. Блок управления рычагами трактора содержит ось 2, установленную посредствам шарнирных подшипников 9 в кронштейнах 1 закрепленных на неподвижном основании, на шлицевой поверхности которой жестко закреплены ведомые кулисы 3 и 4, а также зубчатый сектор 6 с собачкой 12, которая шарнирно соединена с ним, а также шарнирно установлена ведущая кулиса 5. Осевая фиксация деталей установленных на оси 2 осуществляется посредством стопорного кольца 7 и оригинальной гайки 14. Шаровые соединения 9, уплотнены с внутренней стороны манжетами 8, а с наружной стороны закрыты крышками 10, запрессованными в корпуса 1. Ведущая кулиса 5 и ведомая кулиса 4 соединена с соответствующими тягами управления посредством шарнирных подшипников 13.
Работает блок управления тормозами следующим образом. При повороте ведущей кулисы 5 по часовой стрелке, собачка 12 перемещаясь по дуге, своим заостренным концом захватывает определенное количество зубьев на зубчатом секторе 6, при этом ось 2 вместе с ведомыми коромыслами 3 и 4, а также зубчатым сектором 6 остаются неподвижными. При повороте ведущей кулисы 5 против часовой стрелки собачка упирается своим заостренным концом в соответствующий зуб сектора 6 и таким образом заставляет его вместе с осью 2 и ведомыми коромыслами 3 и 4 поворачиваться в том же направлении, в результате чего последние перемещают тяги управления тормозами (на Рис. 20 не показаны).
Рис. 20. Конструкция блока управления тормозами трактора, который выполнен
на основе нескольких коромысел расположенных на общей оси.
В состав коромысел, также как и в состав рычагов, могут входить устройства расширяющие возможности рычажных механизмов, в которые входят эти рычаги. Чаще всего это устройства, которые меняют плечо коромысла или его положение. На Рис. 21 показана конструкция коромысла с регулируемым расстоянием от оси шарнирного соединения до оси качания коромысла. Это коромысло 1 выполнено с поперечными шлицами в
с шагом Т
и продольным пазом а
, в котором установлен палец 4 с буртом б
и двумя резьбовыми концами, при этом на конце пальца пропущенным в продольный паз а
установлены промежуточная шайба 2, опорная шайба 3 и гайка 5. В промежуточной шайбе 2 выполнен продольный паз, длина которого L
определяется по следующей формуле: L = d + 2T/(T-t) t
Кроме того на промежуточной шайбе 2 со стороны ее контакта с коромыслом 1 выполнены шлицы г
с шагом Т
ответные шлицам на коромысле, а на противоположной поверхности промежуточной шайбы 2 выполнены шлицы д
с шагом t
, которые контактируют с ответными шлицами е
на опорной шайбе 3. В нижней части коромысла выполнено отверстие 6, в которое устанавливается соответствующая ось шарнирного соединения коромысла с неподвижной стойкой. Грубая регулировка расстояния R
от оси шарнирного соединения до оси качания коромысла производится путем смещения промежуточной шайбы 2 в продольном пазу а
коромысла, а тонкая регулировка – путем продольного смещения опорной шайбы 3 относительно промежуточной шайбы 2 за счет наличия в ней продольного паза. При этом величина регулировки определяется по следующей формуле:
𝜟R = n1T – n2 t;
Где:
– n1
, число зубьев, на которое смещается промежуточная шайба 2,
– n2
, число зубьев, на которое смещается опорная шайба 3.
Для удобства выполнения регулировки положения пальца 4 на коромысло 1 может наноситься шкала с соответствующими делениями.
Рис. 21. Конструкция коромысла с регулируемым расстоянием
от оси шарнирного соединения до оси качания коромысла.
В некоторых рычажных механизмах угловое положение коромысла регулируется поворотом оси его качания. На Рис. 22 показана конструкция оси качания коромысла, позволяющая регулировать его положение. Для регулирования положения коромысла, его ось качания 2, неподвижно установленная в отверстиях стойки 1, выполнена с эксцентриковой шейкой 3, на которой установлена эксцентриковая втулка 5 с наружной сферической поверхностью, контактирующей с ответной поверхностью коромысла 6. При этом на резьбовом конце оси 2 устанавливается шайба и гайка для ее осевой фиксации, а головка оси расположенная на ее противоположном конце выполнена в форме многогранника, каждая грань которого при определенном угловом положении оси 2 может контактировать с ответной поверхностью 7 выполненной в виде выступа на стойке 1. Для регулировки положения оси качания коромысла 6 осуществляют поворот оси 2 и эксцентриковой втулки 5, который может выполняться в одну и ту же или разные стороны.
Рис. 22. Конструкция оси качания коромысла, позволяющая
регулировать его положение.
На Рис. 23 показана конструкция устройства встроенного в коромысло, которое позволяет плавно регулировать его угловое положение относительно оси, на которой оно установлено. Это устройство, встроенное в коромысло 1, которое посредством оси 2 шарнирно соединено с ведущей тягой рычажного механизма, состоит из червячного колеса 3, расположенного в расточке коромысла и своими внутренними шлицами 4 контактирует со шлицевой поверхностью оси 14, а также зацепляется с червяком 5, установленном в расточке коромысла, выполненной перпендикулярно оси червячного колеса. При этом правая цапфа червяка 5 с шестигранным концом 6 в крышке 10 посредством комплекта роликов 9, контактирует с втулкой 8, на левом торце которой нанесены конические зубья 7, контактирующие с ответными зубьями, выполненными на червяке 5, образуя зацепление. Левый торец червяка 5 центральным конусным отверстием контактирует с ответной поверхностью упругой шайбы 12, которая поджата пружиной 11 и крышкой 13.
Регулировка углового положения коромысла 1 относительно оси 14 осуществляется следующим образом. Для поворота коромысла 1 в ту или другую сторону червяк 5 за шестигранную головку 6 вращается гаечным ключом в нужном направлении, при этом его вращение передается червячному колесу 3, которое будучи зафиксировано посредством шлицевого соединения на валу 14 остается неподвижным, а коромысло 1 совершает поворот в нужную сторону, меняя свое угловое положение относительно оси 14.
Рис. 23. Коромысло со встроенным устройством для регулировки его
углового положения.
ЛИТЕРАТУРА.
1. Игнатьев Н. П. Основы проектирования Азов 2011г.
2. Игнатьев Н. П. «Проектирование механизмов» Азов 2015г.
В статье использована информация из соответствующих разделов работы автора «Основы проектирования»
изданной в 2011г и работы автора «Проектирование механизмов»
, изданной в 2015г.
В спаравочно – методическом пособии «Проектирование механизмов»
помимо примеров конструкции рычагов и коромысел содержится:
– примеры конструкции и рекомендации по применению кулачковых механизмов, механизмов прерывистого действия и комбинированных механизмов,
– примеры конструктивного исполнения и рекомендации по применению основных типов деталей вышеперечисленных механизмов: коленвалов, шатунов, ползунов, кулачков и их шарнирных соединений,
– рекомендации по выбору типа привода механизма и примеры его выполнения,
– расчеты механизмов,
– пример построения циклограммы работы кулачкового автомата,
– методика проектирования механизмов,
– рекомендации по назначению требования по точности к механизмам и их типовым деталям,
– пример проектирования механизма
Для приобретения полной версии статьи добавьте её в корзину,
Стоимость полной версии статьи 50 рублей.
Рычаг – элемент независимой подвески автомобиля. Служит для обеспечения ограниченного движения в вертикальной плоскости колеса, которое он удерживает на месте, не позволяя ему откатиться в сторону.
Виды рычагов подвески
В зависимости от конструкции подвески рычаги делятся на типы по количеству точек крепления. Кроме того, их классифицируют и в зависимости от того, под каким углом они находятся к направлению движения автомобиля. По этому параметру рычаги делят на продольные и поперечные. Чаще всего встречаются рычаги А-образной конструкции (их также называют треугольными рычагами), прямые рычаги с двумя точками крепления и Н-образные рычаги, которые представляют собой 2 спаренных простых рычага, имеющих общую перемычку.Конструкция современного рычага подвески
Рычаг – литая продолговатая деталь из легкого сплава с ребрами жесткости, расположенными в продольном направлении, и с приливами на обоих концах. Один конец снабжен цилиндрическим приливом, в который вставлен, вернее, впрессован сайлентблок – деталь, служащая прокладкой при креплении рычага к кузову, раме или подрамнику. Второй конец снабжен кольцеобразным приливом, служащим местом крепления шаровой опоры. Конструкция рычага может варьироваться в зависимости от инженерного решения подвески. Например, прилива под шаровую опору может не быть, так как он выполнен на корпусе самой шаровой опоры, которая прикрепляется к рычагу при помощи болтов и гаек. Кроме того, в задней многорычажной подвеске нередко применяются рычаги с цилиндрическими приливами под сайлентблок на обоих концах.Пионерами отказа от стальных рычагов были компании Volkswagen и Subaru, начавшие активно использовать легкие сплавы в подвеске своих автомобилей еще в 90-е годы
В подвеске автомобилей, сделанных до начала 2000-х годов, как правило, применялись стальные рычаги. При этом они могут представлять собой либо полую коробчатую структуру (так называемую квадратную трубу), либо структуру с тремя стенками, две из которых служат ребрами жесткости (так называемый швеллер). В более современных конструкциях подвески наблюдается тенденция постепенного отказа от использования стали, с целью снижения как общего веса автомобиля, так и . Пионерами отказа от стальных рычагов в массовых моделях были компании Volkswagen и Subaru, начавшие активно использовать легкие сплавы в подвеске своих автомобилей еще в 90-е годы.
Назначение рычага подвески
Назначение рычагов подвески чаще всего зависит от места расположения. Рычаг может быть поперечным, продольным, верхним и нижним. В зависимости от расположения они выполняют разные функции.Основная особенность треугольного рычага в том, что он работает как в поперечном направлении, в котором он установлен, так и в продольном
Например, задача верхнего рычага передней подвески – удерживать верхнюю часть рулевого кулака, не позволяя прикрепленному к нему колесу завалиться вбок во время движения. Нижний рычаг также частично выполняет эту функцию, помогая верхнему, но при этом он еще и контролирует нижнюю часть , не позволяя ей раскачиваться. Продольные рычаги чаще всего применяются в конструкции задней многорычажной подвески и служат для удержания задних стоек в одном положении при разгоне и ускорении, когда на них воздействуют силы, направленные вдоль оси движения автомобиля.
Особенности конструкции треугольных рычагов
Конструкция треугольного рычага возникла в процессе работы над созданием упрощенной подвески для недорогих автомобилей. Основная особенность треугольного рычага в том, что он работает как в поперечном направлении, в котором он установлен, так и в продольном. Имея три точки крепления (две точки для крепления к кузову, одна для крепления к кулаку), рычаг может удерживать амортизационную стойку как в поперечном, так и в продольном направлении. Появление такой конструкции обеспечило возможность применения меньшего количества деталей в подвеске, сделав ее более дешевой. Именно поэтому независимая передняя подвеска на треугольных рычагах так популярна.Особенности эксплуатации рычагов подвески
В целом, рычаг подвески - неприхотливая и долговечная деталь, особенно, если он сделан из стали. Стальные рычаги, в отличие от легкосплавных, подходят для использования в течение нескольких циклов от ремонта до ремонта подвески. При ремонте рычага заменяют шаровую опору и сайлентблок (или два сайлентблока в случае с треугольным или простым продольным рычагом), а сама деталь отправляется на второй или третий срок службы. Легкосплавные же рычаги в большинстве случаев подлежат замене целиком, что увеличивает стоимость ремонта подвески, хотя и несколько упрощает его.Причиной выходя рычага из строй обычно являются два фактора: механическое воздействие и коррозия
Причиной выходя рычага из строй обычно являются два фактора: механическое воздействие (попадание в яму, ДТП), приводящее к деформации рычага, и коррозия, которая, кстати, легкосплавным рычагам не грозит.
Независимая подвеска передних колес
К атегория:
1Отечественные автомобили
Независимая подвеска передних колес
Современные легковые автомобили имеют независимую подвеску передних колес. Особенность такой подвески заключается в том, что оба передних колеса не связаны между собой жесткой балкой, а с помощью рычагов на пружинах подвешены независимо одно от другого к раме автомобиля или к подрамнику несущего кузова. Таким образом, толчки, получаемые одним колесом от неровностей дороги, не передаются на другое колесо. Независимая подвеска обладает рядом преимуществ: снижение массы неподрессоренных частей благодаря отсутствию балки передней оси; предотвращение появления синхронизированных колебаний передних колес; снижение крена кузова при наезде колеса на препятствие; уменьшение опасности бокового заноса.
Существует несколько разновидностей конструкций независимых подвесок. Наибольшее распространение получила пружинно-рычажная подвеска с поперечным качанием рычагов. В частности, такая подвеска применяется на автомобиле ГАЗ -24 «Волга», обеспечивая ему плавность и мягкость хода.
Устройство независимой передней подвески пружинно-рычажного типа показано на рис. 1.
Спиральная пружина, являющаяся упругим элементом подвески, опирается на нижние рычаги. Рычаги с помощью шарниров связаны с осью, жестко соединенной с поперечиной. Верхней опорой для пружины служит штампованная головка поперечины. Между пружиной и головкой размещена резиновая шайба с отбортовкой. Внутри пружины установлен телескопический амортизатор. Шток амортизатора верхним концом крепится через резиновые подушки к кронштейну, жестко закрепленному вместе с осью верхних рычагов на поперечине. Внизу в проушину амортизатора запрессован резиновый шарнир, ось которого прикреплена двумя болтами к опорной чашке пружины.
Верхние и нижние рычаги подвески соединены между собой стойкой к которой с помощью шкворня крепится поворотная цапфа. Стойка связана с верхними и нижними рычагами пальцами с резьбовыми втулками
При наезде переднего колеса на препятствие нижний рычаг поднимается и сжимает пружину, воспринимающую часть массы автомобиля, приходящуюся на данное колесо.
Рис. 1. Независимая рычажно-пружинная подвеска автомобиля ГАЗ -24 «Волга»: 1 - пружина, 2 - нижний рычаг,- шарниры, 4 - ось, 5 - амортизатор, 6 - стабилизатор поперечной устойчивости, 7, 9 - резиновые подушки, 8 - стойка стабилизатора, 10 - поворотная цапфа, 11 - стойка передней подвески
При независимой передней подвеске устанавливают торсионный стабилизатор поперечной устойчивости. Если при боковом, крене кузова увеличивается нагрузка на одну сторону подвески, то стержень стабилизатора, работая на скручивание, стремится выровнять положение кузова. Показанный на рис. 11 стабилизатор поперечной устойчивости установлен на стойках, закрепленных в резиновых подушках на правом и левом нижних рычагах подвески.
У более новых моделей легковых автомобилей (ВАЗ -2101, BA3-2103, «Москвич-1500» и др.) применяется бесшкворневая рычажно-пружинная подвеска. При такой схеме цапфа колеса объединена с поворотной стойкой, которая при помощи шаровых шарниров крепится к нижнему и верхнему рычагам подвески. Шарниры хорошо предохранены грязезащитными чехлами от попадания в них пыли и влаги. Внутренней стороной нижние рычаги соединены с поперечиной подвески осью, заключенной в резинометаллические втулки (сайлент-блоки), запрессованные в отверстия рычагов и затянутые гайками по обоим резьбовым концам оси.
Такое же крепление применено и для соединения внутренних концов верхних рычагов с несущей частью кузова Цилиндрические пружины опираются внизу на качающиеся нижние рычаги, а вверху входят в стальные штампованные чашки с изолирующими резиновыми прокладками, упирающимися в опоры стоек.
Телескопический амортизатор, установленный внутри пружины, крепится в верхней части к кузову при помощи штока, имеющего на конце резьбу, а в нижней части к качающемуся рычагу посредством проушины на корпусе амортизатора, через которую пропущена ось. Как вверху, так и внизу применены резиновые втулки.
Во всех соединениях передней подвески автомобилей ВАЗ отсутствуют точки шприце-вой смазки благодаря тому, что в шарнирах заложен постоянный запас консистентной смазки.
Бесшкворневая подвеска проще по конструкции и имеет меньшую массу неподрессо-ренных частей по сравнению с подвеской шкворневого типа. Следует, однако, иметь в виду, что бесшкворневая подвеска требует более частой проверки углов установки передних колес, которые могут быть нарушены под влиянием случайных факторов.
К атегория: - 1Отечественные автомобили